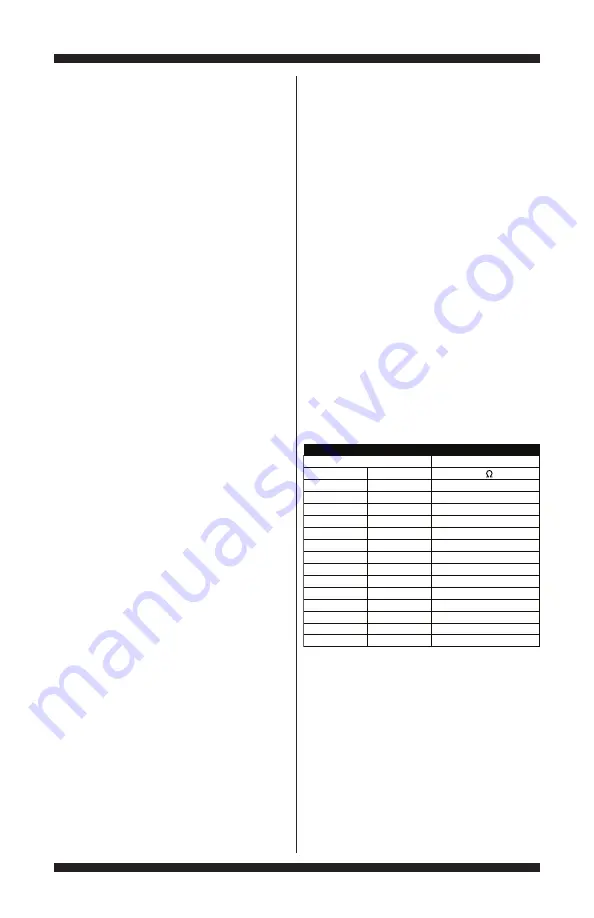
PAGE 18
FOR SERVICE TECHNICIAN’S USE ONLY
DO NOT REMOVE OR DESTROY
TEST #5: Temperature Thermistor
This test checks valves, main control,
temperature thermistor, and wiring.
1.
Check the cold valve by performing Cold
Valve test under Service Load Control Mode
in Service Diagnostic Mode on page 4.
If cold water is being dispensed, proceed
to step 2.
If hot water is being dispensed, verify
proper hose connection.
2.
Check the hot valve by performing Hot
Valve test under Service Load Control Mode
in Service Diagnostic Mode on page 4.
If hot water is being dispensed, proceed
to step 3.
If cold water is being dispensed, ensure
that household hot water is present.
3.
Unplug washer or disconnect power.
4.
Remove console to access main control.
5.
Remove connector
J2
from the main
control. With an ohmmeter, measure the
resistance of the temperature thermistor
between pins J2-1 and J2-2. Verify that the
approximate resistance, shown in the table
below, is within ambient temperature range.
If the resistance is within the range shown
in the table, go to step 6.
If the resistance is infinite or close to zero,
replace the valve assembly.
NOTE:
Most thermistor errors are a result
of the resistance being out of range. If the
temperature thermistor malfunctions, the
washer will default to pre-programmed
wash settings.
6.
If the thermistor is good, replace main
control and perform Service Diagnostics
(see page 5) to verify repair.
Approx. Resistance
F°
C°
(K )
32
0
163
41
5
127
50
10
100
59
15
79
68
20
62
77
25
50
86
30
40
95
35
33
104
40
27
113
45
22
122
50
18
131
55
15
140
60
12
149
65
10
Approx. Temperature
THERMISTOR RESISTANCE
If continuity fails, replace the UI harness
and go to step 5.
If continuity passes, replace the user
interface and go to step 5.
5.
Reassemble all parts and panels.
6.
Plug in washer or reconnect power.
7.
To verify repair, activate the Service
Diagnostic Mode, and then perform Key
Activation & Encoder Test on page 3.
Some buttons do not light indicators:
1.
Unplug washer or disconnect power.
2.
Replace the UI assembly.
3.
Reassemble all parts and panels.
4.
Plug in washer or reconnect power.
5.
To verify repair, activate the Service
Diagnostic Mode, and then perform Key
Activation & Encoder Test on page 3.
No audio feedback is heard:
1.
Enter the Service Diagnostic Mode, and then
perform Key Activation & Encoder Test on page 3.
If audio feedback is heard with each button
press while in Key Activation & Encoder
Test mode, continue to step 2.
If no audio feedback is heard with each
button press while in Key Activation &
Encoder Test mode, continue to step 4.
2.
Exit Key Activation & Encoder Test by
pressing POWER.
3.
Turn on the washer and enable audio
feedback in normal mode:
On Whirlpool models, press and hold “End
Beep” for 3 seconds to change the button
sounds level (Off, Low, Med, High). Each
press and hold increments the sound
one level.
On Maytag models, press “Audio Level”
to change the audio level (Off, Low, High).
On Kenmore models, press and hold
“Cycle Signal” for 3 seconds to change
the button sounds level (Off, Low, ...High).
Each press and hold increments the
sound one level.
4.
Unplug washer or disconnect power.
5.
Access the console electronics and, if
needed, remove the user interface from the
console shell and visually check that the
speaker connector on the UI is fully seated.
6.
If visual check passes, replace the user
interface assembly.
7.
Reassemble all parts and panels.
8.
Plug in washer or reconnect power. Perform
Service Diagnostics on page 5. To verify repair,
activate the Service Diagnostic Mode, and then
perform Key Activation & Encoder Test on page 3.