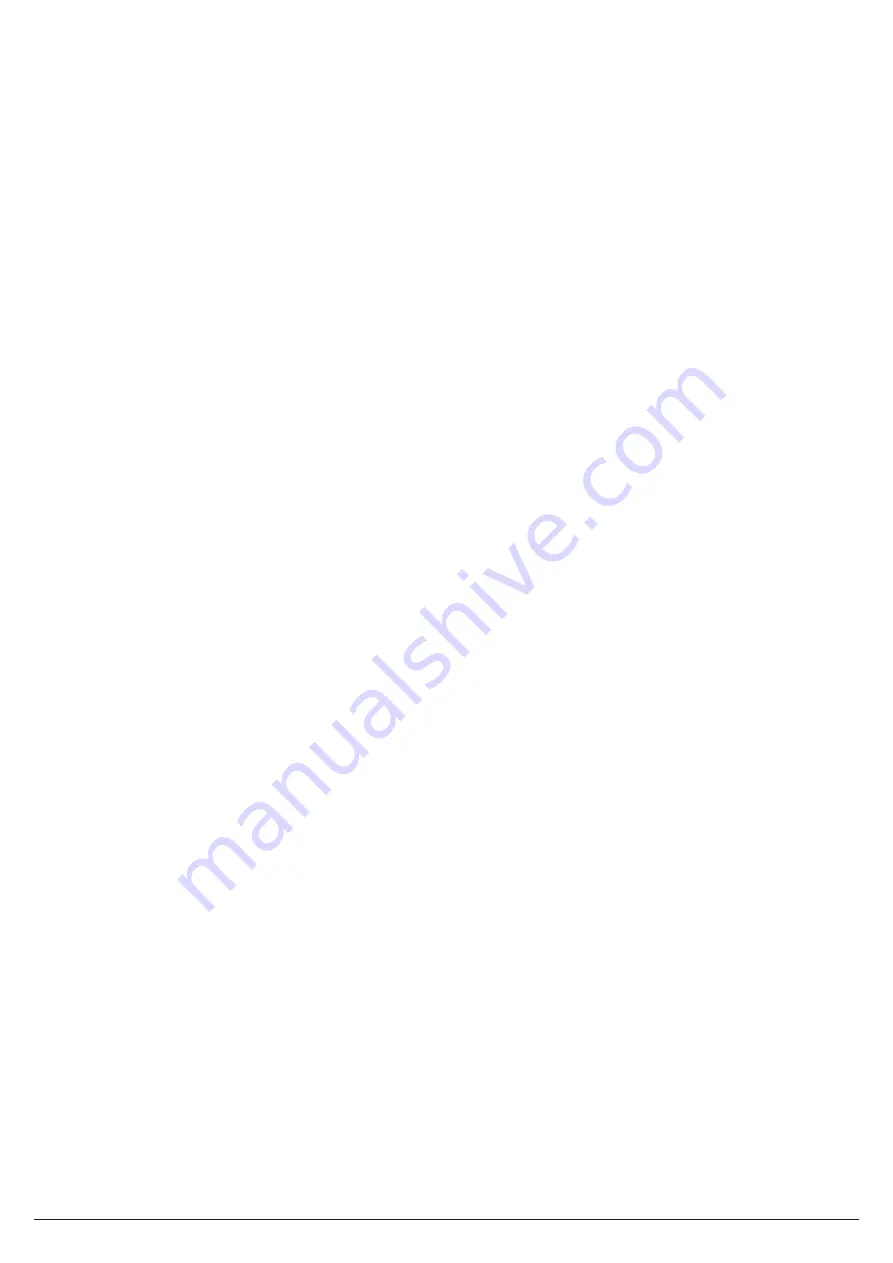
Yokogawa Electric Corporation - TC10 - ENGINEERING MANUAL - PAG. 17
On the contrary, when you want to decrease the temperature
from 250 to 230°C (
D
T = 20°C) using 100% of the cooling
power (fan), you will need 20 seconds only.
In our example the ratio is equal to 60/20 = 3 ([67] rcG = 3)
and it say that the efficiency of the cooling system is 3 time
more efficient of the heating one.
Available:
When two control action are programmed
(H.rEG and c.rEG) and [56] cont = PID and
[59] SELF = no.
Range:
0.01 to 99.99.
Note:
auto-tune functions calculate this value.
[68] tcc - Cycle time of the cooling output
Available:
When at least one output is programmed in order
to be the cooling output (c.rEG), [56] cont = PID
and [59] SELF = no.
Range:
1.0 to 130.0 seconds.
[69] rS - Manual reset (integral pre-load)
It allows to drastically reduce the undershoot due to a
hot restart. When your process is steady, the instrument
operates with a steady power output (e.g.: 30%).
If a short power down occurs, the process restarts with a
process variable close to the set point while the instrument
starts with an integral action equal to zero.
Setting a manual reset equal to the average power output (in our
example 30%) the instrument will start with a power output equal
to the value it will use at steady state (instead of zero) and the
undershoot will become very little (in theory equal to zero).
Available:
When [56] cont = PID.
Range:
-100.0 to +100.0%.
[72] od - Delay at power up
Available:
When at least one output is programmed as
control output.
Range:
oFF:
Function not used;
0.01 to 99.59 hh.mm.
Notes: 1.
This parameter defines the time during which
(after a power up) the instrument remains in stand
by mode before to start all other function (control,
alarms, program, etc.).
2.
When a program with
automatic start at power up
and
od function
are programmed, the instrument
performs od function before to start the program.
3.
When an auto-tune with
automatic start at power
up
and
od function
are programmed, the autotune
will start at the end of
od delay
.
[73] St.P - Maximum power output used during
soft start
Available:
When at least one output is programmed as
control output.
Range:
-100 to +100%.
Notes: 1.
When St.P parameter have a positive value, the
limit will be applied to the heating output(s) only.
2.
When St.P parameter have a negative value, the
limit will be applied to the cooling output(s) only.
3.
When a program with automatic start at power
up and soft start function are programmed, the
instrument performs the soft start and than the
program function.
4.
The auto-tune function will be performed after
soft start function.
5.
The Soft start function is available also when ON/
OFF contro l is used.
[74] SSt - Soft start time
Available:
When at least one output is programmed as
control output.
Range:
oFF = Function not used;
0.01 to 7.59 hh.mm;
inF =
Soft start always active.
[75] SS.tH - Threshold for soft start disabling
Available:
When at least one output is programmed as
control output.
Range:
-1999 to 9999 engineering units.
Notes: 1.
When the power limiter have a positive value (the
limit is applied to the heating action) the soft start
function will be aborted when the measured value
is greater or equal to SS.tH parameter.
2.
When the power limiter have a negative value
(the limit is applied to the cooling action) the soft
start function will be aborted when the measured
value is lower or equal to SS.tH parameter.
]
SP Group - Set point parameters
The SP group will be available only when at least one output
is programmed as control output (H.rEG or C.rEG).
[76] nSP - Number of used set points
Available:
When at least one output is programmed as
control output.
Range:
1 to 4.
Note:
When you change the value of this parameter, the
instrument operates as follows:
• [83] A.SP parameter will be forced to SP.
•
The instrument verifies that all used set point are
within the limits programmed by [77] SPLL and [78]
SPHL. If an SP is out of this range, the instrument
forces it to the maximum acceptable value
[77] SPLL - Minimum set point value
Available:
When at least one output is programmed as
control output.
Range:
From -1999 to [78] SPHL engineering units.
Notes: 1.
When you change the [77] SPLL value, the
instrument checks all local set points (SP, SP2,
SP3 and SP4 parameters) and all set points of the
program ([97] Pr.S1, [102] Pr.S2, [107] Pr.S3, [112]
Pr.S4 parameters). If an SP is out of this range, the
instrument forces it to the maximum acceptable value
2.
A [77] SPLL change produces the following actions:
• When [84] SP.rt = SP the remote set point will
be forced to be equal to the active set point
• When [84] SP.rt = trim the remote set point will
be forced to zero
• When [84] SP.rt = PErc the remote set point
will be forced to zero
[78] SPHL - Maximum set point value
Available:
When at least one output is programmed as
control output.
Range:
From [78] SPLL to 9999 engineering units.
Note:
For other details see [78] SPLL parameter.
[79] SP - Set Point 1
Available:
When at least one output is programmed as
control output.
Range:
From [77] SPLL to [78] SPHL engineering units.