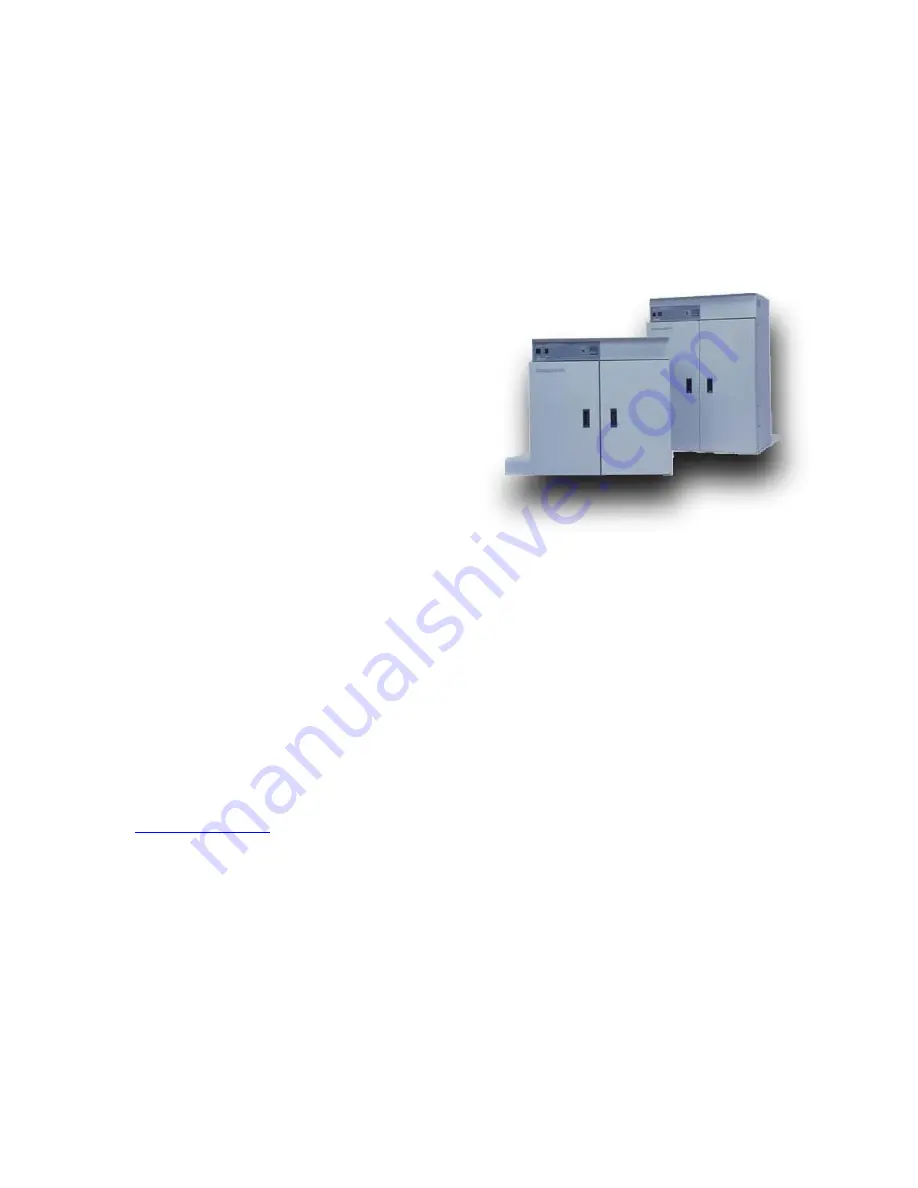
Appendix I
ZCast Design Guide - 23
9.3 Powder
Recycling
Unprinted ZCast material can be recycled. Z Corp. recommends that you add approximately 30%
new powder with recycled powder.
10 Finishing
10.1 De-molding
Removing a casting from a ZCast mold is virtually
identical in process to the removal of a casting
from a traditional chemically set sand mold. After
cooling and solidifying, the mold can be
unclamped and broken apart. Breaking a mold
can usually be done with a hammer or other blunt
object. Once the majority of the mold material has
been broken off, the cores and detailed sections
can be cleaned out with a high-pressure water jet
or by simply breaking them apart with a tool (a
simple screwdriver will work well). All sand
casting foundries will be set up with the means to
remove ZCast material from a finished casting.
10.2 Secondary Operations
Castings will often need secondary operations, all of which are
identical
in process to traditionally
cast parts. At the very least, the material formed in the gating system will need to cut off. The
flashing will probably need to be ground off. Machining may need to be done on critical surfaces
(remember to add machining stock (typically around .080” (2mm)). Holes may need to be drilled
out and tapped. The surface may be bead blasted or sand blasted. Castings may be heat-
treated.
10.3 Ovens
You can bake your parts in one of the ovens offered through Z Corporation, or any other oven
that will reach temperatures up to 400
º
F. Since ZCast molds will tend to smoke when baking, it is
a
requirement
to ensure that your oven is properly vented to the atmosphere. For more
information about the ovens offered through Z Corp. contact your local representative or go to
http://despatch.com/
on the web.
Figure 14: Despatch baking ovens
offered through Z Corporation