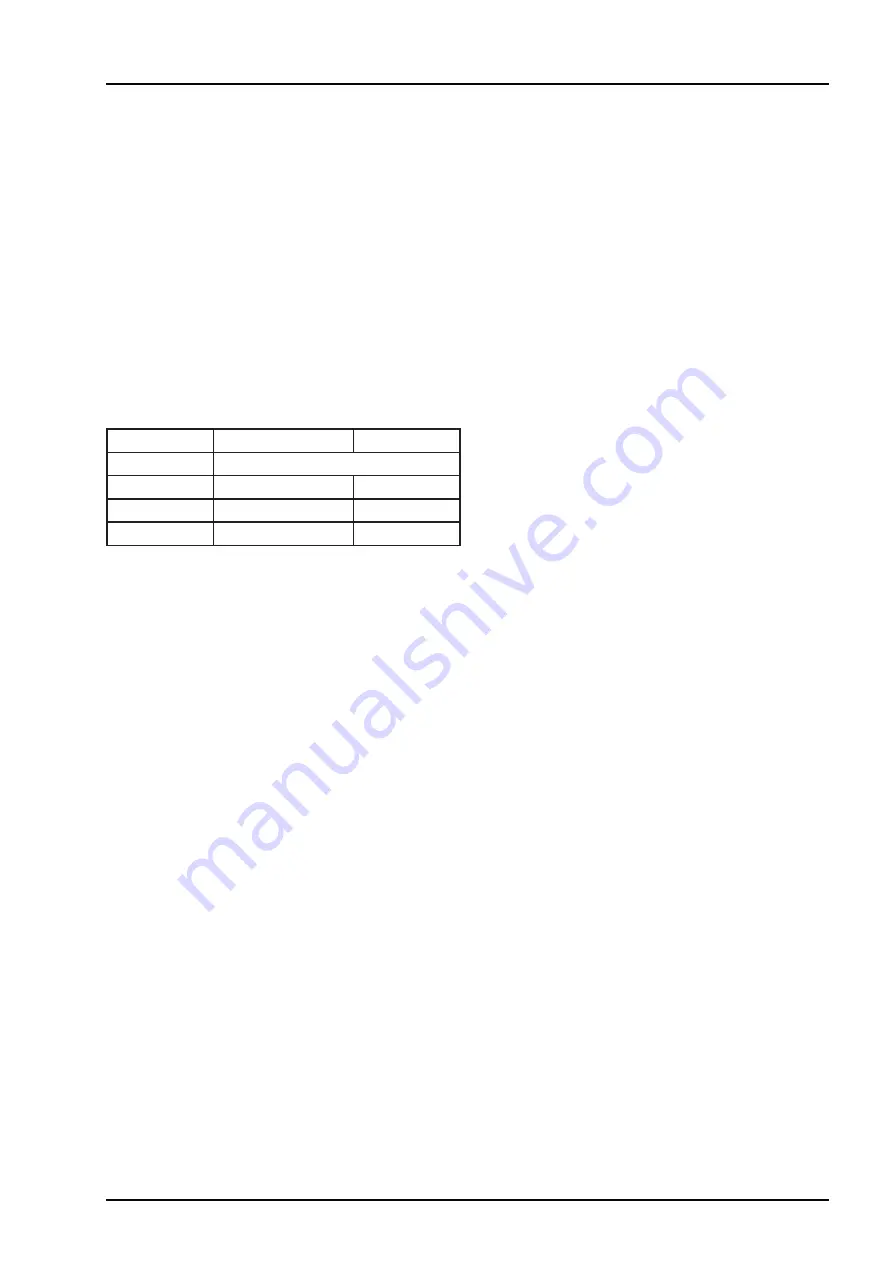
ZT MK2
Testing and verification
49
www.zepro.com
11.2 Dynamic load test.
11.2.1
Test with max. load
Place a test load on the platform according to the table (for the respective tail lift model/lifting capacity).
Check that the lift operates correctly in the normal range of movement, i.e. up, down, tilting at ground level
and tilting at vehicle floor level.
11.2.2
Test with overload
Place a test load on the platform according to the table (for the respective tail lift model/lifting capacity). The
test load should be 1.25 x the lift model’s max. load. Verify that the tail lift cannot lift the load when the up
function is switched on (it may however be possible to tilt up the load).
Dynamic load (Test load 1.0 x tail lift loading capacity). For tail lifts with load centre of 750 mm
Capacity
Load 1000 kg
Load 1500 kg
Distance on platform (L)
1500 kg
1125 mm
750 mm
2000 kg
1500 mm
1000 mm
2500 kg
1875 mm
1250 mm
11.3
Test of safety functions
The tail lift functions must be tested.
Check:
• That the red light in the driver’s cab turns off when the platform is in transport position and that it turns on
when the platform is run out.
• That the tail lift cannot be activated if the cabin switch is in the off position.
• That the tail lift cannot be activated when the main switch fuse is removed.
•
That the overflow valve is activated when the lift is operated up to the vehicle floor level or end stops.
• That the tail lift cannot be lowered or tilted down if the electrical connector from the electric hose rupture
valves is disconnected from the lift and tilting cylinders respectively.
• That there is a “max. load” marking on the platform and it is correctly positioned according to the loading
diagram for the tail lift model concerned.
•
That warning flags and reflectors are fitted and fulfil their function correctly.
•
That all safety and operating stickers are affixed in their respective positions.
• That the platform’s mechanical lock is functioning correctly (where applicable).
• That the instructions for using the tail lift have been left in the driver’s cab.
• That the CE declaration of conformity has been completed.