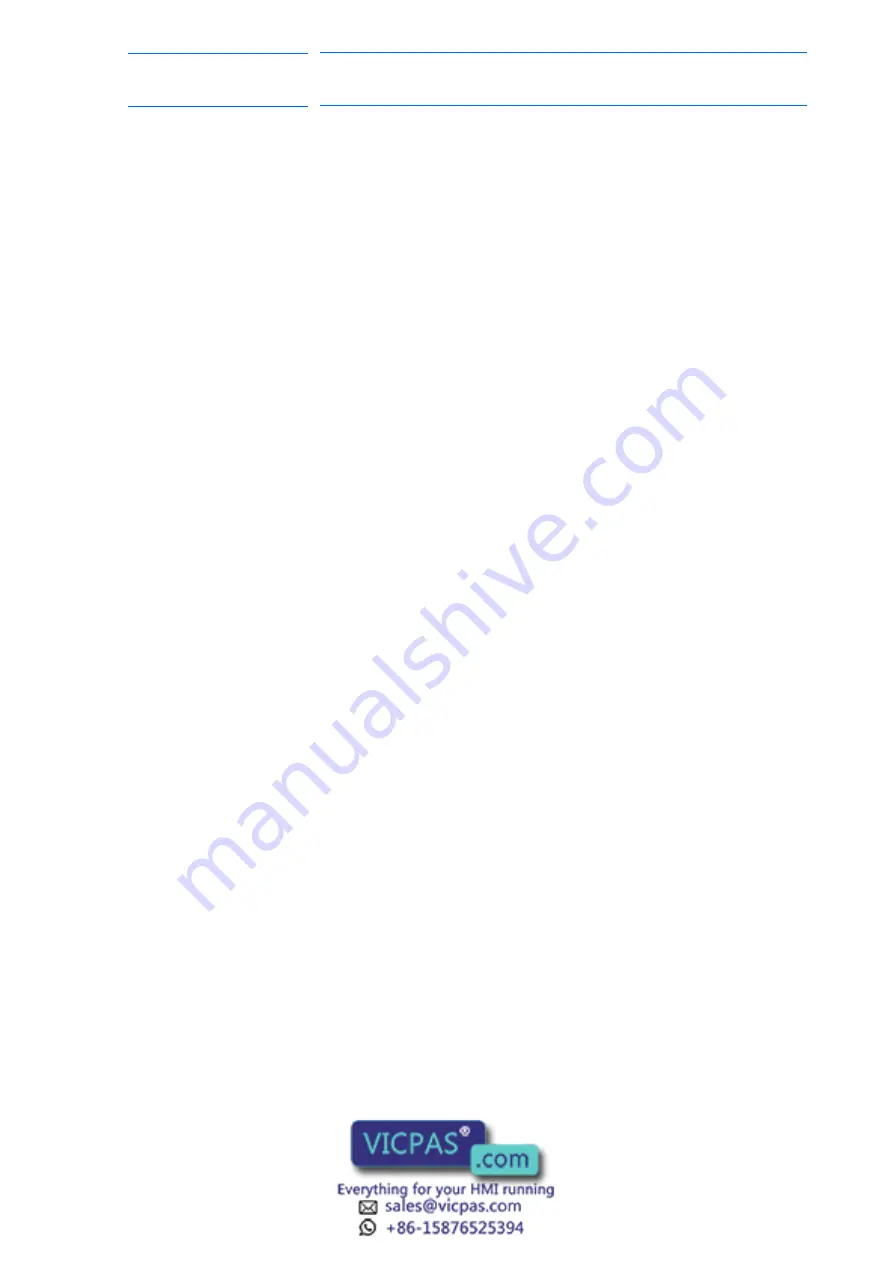
1-4
175932-1CD
175932-1CD
EcoTrim ET-1024 System
1 Introduction
1.2 System Overview
1.2.2 Major Components
The EcoTrim-1024 System includes the following major components:
• Motoman MH24 manipulator (robot)
• DX200 controller
• One MSR series rotary positioner
• One Programming Pendant (located on the DX200 controller)
• Operator Station
• Ultrasonic Trimming (Standard) or Hybrid (Optional) tool
• Safety equipment:
• Heavy gauge, wire-mesh safety fencing
• Dual-channel, interlocked safety light curtain system
• Dual-channel, interlocked work-cell entry doors
• Steel screen on the MSR rotary positioner
1.2.3 Theory of Operation and Safe Guarding
The DX200 EcoTrim-1024 cell is designed to accommodate a single
MH24 robot.
• EcoTrim-1024 - Single MH24 robot with MSR-355 positioner
or optional MSR-655.
The robot controller and Ultrasonic/Hybrid tool controls are located behind
the cell. Two sliding doors with safety interlocks allow access from either
side. The MH24 sits on a 610 mm raiser.
The standard servo driven MSR positioner provides either a 60 inch
(1500 mm) or optional 72 inch (1829 mm) H-Frame tabletop. The table
comes programmed for two reciprocating positions (Side A/Side B).
Based on the selected table, options are available for additional load
positions, rotary brushes, slip-rings and hard-stops.
The functional safety unit (FSU) is included in the controller for monitoring
the rotary table. Two FSU “Axis Range Limit” files monitor the table's
position (within 1 degree) to determine if the table is at “Side A” or “Side
B”. The status of these two “Axis Range Limit” files generate outputs
FSUOUT#1 (“Side A @ Robot”) and FSBOUT#2 (“Side B @ Robot”). The
controller outputs connect to the coils of two force-guided relays. The
contacts of these relays (At Side A and Side B), or with the light curtain's
“Clear” status to generate an element in the E-stop chain.
15 of 64