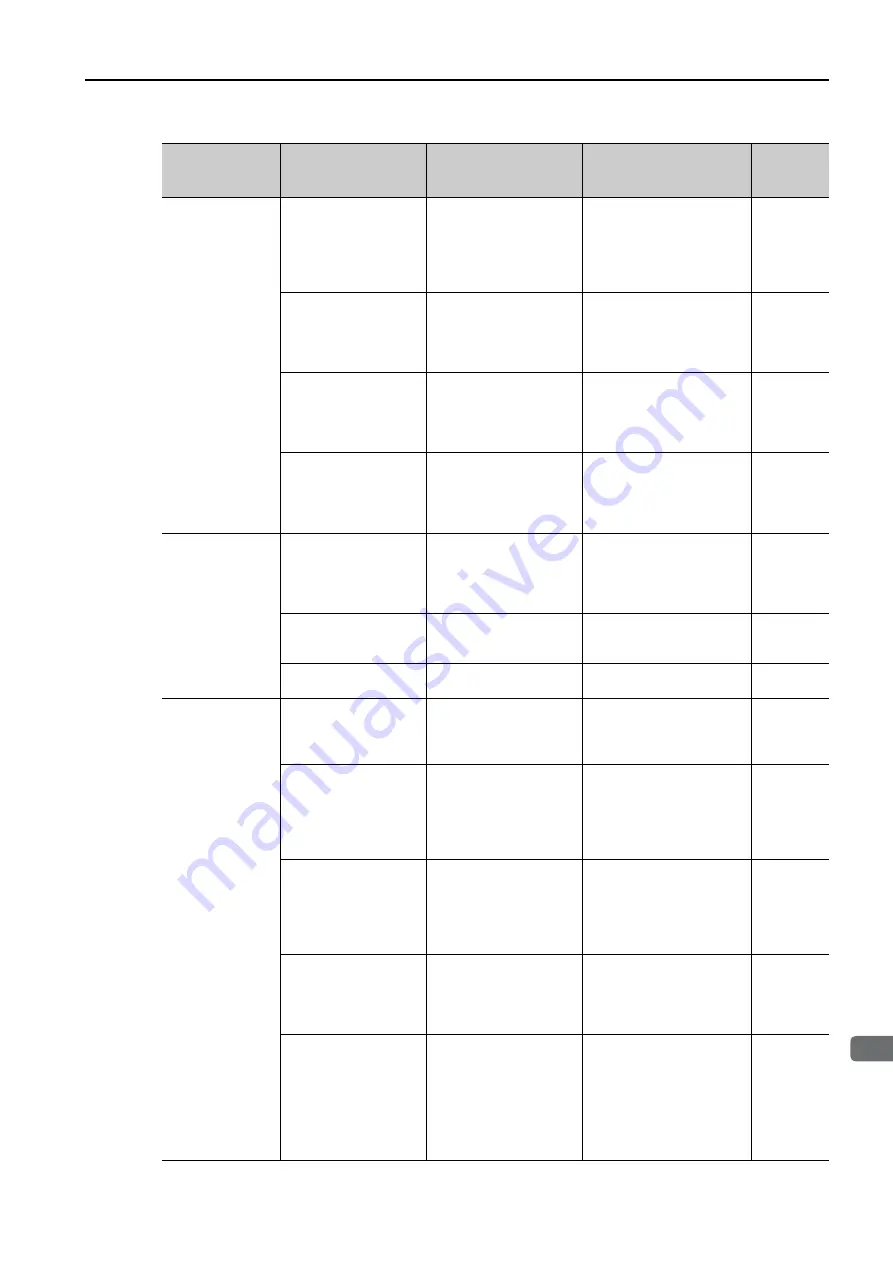
12.2 Alarm Displays
12.2.2 Troubleshooting Alarms
12-35
12
Maintenance
A.CF1:
Reception Failed
Error in Feed-
back Option
Module Commu-
nications
The cable between
the Serial Converter
Unit and SERVOPACK
is not wired correctly
or there is a faulty
contact.
Check the wiring of the
external encoder.
Correctly wire the cable
between the Serial Con-
verter Unit and SERVO-
PACK.
A specified cable is
not being used
between Serial Con-
verter Unit and SER-
VOPACK.
Check the wiring speci-
fications of the external
encoder.
Use a specified cable.
–
The cable between
the Serial Converter
Unit and SERVOPACK
is too long.
Measure the length of
the cable that connects
the Serial Converter
Unit.
The length of the cable
between the Serial Con-
verter Unit and SERVO-
PACK must be 20 m or
less.
–
The sheath on cable
between the Serial
Converter Unit and
SERVOPACK is bro-
ken.
Check the cable that
connects the Serial
Converter Unit.
Replace the cable
between the Serial Con-
verter Unit and SERVO-
PACK.
–
A.CF2:
Timer Stopped
Error in Feed-
back Option
Module Commu-
nications
Noise entered the
cable between the
Serial Converter Unit
and SERVOPACK.
–
Correct the wiring around
the Serial Converter Unit,
e.g., separate I/O signal
lines from the Main Circuit
Cables or ground.
–
A failure occurred in
the Serial Converter
Unit.
–
Replace the Serial Con-
verter Unit.
–
A failure occurred in
the SERVOPACK.
–
Replace the SERVO-
PACK.
–
A.d00:
Position Devia-
tion Overflow
(The setting of
Pn520 (Exces-
sive Position
Deviation Alarm
Level) was
exceeded by the
position devia-
tion while the
servo was ON.)
The Servomotor U, V,
and W wiring is not
correct.
Check the wiring of the
Servomotor’s Main Cir-
cuit Cables.
Make sure that there are
no faulty contacts in the
wiring for the Servomotor
and encoder.
–
The frequency of the
position reference
pulse is too high.
Reduce the reference
pulse frequency and try
operating the SERVO-
PACK.
Reduce the position refer-
ence pulse frequency or
the reference accelera-
tion rate, or reconsider
the electronic gear ratio.
The acceleration of
the position reference
is too high.
Reduce the reference
acceleration and try
operating the SERVO-
PACK.
Apply smoothing, i.e., by
using Pn216 (Position
Reference Acceleration/
Deceleration Time Con-
stant).
The setting of Pn520
(Excessive Position
Deviation Alarm Level)
is too low for the
operating conditions.
Check Pn520 (Exces-
sive Position Deviation
Alarm Level) to see if it
is set to an appropriate
value.
Optimize the setting of
Pn520.
A failure occurred in
the SERVOPACK.
–
Turn the power supply to
the SERVOPACK OFF and
ON again.
If an alarm still occurs, the
SERVOPACK may be
faulty.
Replace the SERVO-
PACK.
–
Continued from previous page.
Alarm Number:
Alarm Name
Possible Cause
Confirmation
Correction
Reference
for Correc-
tion