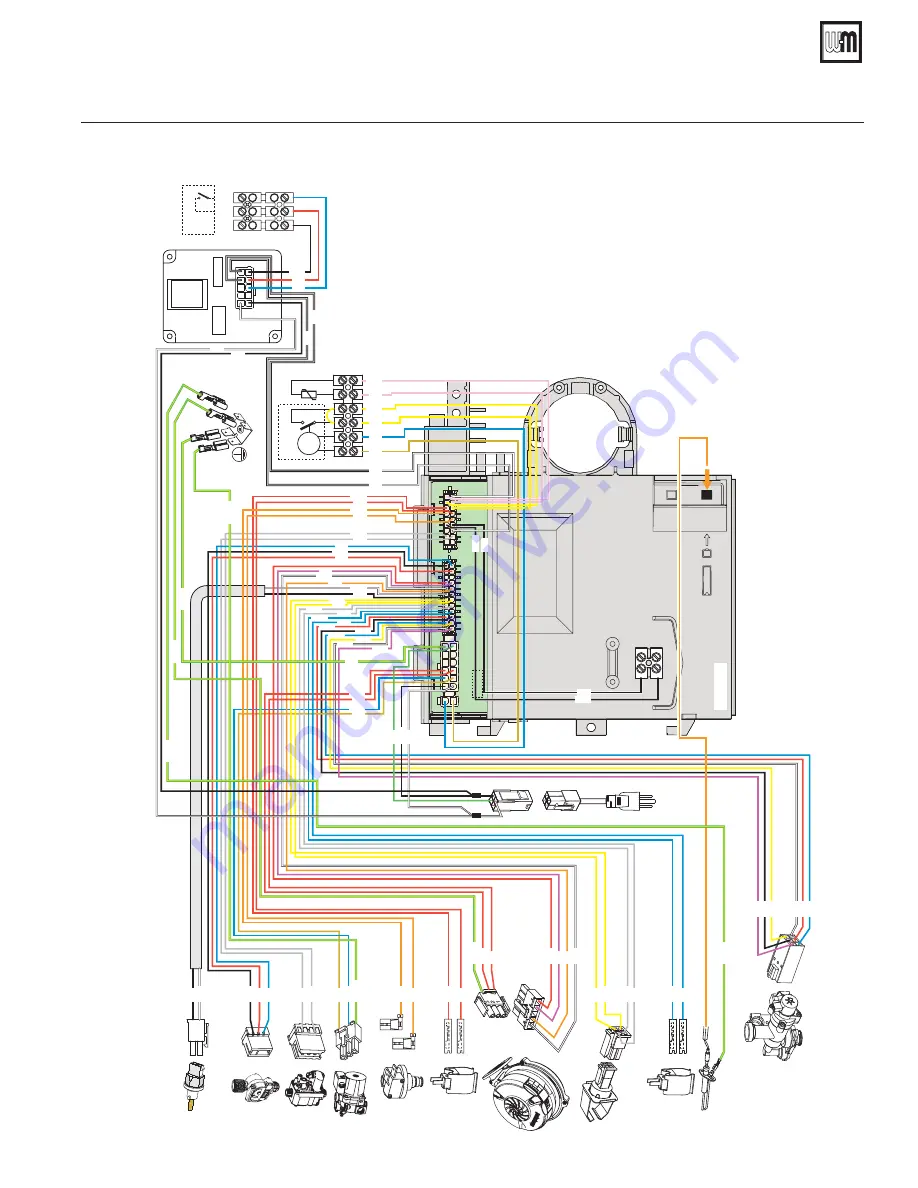
Part number 550-100-305/0118
53
AquaBalance
TM
W
ALL
M
OUNT
GAS
-
FIRED
WATER
BOILER
—
Boiler Manual
22
Wiring diagram — WMB-80/120C Combi Schematic
Figure 69
WMB-
80/120C –– Combi Schematic Wiring Diagram
ABM08
X3 - 12 X3 - 10 X3 - 1
1
X3 - 24 X3 - 22 X3 - 23
X3 - 6
X3 - 2
X3 - 13
X3 - 1
X2 - 5
X2 - 11
X4 - 8
X4 - 17
X4 - 5
X4 - 13
X4 - 12
X4 - 4
X2 - 7
X3 - 12
X3 - 24
X3 - 11
X3 - 23
X3 - 10
X3 - 6
X3 - 13
X3 - 2
X3 - 1
X4 - 8
X4 - 17
X2 - 1
1
X2 - 5
X4 - 13
X4 - 5
X4 - 4
X4 - 12
X2
1
12
13
24
X3
1
9
10
18
X4
61
12
7
191
136
44
32
11
4
X3 - 18
X3 - 18
95
X3 - 5
X3 - 17
X3 - 4
X3 - 16 X3 - 4
X3 - 17
X3 - 5
X3 - 22
X3 - 8
X3 - 20
X3 - 7
X3 - 19
X3 - 8
X3 - 20
X3 - 7
X3 - 19
X2 - 4
X2 - 10
X2 - 10
X2 - 4
GROUND
X3 - 9
X3 - 21
186
X3 - 9
X3 - 21
42
278
16
GROUND
X4 - 6
X4 - 15
X4 - 6
X4 - 15
GROUND
X2 - 12
X2 - 6
X1 - 1
X1 - 2
X4 - 3
X4 - 11
X4 - 2
X4 - 10
X1
81
373
1
2
GROUND
GROUND
GROUND
X2 - 1
GROUND
120Vac
60Hz
GROUND
370
138
(see note 3)
M
1
61
0
5
279
284
104 (2)
X4 - 7
X4 - 1
72
(see note 2)
X0
R
W
C
TT
X0 - 10
X0 - 9
X0 - 8
X0 - 1
X0 - 6
X0 - 5
X0 - 4
104 (1)
12
3
4
5
6
.(<
$
%##
&'*
#
%
+
;#<=
&
$>?@
$D>E@
*
#!
$!
H
+#
=J#
&O
Q
?Y[
+;\;Q
Y%[
]!*
%
^H\=_Q'=+`