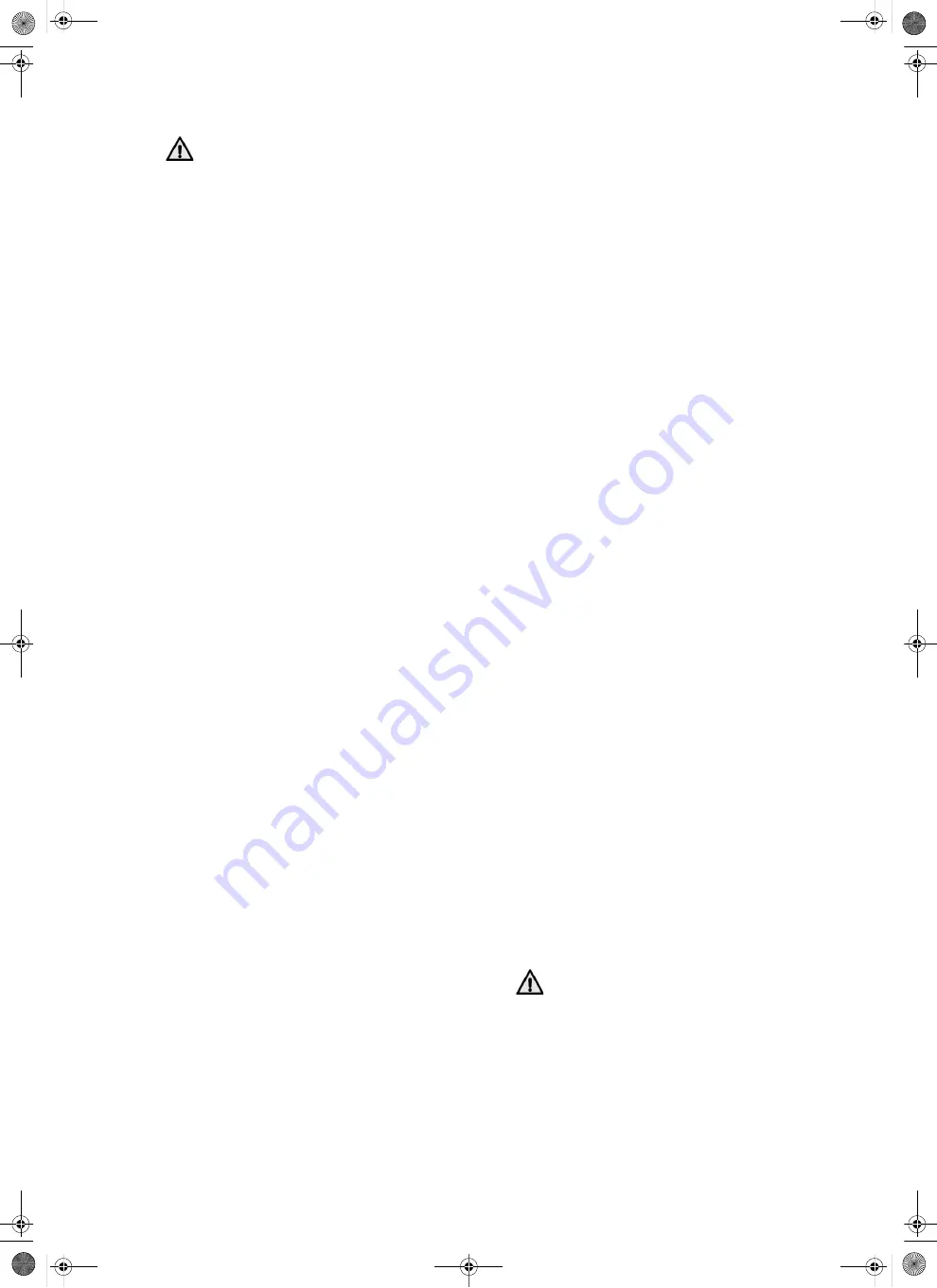
English
48
WILO SE 01/2018
CAUTION! Risk of malfunction of the pump!
Valves or gate valves must not be directly
installed on the pump suction.
• Provide an eccentric cone as indicated in the
EN 12845 standard;
7.4.4 Unit with positive suction head
[Fig. 6a - 6b] (As defined in EN 12845,
point 10.6.2.2)
• Check the minimum level defined for the storage
tanks or the minimum historical level for virtually
inexhaustible tanks in order to agree with the
conditions for the installation of the unit.
• Check if the diameter of the suction pipes is not
less than DN 65, and check if max suction speed
does not exceed 1.8 m/s.
• Check if the NPSH available on the suction side of
the pump is at least 1 meter higher than the NPSH
required for flow rate and at the maximum water
temperature.
• Fit a strainer outside the water tank on the suction
pipes, having a diameter of a size of at least 1.5 of
the nominal pipe diameter and that does not allow
the passage of parts with a diameter beyond 5 mm.
• Install a gate valve between the strainer and the
water tank.
7.4.5 Unit with suction lift
[Fig. 7] (As defined in EN 12845, point 10.6.2.3)
• Check the minimum level defined for storage
tanks, or the minimum historical level for virtually
inexhaustible tanks;
• Provide a diameter of the suction pipes equal or
larger than DN 80 and ensure that the maximum
suction speed does not exceed 1.5 m/s;
• Check if the NPSH available on the suction side of
the pump is at least 1 meter higher than the NPSH
required for flow rate and at the maximum water
temperature;
• Provide independent intake pipes for the pumps
equipped at the lowest point of the bottom valve;
• Fit a strainer on the suction pipes, before the bot-
tom valve. This strainer must be set up so that it
can be cleaned without having to empty the tank.
It must have a diameter of a size of at least 1.5 of
the nominal pipe diameter and does not allow the
passage of parts with a diameter beyond 5 mm.
• The distance between the rotation axis of the
pump and the minimum water level must not
exceed 3.2 m.
• Each pump must have automatic priming devices
in compliance with the requirements of EN 12845,
point 10.6.2.4.
7.4.6 Exhaust air for combustion and cooling diesel
engine
[Fig. 8] (Fig. 9a – 9b & variant)
If the system is assembled with a pump driven by
a diesel engine, the combustion gases of the
engine must be evacuated outside by a pipe sup-
plied with an adequate silencer.
Back pressure cannot exceed recommendations
for the type of diesel engine installed. The exhaust
pipe must have an adequate size respective to the
length of piping. It must be isolated and supplied
with sufficient protections against accidental
contacts with surfaces at high temperatures.
The exhaust tailpipe must not be close to windows
or doors. Besides, exhaust gas must not come
back into the pump room.
The exhaust tailpipe must be protected against
the weather and must not allow the introduction
of rainwater into the exhaust pipe or the return of
condensate to the engine.
Hoses have to be as short as possible (perfectly no
longer than 5.0 m), with as less curves as possibles
and a radius less than 2.5 times the pipe diameter.
Pipes must be supported and a condensate drain
system must be supplied with a material resistant
to the acidity of the condensate.
The ventilation system in the pump room with
diesel pumps with air cooling or air/water
exchanger is crucial. This determines the correct
functioning of the fire extinguishing system.
The ventilation system must allow dissipation of
heat generated during operation of the diesel
pump system and ensure a correct air flow to cool
the engine.
The room’s openings must consider the air flow
necessary for the engine, which may vary accord-
ing to altitude. (See manufacturers’ data of diesel
engine).
8 Commissioning
For the first commissioning, recommend to con-
tact the closest Wilo
after-sales service agent or
our after-sales call centre.
The commissioning of the pressure boosting sys-
tem must be performed by qualified staff.
8.1 General preparations and check
• Before switching on for the first time, check that
the wiring has been done correctly, particularly
the earth connection;
• To make sure that rigid connections are not
exposed to mechanical stress;
• Fill the installation and search for possible faults
during visual inspection;
• Open the gate valves on the pump sides and on
the discharge pipe;
CAUTION! Risk of product damage!
Never let the system run dry. Dry running
destroys the pump‘s mechanical seal tightness.
• The jockey pump tank is empty of water; inflate
it to a pressure 0.5 bar below the pressure which
activates the jockey pump.
• Do not exceed the maximum inflation value for
the vessel.
om_sifire_easy__4206362_ed02__1801_de_en_fr.book Seite 48 Freitag, 2. Februar 2018 10:23 10
Содержание SiFire Easy
Страница 2: ...Fig 1 Fig 2a om_sifire_easy__4206362_ed02__1801_de_en_fr book Seite 1 Freitag 2 Februar 2018 10 23 10...
Страница 3: ...Fig 2b Fig 3 om_sifire_easy__4206362_ed02__1801_de_en_fr book Seite 2 Freitag 2 Februar 2018 10 23 10...
Страница 4: ...Fig 4 Fig 5 om_sifire_easy__4206362_ed02__1801_de_en_fr book Seite 3 Freitag 2 Februar 2018 10 23 10...
Страница 5: ...Fig 6a Fig 6b om_sifire_easy__4206362_ed02__1801_de_en_fr book Seite 4 Freitag 2 Februar 2018 10 23 10...
Страница 10: ...om_sifire_easy__4206362_ed02__1801_de_en_fr book Seite 9 Freitag 2 Februar 2018 10 23 10...
Страница 112: ......