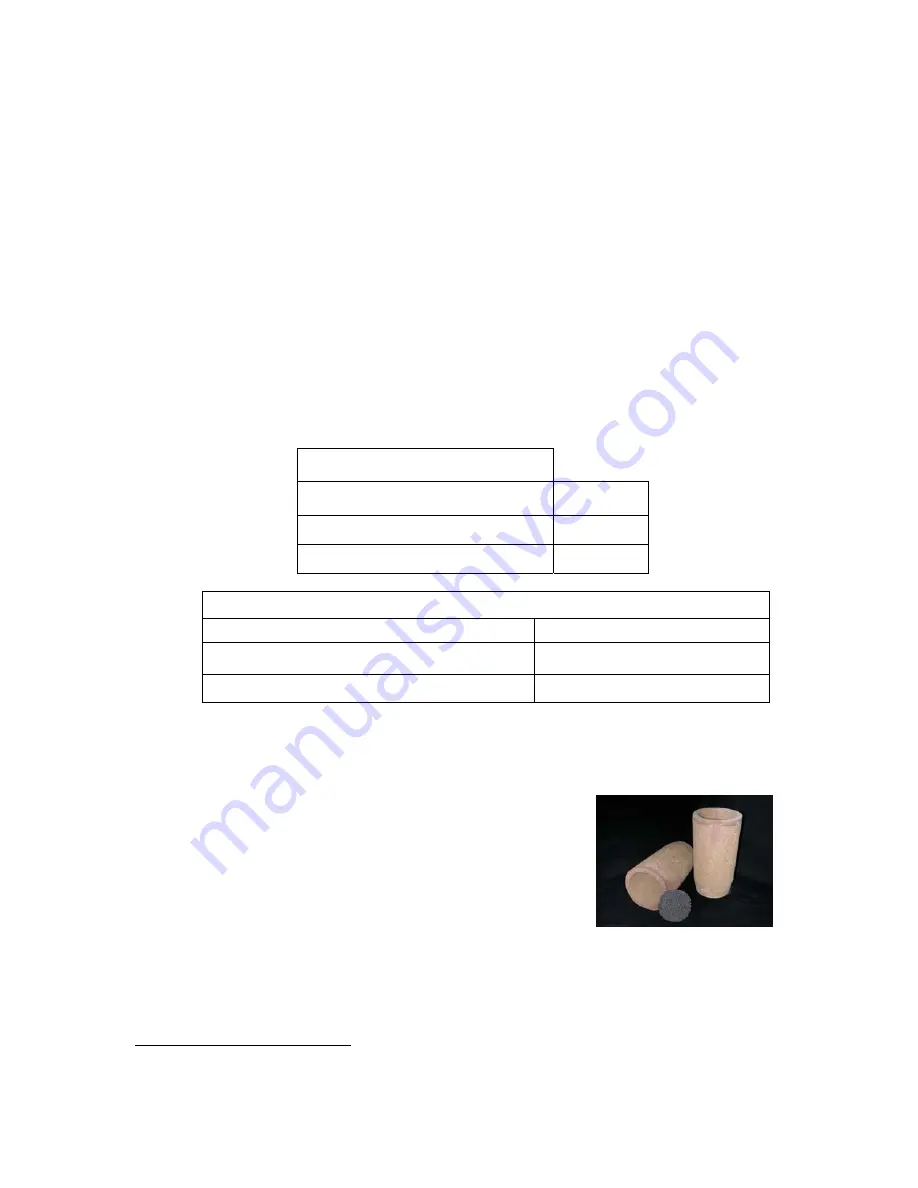
Appendix I
ZCast Design Guide - 19
•
Using “Bleed Compensation” is recommended. This will improve the accuracy so parts
will fit together better
3
.
•
Orient parts so that the most critical faces are facing up in the build. For example, when
possible, put the outside of the mold components (non-molding surfaces) facing down in
the build. Under certain conditions, a slight arching
4
effect can occur on the bottom
surfaces in the build. This will not affect the rest of the part, so putting non-critical
surfaces down will eliminate any risk.
•
When cores are being printed, you may choose to build a fixture underneath it. This will
improve the accuracy for critical fit items. Refer to the ZPrint Manual for instructions on
using fixtures.
•
For mating parts (such as a cope and drag of the same mold), try to always print them in
the same orientation in the build.
6.13.1 Machine Settings
Use the following optimized print settings for printing ZCast 500 powder with zb56 binder:
Saturation Settings
Shell 1.4
Core 0.7
Layer Thickness
0.004”
Bleed Compensation Settings
X 0.018
Y 0.018
Z 0.018
6.14 Degassing and Filtering Metal
To help achieve improved part quality, steps should be taken to
properly prepare the metal for pouring. Two typical foundry
practices are degassing and filtering. When properly taken,
these steps help to yield quality parts in any foundry.
Filters can be added directly to the mold. This can be
accomplished by strategically locating filters within the drag
assembly as shown in figure 13. Design slots or shelves in the
drag for filter placement. Other options include using foundry
consumables with ceramic inserts as shown in figure 12.
Accumulated slag on the top of the crucible should be removed prior to pouring.
3
See Table 1
4
See Figure 8
Table 1
Figure 12: Refractory sleeves
and filters