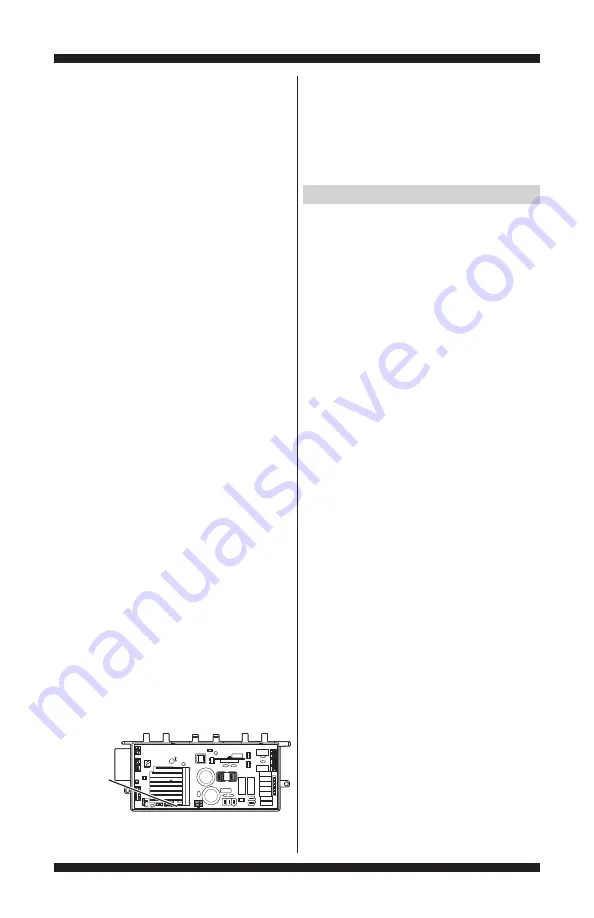
PAGE 2
FOR SERVICE TECHNICIAN’S USE ONLY
DO NOT REMOVE OR DESTROY
SERVICE DIAGNOSTIC MODE
These tests allow factory or service personnel
to test and verify all inputs to the main control
board. You may want to do a quick and overall
checkup of the washer with these tests before
going to specific troubleshooting tests.
ACTIVATING SERVICE DIAGNOSTIC MODE
1.
Be sure the washer is in standby mode
(plugged in with all indicators off).
2.
Select any three (3) buttons (except
POWER) and follow the steps below, using
the same buttons (remember the buttons and
the order that the buttons were pressed):
Within 8 seconds,
•
Press and Release the
1st
selected button,
•
Press and Release the
2nd
selected button,
•
Press and Release the
3rd
selected button;
•
Repeat this 3 button sequence 2 more times.
3.
If this test mode has been entered
successfully, all indicators on the console
will be illuminated for 5 seconds with “
888
”
showing in the three-digit display and a tone
will sound. If there are no saved fault codes,
all indicators on the console will momentarily
turn off, and then only the seven segment
display will come back on and display “
888
”.
Upon entry to Service Diagnostic mode, all
cycles and options reset to factory default.
NOTE:
The Service Diagnostic mode will time
out after 5–10 minutes of user inactivity, or
shut down if AC power is removed from the
washer.
Unsuccessful Activation
If entry into diagnostic mode is unsuccessful,
refer to the following indication and action:
Indication
: None of the indicators or display
turn on.
Action:
Select any cycle.
If indicators come on, try to change the
function for the three buttons used to activate
the diagnostic test mode. If any button is
unable to change the function, something
is faulty with the button, and it will not be
possible to enter the diagnostic mode using
that button. Replace the user interface.
If no indicators come on after selecting
the cycle, go to TEST #1: Main Control,
page 14.
DIAGNOSTIC GUIDE
Before servicing, check the following:
Make sure there is power at the wall outlet.
Has a household fuse blown or circuit breaker
tripped? Was a regular fuse used? Inform
customer that a time-delay fuse is required.
Are both hot and cold water faucets open
and water supply hoses unobstructed?
Make sure drain hose is not sealed into
drain pipe, and that there is an air gap for
ventilation. Ensure drain height is between
39" (991 mm) and 8' (2.4 m) above the floor.
All tests/checks should be made with a
VOM (volt-ohm-milliammeter) or DVM
(digital-voltmeter) having a sensitivity of
20,000
Ω
per volt DC or greater.
Resistance checks must be made with
washer unplugged or power disconnected.
IMPORTANT:
Avoid using large diameter
probes when checking harness connectors
as the probes may damage the connectors
upon insertion.
Check all harnesses and connections before
replacing components. Look for connectors
not fully seated, broken or loose wires and
terminals, or wires not pressed into connectors
far enough to engage metal barbs.
A potential cause of a control not
functioning is corrosion or contamination on
connections. Use an ohmmeter to check for
continuity across suspected connections.
DIAGNOSTIC LED – MAIN CONTROL
A troubleshooting tool has been implemented
onto the main control board—a diagnostic LED.
LED Flashing
– The Control is detecting correct
incoming line voltage and the processor is
functioning.
LED OFF or ON
– Control malfunction.
Perform TEST #1: Main Control, page 14, to
verify main control functionality.
Figure 1 - Diagnostic LED
LED
Location