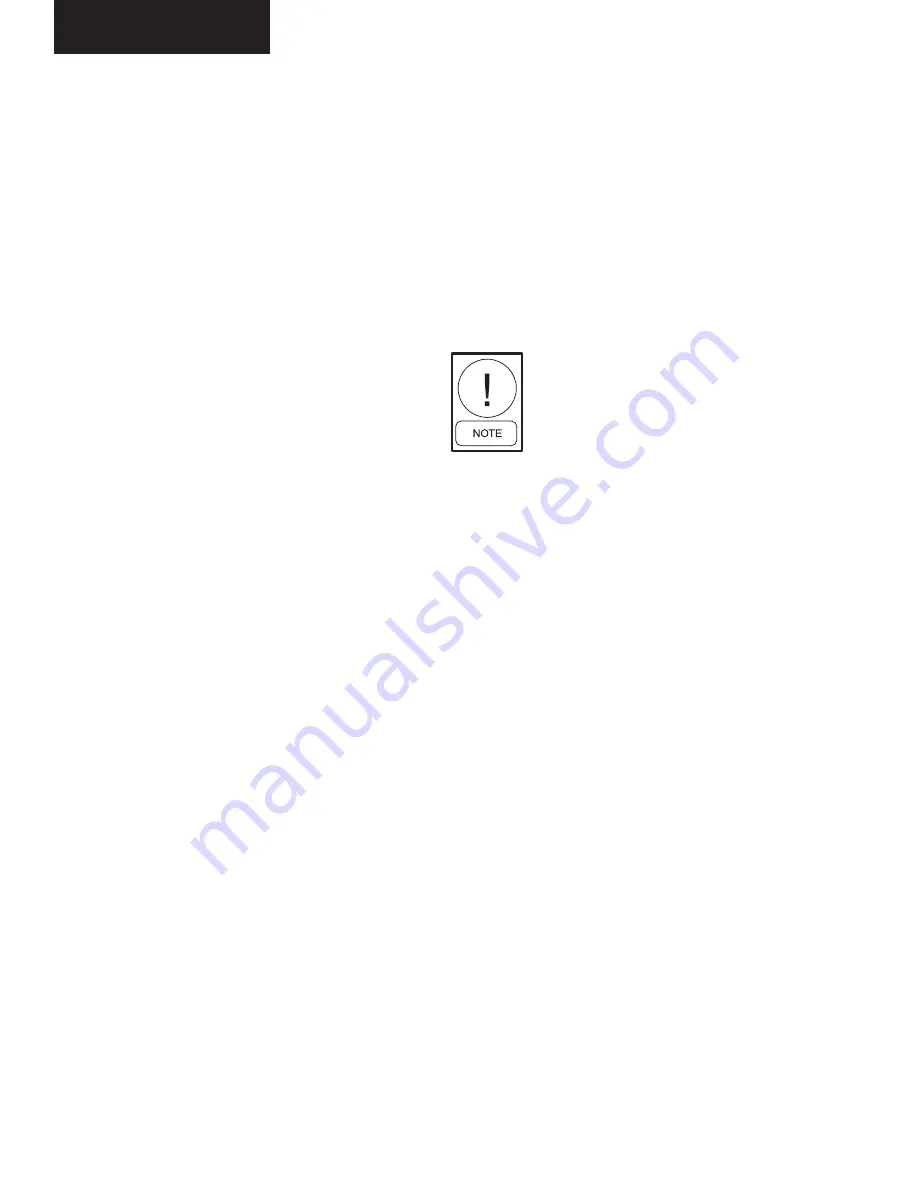
22
YORK INTERNATIONAL
FORM 150.52-NM2 (1001)
KEYPAD CONTROLS
Display
Parameters are displayed in Metric (°C and Bar) units
or, English (°F and PSIG) and for each circuit, the fol-
lowing items can be displayed:
• Return and leaving chilled liquid, and ambient tem-
perature.
• Day, date and time. Daily start/stop times. Holiday
and Manual Override status.
• Compressor operating hours and starts. Automatic
or manual lead/lag. Lead compressor identification.
• Run permissive status. No cooling load condition.
Compressor run status.
• Anti-recycle timer and anti-coincident start timer
status per compressor.
• System suction (and suction superheat), discharge,
and oil pressures and temperatures.
• Percent full load compressor motor current per
phase and average per phase. Compressor capac-
ity control valve input steps.
• Cutout status and set-points for: supply fluid tem-
perature, low suction pressure, high discharge pres-
sure and temperature, high oil temperature, low and
high ambient, phase rotation safety, and low leaving
liquid temperature.
• Unloading limit setpoints for high discharge pres-
sure and compressor motor current.
• Liquid pull-down rate sensitivity (0.3°C to 2.8°C
[0.5°F to 5°F])/minute in 0.1° increments).
• Status of: evaporator heater, condenser fans, load
and unload timers, chilled water pump.
• “OUT OF RANGE” message.
• Up to 6 fault shut down conditions.
• The standard display language is English, with 4 other
languages available.
Entry – Used to enter Setpoint changes, cancel inputs,
advance day, and change AM/PM.
Setpoints – Used to enter chilled liquid temperature,
chilled liquid range, remote reset temperature range.
Clock – Used to set time, daily or holiday start/stop
schedule and manual override for servicing.
Print – Used to display or print operating data or sys-
tem fault shutdown history for last six faults, and soft-
ware version. Printouts through an RS-232 port via a
separate printer (by others).
Program
• Used for setting low leaving liquid temperature
cutout, 300-600 second anti-recycle timer, lag
compressor start time delay, average motor cur-
rent unload point, liquid temperature setpoint re-
set signal from YORK ISN or building automa-
tion system (by others), via:
• Pulse-Width Modulated (PWM) input for up to
22°C (40°F) total reset as standard.
• Optional Building Automation System Interface
input card for up to 22°C (40°F) reset using a
4-20mA, 0-10VDC input, or discrete reset input.
The standard Micro Panel can be di-
rectly connected to a YORK ISN Build-
ing Automation System via the standard
on-board RS485 communication port.
This Option also provides open system
compatibility with other communica-
tions networks (BACNET
TM
and
LONMARK
TM
) via interface through
standard on-board 485 or 232 port and
an external YorkTalk Translator.
ACCESSORIES AND OPTIONS
See Electrical Data on pages 57 through 63 for specific
voltage and options availability. Separate external branch
circuit protection and disconnecting means must be sup-
plied by others in accordance with applicable Local and
National codes. (Factory-mounted)
• Multiple Point Supply – Standard field power
wiring connection on all models is Multiple Point
Power Connection, which is provided in two sepa-
rate motor control center cabinets, located adjacent
to each other at one end of the chiller. Each cabinet
contains starter elements for one compressor and
its associated fan motor starters. Field provided
power supply circuits, with appropriate branch cir-
cuit protection, are connected to factory provided
Terminal Blocks located in the two separate com-
pressor motor control centers. Optional to the Ter-
minal Blocks are Non-Fused Disconnects with ex-
ternal, lockable handles, or Circuit Breakers with
external, lockable handles.
•
Signle-point Supply with Internal Branch
Breakers – These Optional configurations include
enclosure and either a unit mounted Terminal Block,
or a Non-Fused Disconnect Switch with external,
lockable handle (in compliance with Article 440-
Product Description