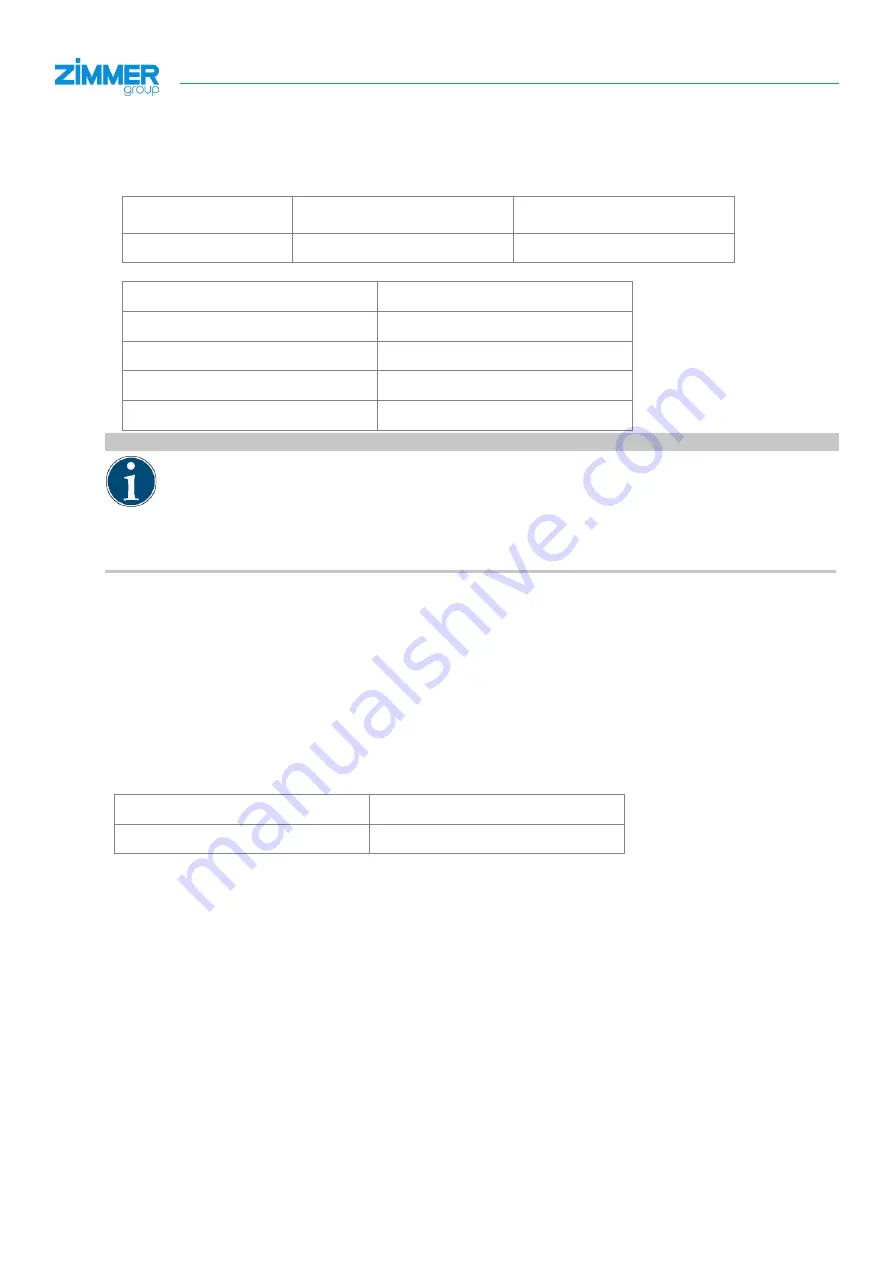
22
DDOC00270 / f
EN / 2020-03-31
Zimmer GmbH
●
Im Salmenkopf 5
●
77866 Rheinau, Germany
●
+49 7844 9138 0
●
+49 7844 9138 80
●
www.zimmer-group.com
INSTALLATION AND OPERATING INSTRUCTIONS:
2-jaw angular grippers, electric/pneumatic, HRC-05 series
8.3.8 “ActualPosition” parameter
The parameter "ActualPosition" corresponds to the current position of the gripper jaws relative to the full stroke.
The value is specified with a resolution of 0.01 mm.
The values can move between the "BasePosition" (minimum values) and the "WorkPosition" (maximum values).
By means of the position measuring system, it is possible to achieve a position accuracy of +/- 0.05 mm.
Product
“BasePosition” (minimum
value)
“WorkPosition” (maximum
value)
HRC-05-xxx
0
2000
Name
"ActualPosition"
Data format
UINT16
Permission
Read
Transfer
Cyclical
Value range
0 to max. jaw stroke of the gripper
INFORMATION:
The "StatusWord" of the gripper should be used to check whether a workpiece has been gripped correct-
ly.
Ö
The position measurement resolution is: 0.01 mm
Ö
The position measurement accuracy is: 0.1 mm
If the "ActualPosition" parameter is used for detecting the workpiece, then fluctuations around the exact
value must be taken into consideration during commissioning!
8.4 "Cold boot"
For proper function, we recommend that the actuator and sensor voltage be supplied with power separately.
Pins 1 and 3 are intended for the sensor power supply and must be switched on first.
Once the gripper is able to communicate with the PLC, the supply voltage can then be activated via pins 2 and 5.
Please note:
If pin 1 is disconnected, pin 4 (IO-Link) must also be disconnected.
8.5 Minimum travel path
The gripper requires a certain "minimum travel path" to accelerate to the desired gripping force.
This minimum travel path depends on:
• The desired gripping force
•
The dimensions of the gripper fingers
Model
Minimum travel path
HRC-05-xxx
0.5 mm per gripper jaw