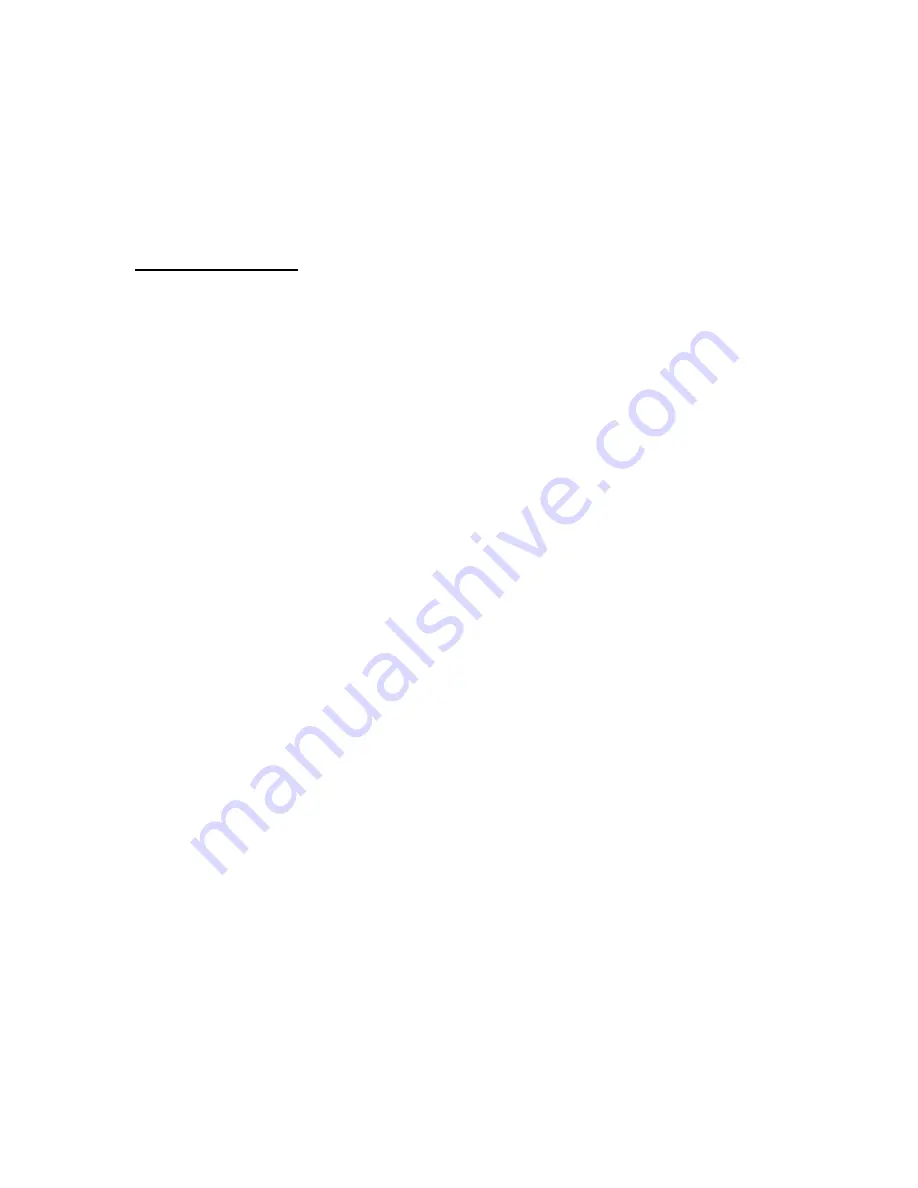
Z810
System
User
Manual
Z
Corporation
Z Corporation Service (781) 852-5050 / (887) 88-ZCORP
75
The instructions below are specific to molds produced on Z Corporation Printers. It is assumed
that the user currently owns a thermoforming system and is familiar with using molds created
from other techniques for creating thermoformed parts.
The process for making molds is straightforward. Good design of the molds will be the first and
most important step in the process.
Design Considerations
1. Material – Plaster
2. Thickness - Capital equipment (presses) will vary from plant to plant. The optimum thickness
(minimum material use = minimum cost) for the mold will vary as well, but we recommend
beginning with a minimum thickness of 1.5” (38 mm).
3. Printing the small size holes needed for the vacuum is unrealistic. The tool designer may
place ‘guide’ holes or marks in the part to act as guides for drilling, but the process will
require the use of a mechanical drill to fully incorporate the hole into the mold. Drill diameters
should be the same as used when creating molds from aluminum or other non-permeable
materials.
4. Drying – the molds will need approximately four hours minimum of drying time at 150
o
F
(66
o
C) to maintain a usable strength.
5. It is often useful to use STL editing features to improve the accuracy of the final mold. If
using the Magics RP software for STL file editing, read the help section regarding the offset
function. In summary:
a. For applying correction to the part on flat faces of the block, use the Extrude
command on each face. For the faces of the part that have curved features, use the
offset command.
6. Resin
a. Epoxy resin works best in terms of speed, ease of use, and strength.
7. Sanding is optional – some users are satisfied with the surface finish as is.
8. Usage life - Individual molds have consistently produced 10-20 parts successfully without the
use of a release agent.