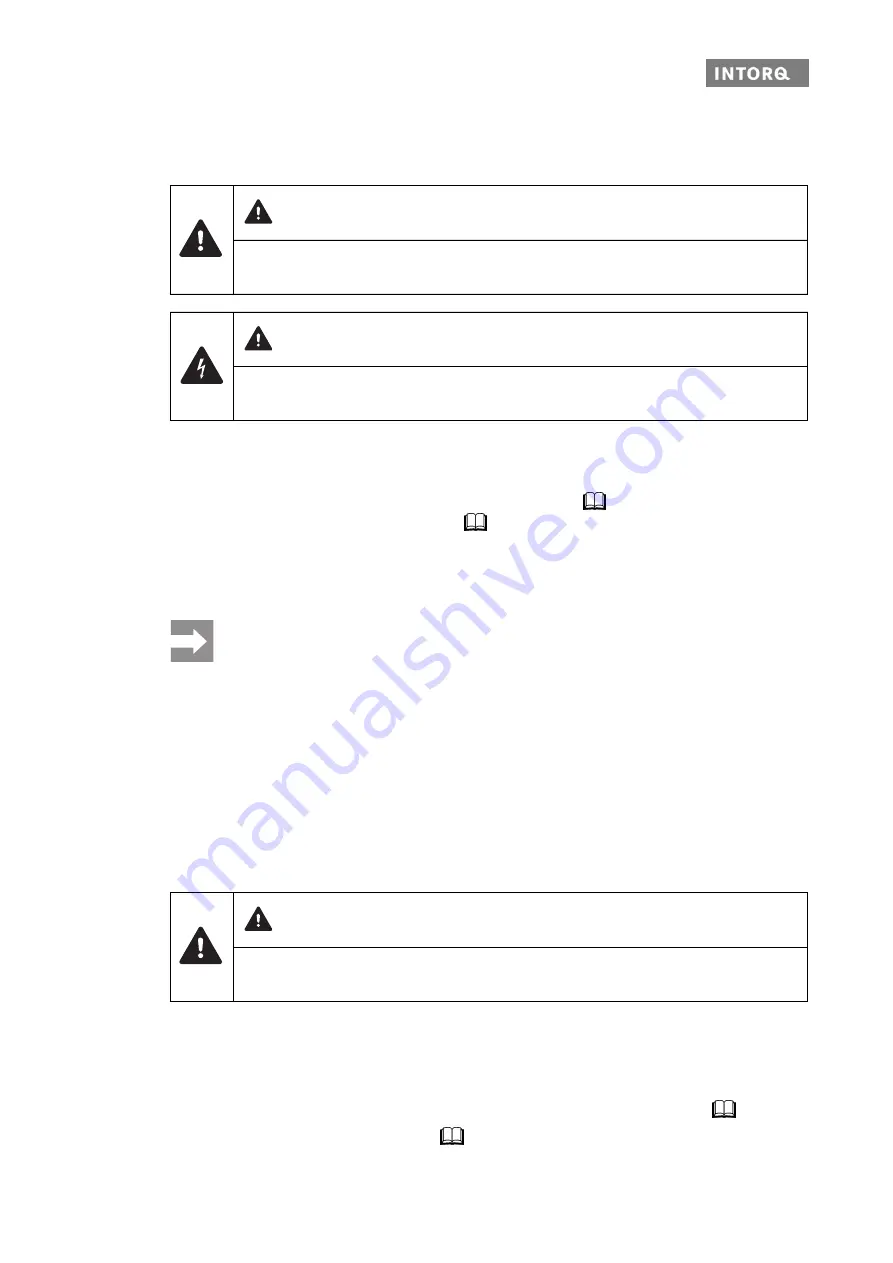
Maintenance and repair
INTORQ | BA 14.0196 | 04/2016
44
7.2.2
Release / voltage
1. Start motor and control system!
2. Observe the air gap “s
L
” when the drive is running. It should be zero.
3. Measure the DC voltage at the brake.
-
After the over-excitation time (see bridge/half-wave rectifier,
must correspond to the holding voltage (
37). A deviation of ±10 % is permissible.
7.3
Maintenance
7.3.1
Check the rotor thickness
1. Stop the motor and control system!
2. Remove the motor cover and remove the cover ring, if present.
3. Measure the rotor thickness using a caliper gauge.
4. Compare the measured rotor thickness with the minimally permissible rotor thickness,
5. If required, replace the rotor completely (
DANGER
Danger: rotating parts!
The running rotor must not be touched.
DANGER
There is a risk of injury by electrical shock!
Live connections must not be touched.
NOTICE
Brakes with defective armature plates, socket head cap screws, springs or counter friction
faces must always be replaced completely. Observe the following for inspections and mainte-
nance works:
❚
Contamination by oils and greases should be removed using brake cleaner, or the brake
should be replaced after determining the cause. Dirt and particles in the air gap between the
stator and the armature plate endanger the function and should be removed.
❚
After replacing the rotor, the original braking torque will not be reached until the run-in oper-
ation for the friction surfaces has been completed. After replacing the rotor, the run-in arma-
ture plates and counter friction faces have an increased initial rate of wear.
DANGER
Danger: rotating parts!
The motor must not run during the check.