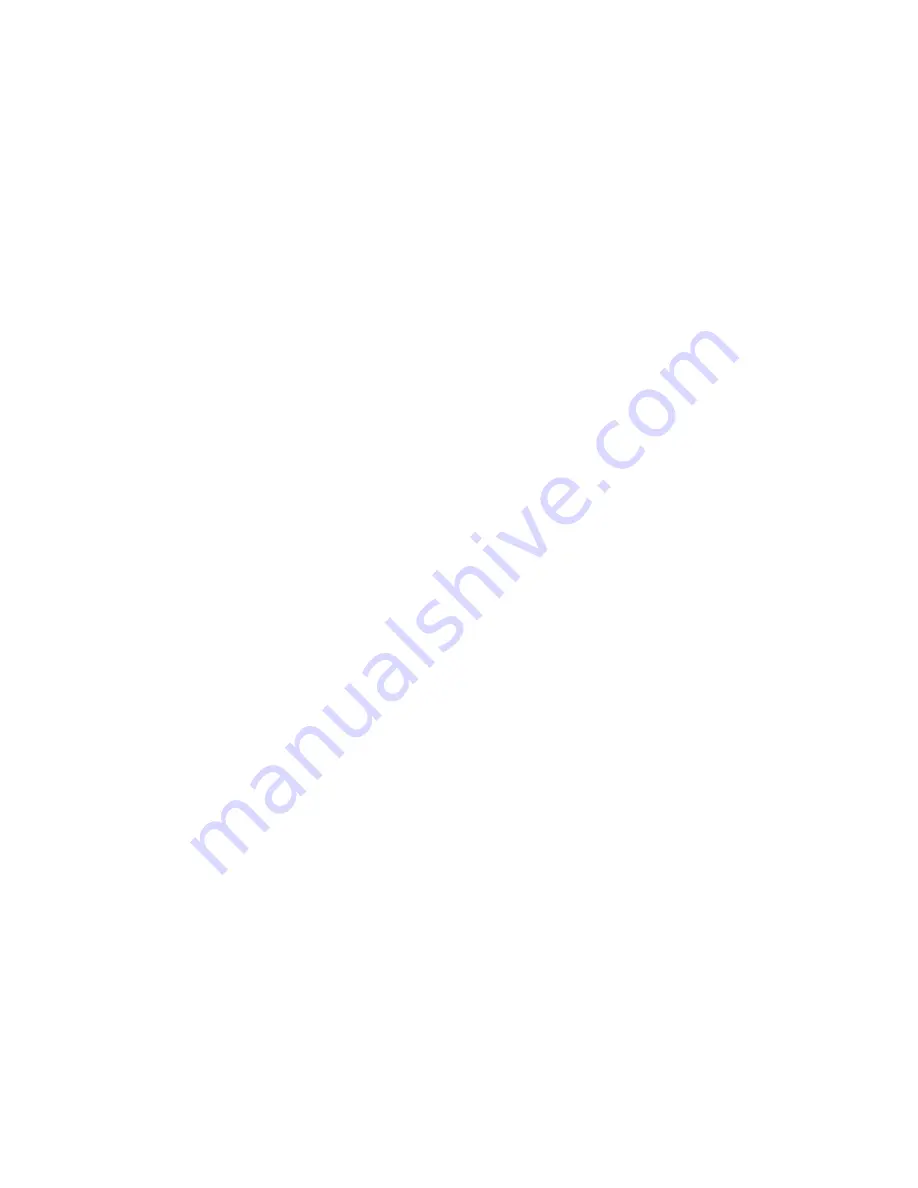
6
Figures:
Figure 1 - Lockable Handle .......................................................................................................... 23
Figure 2 - RQ Series Orientation .................................................................................................. 27
Figure 3 - RQ Cabinet Standard and Power Exhaust Gasket Locations ....................................... 29
Figure 4 - Forklifting an RQ Series Unit from the Side ............................................................... 30
Figure 5 - Forklifting an RQ Series Unit from the Front .............................................................. 30
Figure 6 - Lifting Details of a 2-6 ton Standard or Power Exhaust Unit ...................................... 31
Figure 7 - Lifting Details of a 2-6 ton Energy Recovery Wheel Unit .......................................... 31
Figure 8 - Vertical Duct Connection ............................................................................................. 32
Figure 9 - Solid Bottom Seismic Curb with Filters ...................................................................... 33
Figure 10 - Seismic Solid Bottom Curb without Filters Cross Section ........................................ 34
Figure 11 - Seismic Solid Bottom Curb without Filters Detail A................................................. 34
Figure 12 - Seismic Solid Bottom Curb without Filters Detail B ................................................. 34
Figure 13 - Seismic Rigid Mount Curb Cross Section ................................................................. 35
Figure 14 - Horizontal duct connections ....................................................................................... 35
Figure 15 - RQ Series unit Closed Rain Hood .............................................................................. 36
Figure 16 - RQ Series unit Open Rain Hood ................................................................................ 36
Figure 17 - Rain Hood with Metal Mesh Filter Rack Installation ................................................ 36
Figure 18 - Unit Base Utility Entry............................................................................................... 37
Figure 19 - Back View of Power Switch from Control Compartment ......................................... 37
Figure 20 - RQ Series Gas Heat Exchanger .................................................................................. 40
Figure 21 - Example 2-6 ton through the Base Gas Piping .......................................................... 43
Figure 22 - Post Corner Hole Location ......................................................................................... 49
Figure 23 - Post Back Hole Location ............................................................................................ 49
Figure 24 - Post Corner Hole Piping............................................................................................. 50
Figure 25 - Post Back Hole Piping ............................................................................................... 50
Figure 26 - Preheat Controller ...................................................................................................... 52
Figure 27 - Gas Heater Instructions .............................................................................................. 67
Figure 28 - PIN Connectors on EC Supply Fan Motor Electronics .............................................. 68
Figure 29 - Gas Heat Exchanger ................................................................................................... 76
Figure 30 - Removal of a Condenser Fan Assembly .................................................................... 76
Figure 31 - Evaporator Coil Access .............................................................................................. 77
Figure 32 - 2-6 ton Supply Fan ..................................................................................................... 81
Figure 33 - RQ Supply Fan Removal Bolts .................................................................................. 81
Figure 34 - RQ Supply Fan Removal Slide .................................................................................. 82
Figure 35 - Variable Capacity Compressor Controller ................................................................. 84
Figure 36 - Compressor Controller Flash Code Details................................................................ 85
Figure 37 - RQ Series 2-6 ton Standard Filter Layout .................................................................. 86
Summary of Contents for RQ SERIES
Page 2: ......
Page 29: ...29 Figure 3 RQ Cabinet Standard and Power Exhaust Gasket Locations ...
Page 43: ...43 Figure 21 Example 2 6 ton through the Base Gas Piping ...
Page 49: ...49 Figure 22 Post Corner Hole Location Figure 23 Post Back Hole Location ...
Page 50: ...50 Figure 24 Post Corner Hole Piping Figure 25 Post Back Hole Piping ...
Page 67: ...67 Gas Heater Instructions Figure 27 Gas Heater Instructions ...
Page 97: ......
Page 98: ......
Page 99: ......