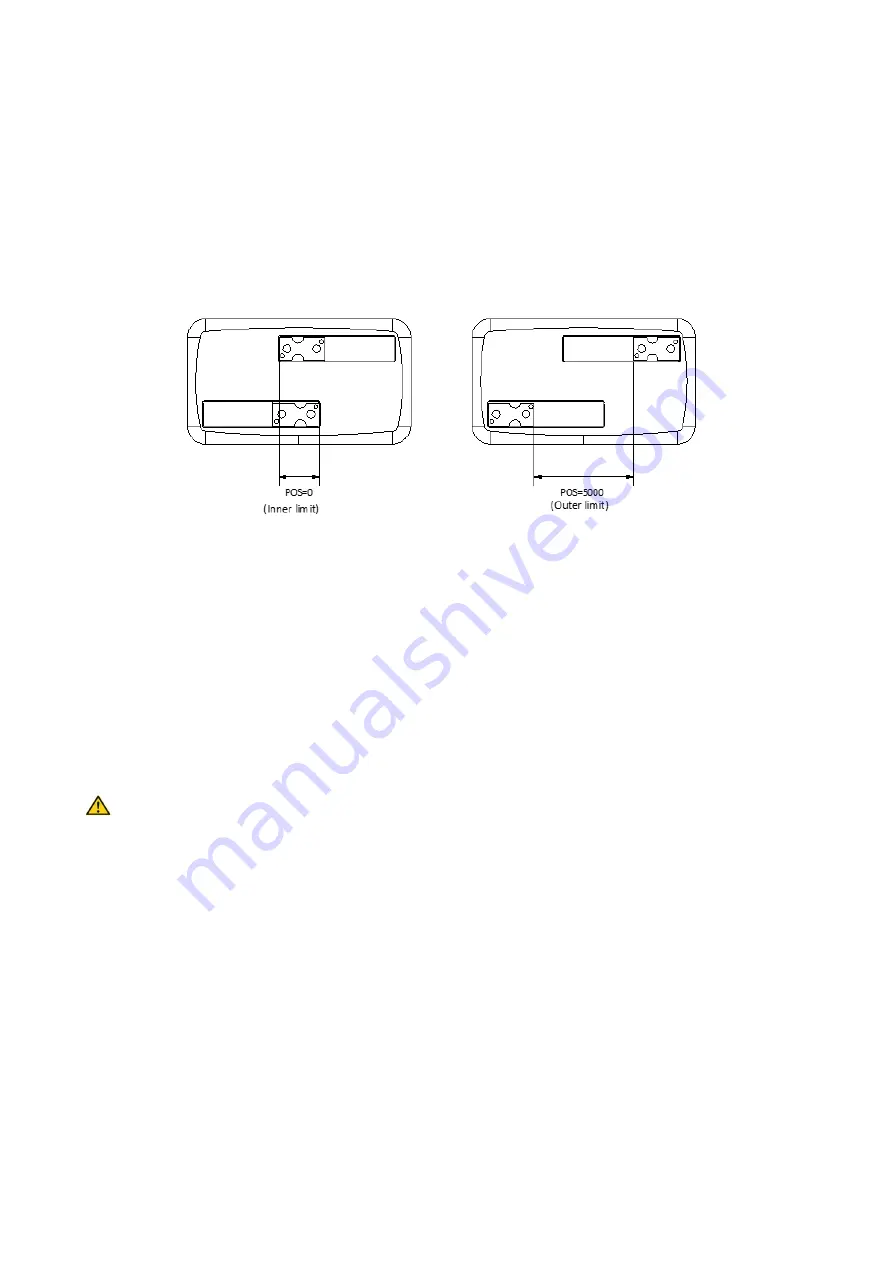
- 41 -
9.2
Position Sensors
The gripping module has an integrated position measurement system with which the position of the base
jaws is measured relatively. The position value corresponds to the spacing of the two base jaws. The inner
limit corresponds to the value 0 mm. Figure 12 shows the correlation between the position value and the
position of the base jaws using the example of the CRG 30-050. The current position value is transmitted in
the cyclic process data.
Figure 12: Example: position value CRG 30-050
9.3
Reference Run
In addition to the relative position measurement system, the gripping module CRG series has an absolute
measuring system which provide the position of the base jaws directly after activating. Therefor a reference
movement is not required. Nevertheless, the module can be referenced during operation. For this purpose,
the module moves the base jaws with defined force and speed to the outer limit and uses this position as a
reference value.
Keep the traversing range of the fingers free during the reference run to avoid collisions and faulty
referencing.
If an individual application makes an outwards reference run impossible, e.g. if it would lead to a collision
with a part or with the environment, the direction of the reference run can be reversed and the inner limit
can be used (see chapter 8.2.3.1).
9.4
Virtual Position Switches
To detect different end positions, up to four virtual position switches can be parameterized. These position
switches are realized in the control software of the gripping module (“virtually”). Their switching status is
transmitted via the cyclic process data of the gripping module.
Содержание 5120012
Страница 1: ...Mounting and Operating Manual CRG Series Electrical Gripping Modules with IO Link October 2020...
Страница 63: ...62 Figure 22 Configuration of the IO Link master Figure 23 Starting the S7 PCT port configurator device tool...
Страница 64: ...63 Figure 24 Configuration of the IO Link port...