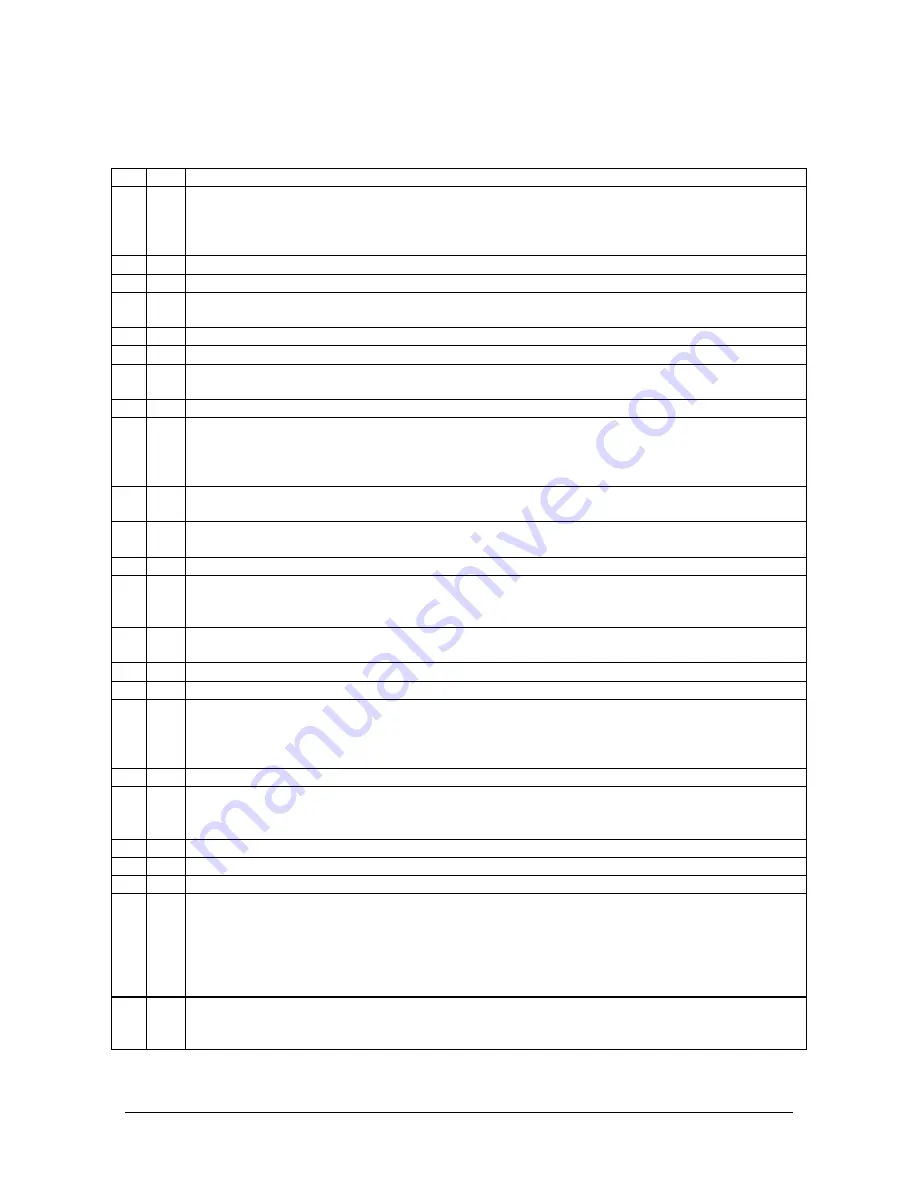
6
XYZ Machine Tools
ProTURN SLX 1630 ProtoTRAK SLX CNC Safety, Installation, Service & Parts List Manual
2.4 Installation Instructions & Checklist
Installer: Use this checklist to assure a complete set-up of the SLX 1630. * Items
checked before leaving the factory
1.
Shut off power to the machine.
2.
Visually inspect the 415V going into the electrical panel. Visually verify the wiring is correct per
our wiring diagram. Make sure a strain relief is being used where the wiring enters the cabinet.
Have the customer repair any wiring discrepancies. Note: Machine can only be wired for 415
VAC.
3.
Clean the machine if needed and remove any remaining grease.
4.
Mount the pendant on the bracket that is attached to the chip enclosure for the 1630.
5.
Make and check all the proper electrical connections from the pendant to the electric box. Be
sure to mount the cable cover to the left side of the pendant.
6.
Slide the doors back and forth to make sure they slide smoothly. Adjust as necessary.
7.
Remove the protective plastic covers from the headstock and the windows on the sliding doors.
8.
Turn on the power to the machine and to the pendant. Make sure that the 115-volt line is
plugged into the pendant.
9.
Check to make sure the coolant pump is rotating in the correct direction.
10.
Visually inspect the oil level through the site glass which is found under the rear spindle cover
and verify that the oil level is correct in the head stock prior to turning on the machine tool. Add
oil if necessary. Make a notation on the installation summary sheet if the oil level is incorrect.
For the 1630, oil will only be visible on the headstock site glass when the spindle is running.
11.
Manually override the automatic way oiler and pump oil to lubricate all sliding surfaces. This can
be done by running service code 300 a few times.
12.
Jog the saddle and cross slide back and forth until the way surfaces are well lubricated. Oil
should be visible on all the way surfaces.
13.
Position the saddle and tailstock to the center of the bed for leveling.
14.
Check the level of the machine. The machine should be level to within 0.02 mm longitudinally
and 0.01 mm transversely. Even though it is the responsibility of the customer, make any
adjustments if necessary (see section 2.9 Leveling).
15.
Check the tailstock and the tailstock barrel locks by locking and unlocking. Run the tailstock
barrel in and out to ensure proper function.
16.
Run the spindle at 500 rpm or so for 15 to 20 minutes in order to warm the headstock. *
17.
Run the spindle through it's various speeds.
18.
Open and close the doors and verify the door switches are functional. The control should
display a message of “DOOR OPEN” in DRO mode when the doors are open and it should
disappear when the doors are closed. Open and close the chuck guard and verify a message is
present on the screen and the spindle does not run with the chuck guard open.
19.
Make sure the X and Z electronic handwheels and jogstick are functional.
20.
Check to make sure that the E-Stop button on the pendant is functioning correctly. The 1630
only has an e-stop on the pendant. Undo the e-stop ad press the screen button on the right
side of the pendant to reset.
21.
Perform Service Code 12, Feed Forward Constant.*
22.
Perform Service Code 123 to calibrate the X and Z-axis using a 150mm standard. *
23.
Perform Service Code 127 and 128 to manually calculate the backlash for the X and Z-axis.*
24.
Check for positional accuracy and repeatability on the X and Z-axis using programs X LATHE
REPEAT.PT4 and Z LATHE REPEAT.PT4 respectively. Positioning and repeatability values should
be less than or = to 0.01 mm. Programs can be found on the parts program disk that comes
with each pendant. It may also be found in the PT4 folder followed by the SWI TEST
PROGRAMS folder if the customer ordered the Network/Memory software option. Note: the
doors must be closed to run these programs.*
25.
Perform Service Code 100 in both directions for the X and Z-axis to verify that the feed rate
shown on the display is at least 4572 mm/min (180 ipm) for Z and 3048 mm/min (120 ipm) for
X.*