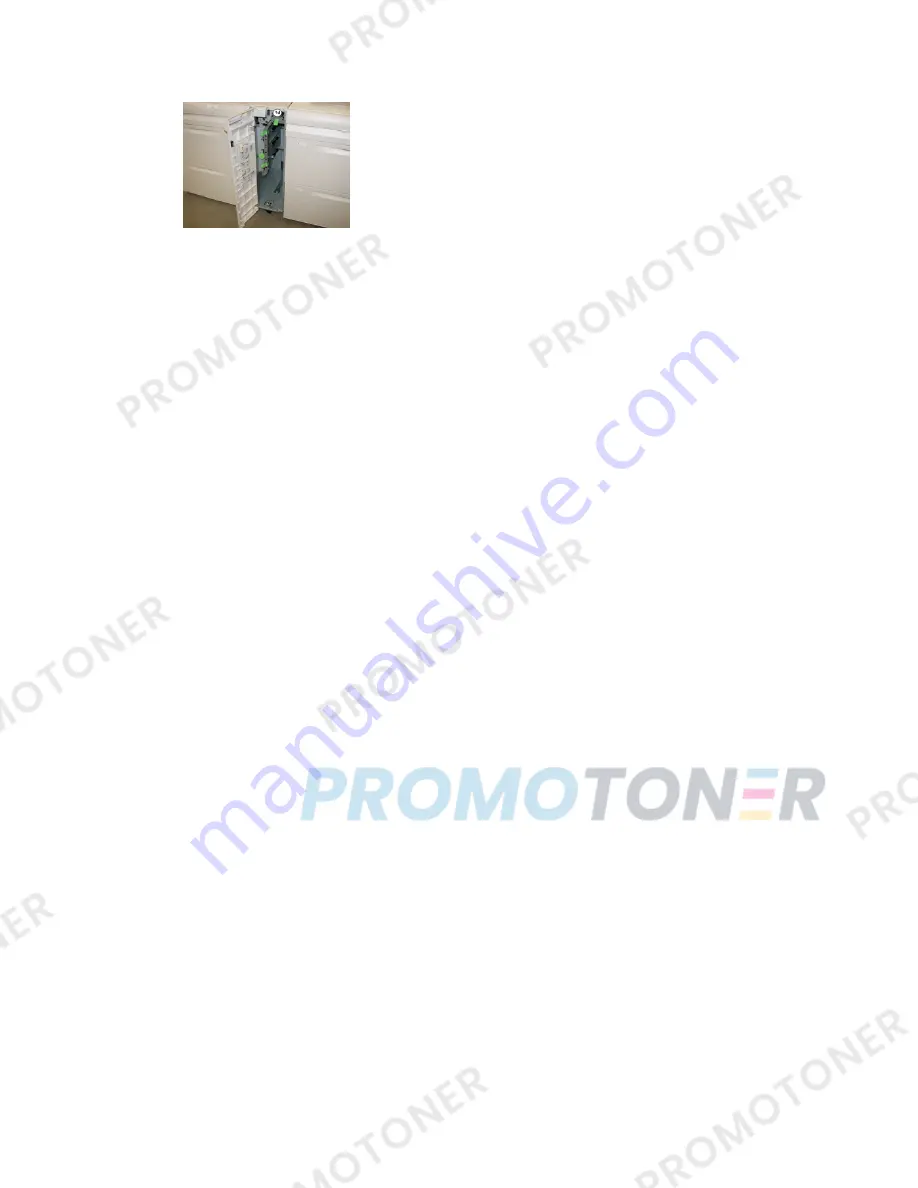
2. Move the lever 1d upward and remove the jammed paper.
Note
If paper is torn, check inside the machine and remove it.
3. If the paper cannot be removed, turn the knob 1c clockwise, and then remove the
jammed paper.
4. Return the lever 1d to the original position.
5. Close the front cover of the OHCF.
Note
If the front cover of the OHCF is not completely closed, a message will appear and
the machine will not operate.
11-15
Xerox
®
Versant
®
2100 Press
User Guide
Chained (Second) Oversized High Capacity Feeder (OHCF / Trays 8 and 9)
Содержание Versant 2100
Страница 36: ...Xerox Versant 2100 Press 3 8 User Guide Technical Specifications...
Страница 58: ...Xerox Versant 2100 Press 4 22 User Guide Paper and Other Media...
Страница 70: ...Xerox Versant 2100 Press 7 6 User Guide Machine Status...
Страница 160: ...Xerox Versant 2100 Press 11 16 User Guide Chained Second Oversized High Capacity Feeder OHCF Trays 8 and 9...
Страница 168: ...Xerox Versant 2100 Press 12 8 User Guide Interface Module...
Страница 212: ...Xerox Versant 2100 Press 15 10 User Guide High Capacity Stacker HCS...
Страница 246: ...Xerox Versant 2100 Press 16 34 User Guide Standard Finisher Booklet Maker Finisher...
Страница 295: ......
Страница 296: ......