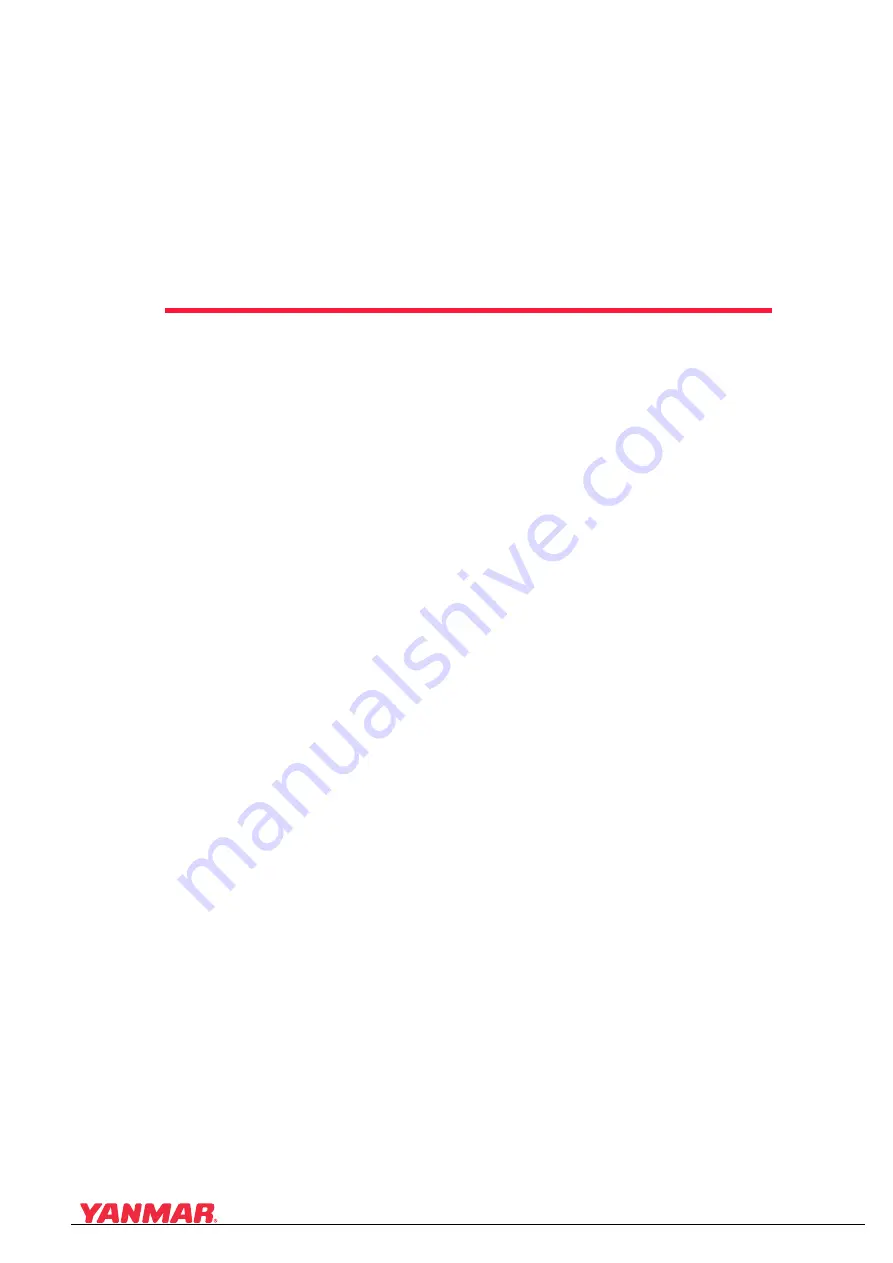
ZT350 Installation Manual
6-1
© 2007 Yanmar Marine International
ZT350 Installation Manual
Section 6
PRE-DELIVERY
Page
Pre-Delivery Preparation ................................................................. 6-2
Power Steering Fluid ................................................................. 6-2
Battery Connections .................................................................. 6-2
Check the Power Trim Pump Fluid............................................ 6-3
Fill the Power Trim Pump Fluid ................................................. 6-4
Check the Stern-Drive Oil Level ................................................ 6-4
Fill the Stern-Drive with Oil ........................................................ 6-5
Propeller Selection .................................................................... 6-6
General Propeller Installations .................................................. 6-7
Installing the Propellers ............................................................. 6-8
Removing the Propeller ............................................................. 6-9
Test Preparations .................................................................... 6-10
Engine Operation Tests........................................................... 6-10
Out-of-Water Testing ............................................................... 6-10
In-Water Testing ...................................................................... 6-11
Drive Unit Operational Tests ................................................... 6-11
Cold Weather (Freezing Temperature), Seasonal and
Extended Storage.................................................................... 6-13
Содержание ZT350 series
Страница 1: ...ZT350 series INSTALLATION MANUAL ZT350 Installation Manual P N 0FZTD G00100 STERN DRIVE ...
Страница 6: ...vi ZT350 Installation Manual 2007 Yanmar Marine International This Page Intentionally Left Blank ...
Страница 12: ...SAFETY 1 6 ZT350 Installation Manual 2007 Yanmar Marine International This Page Intentionally Left Blank ...