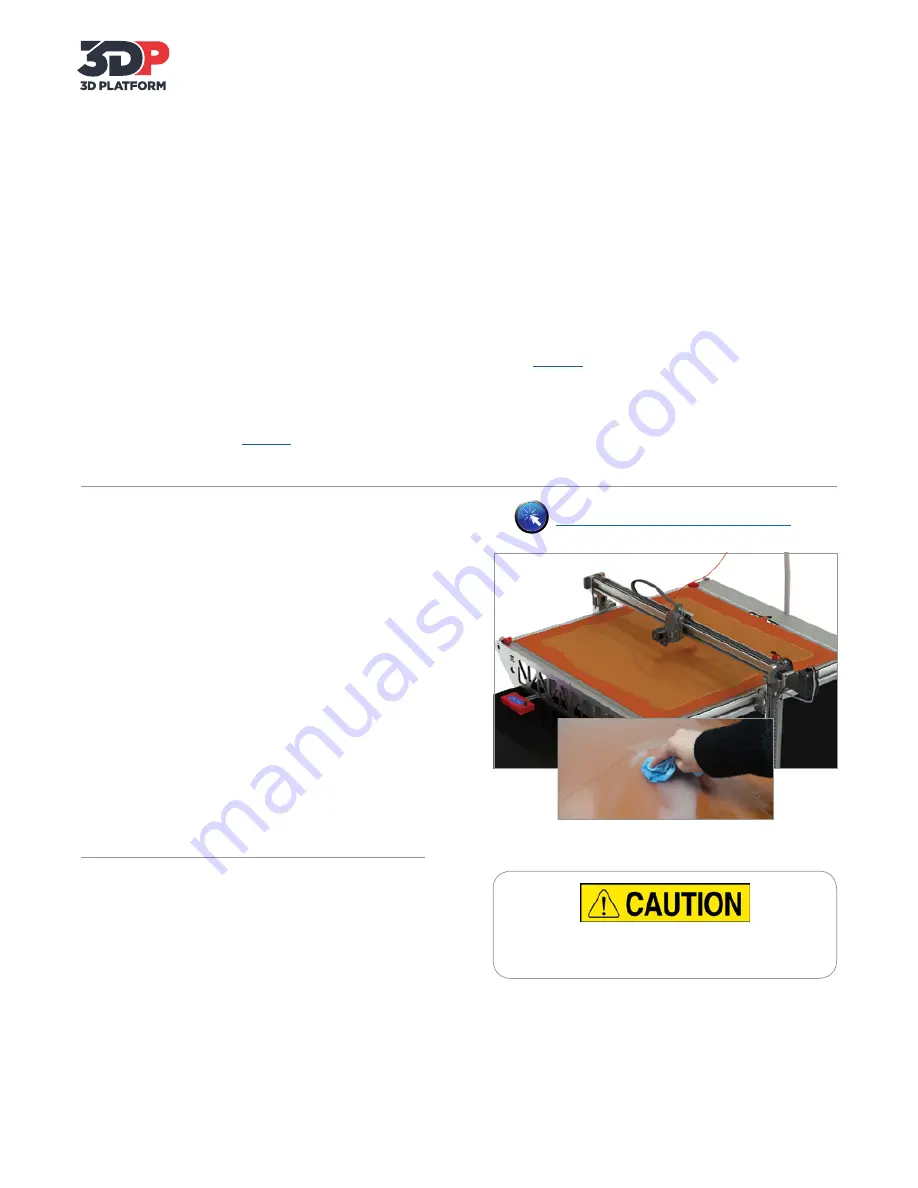
18
| www.3DPlatform.com
Original Instructions 2015
Care and Maintenance
PREPARE THE PRINT BED
Prepare the build area for printing. In order for your
prints to adhere to the borosilicate glass—it needs to
be clear of debris but somewhat tacky. We have found
that using a sugary substance, such as beer, works quite
well. Pour a liberal amount onto the build area and wipe
as if you were cleaning with glass cleaner. Cover the
entire area that your print will touch. Repeat this process
between prints to remove filament particles and other
debris, as well as prepare the bed for the next print.
This is not the only method available. Other suggestions
include: painter's tape, glue stick, and hairspray.
Do not use glass cleaner or alcohol on the glass. Doing
so will make adhesion very difficult.
MAINTENANCE
For the safety of the user and to avoid shock or
unintended motion, all maintenance of the 3DP1000
3D printer should be:
• Conducted with the machine unplugged from all
electrical outlets.
• Conducted when the machine is cool.
Exception: maintenance and replacement of the extruder
nozzles must be done when the extruder is heated. Use
extreme caution when maintaining or operating heated
machinery. See details—Cleaning the Nozzle and
Changing the Nozzle—on
page 19
.
For the safety of the user, use extreme caution when
working with heated machinery.
Link to article: Perfecting the First Layer
CLEARING THE HOB
For machines sold prior to 12/4/15, this process can
be used to clear the hob mechanism. It is best practice
to use a metal pick to clean the grooves in the feeding
mechanism in the extruder—called the hob. In time—
especially long prints—filament particles may fill the
gripping crevices in the hob and create filament feeding
issues.
Tip: If your filament is not feeding smoothly, try clearing
the hob.
SIMO® Series actuators from PBC Linear®:
• Rail and bearing system is inclusive of internal
lubrication system—requiring no preventative
maintenance—for the lifetime of the machine.
• Teflon coated screw, with engineered polymer nut
is designed for lifetime operation under normal
operating conditions—see Work Environment
on
page 10
.
• Cam Roller carriages include built-in micro-polymer
lubricators. If lubricators become damaged, contact
manufacturer for replacement.