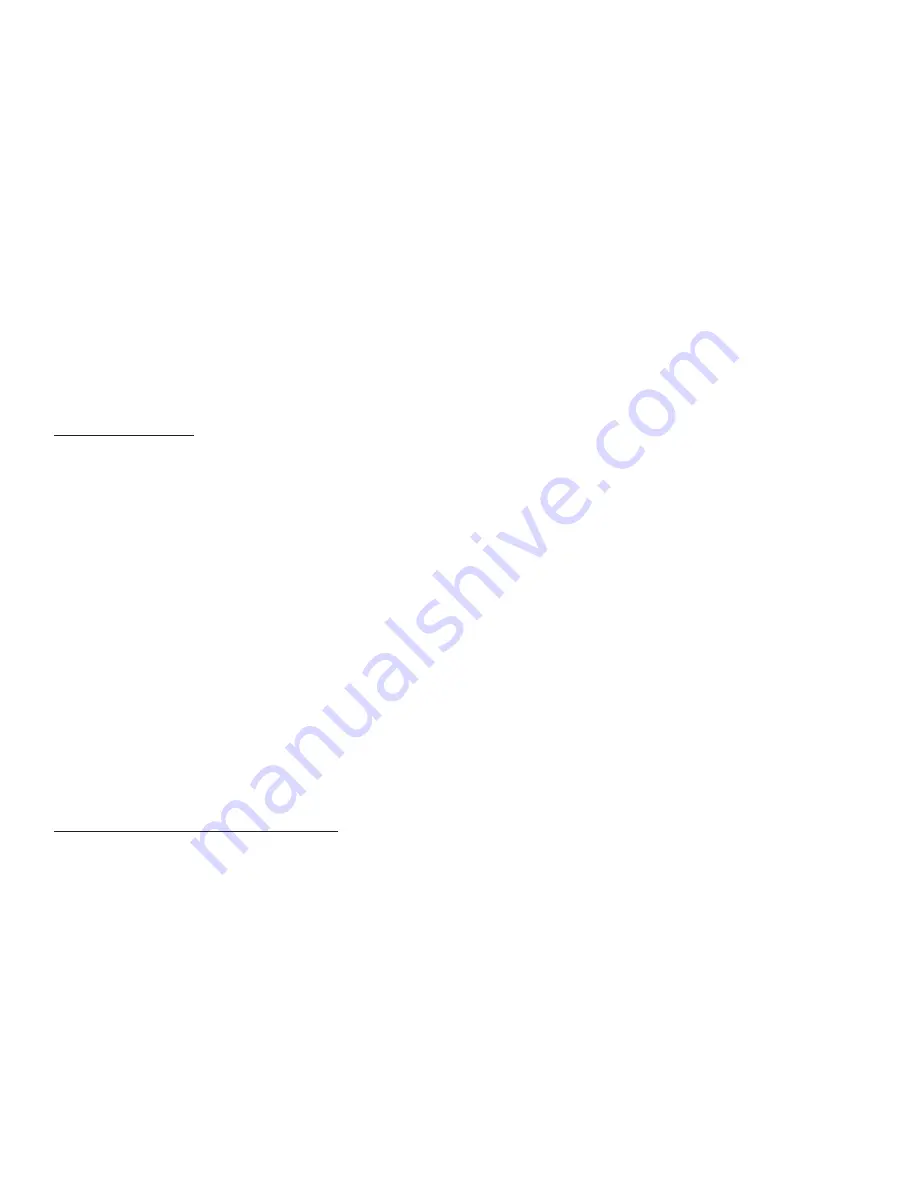
Page 48
WS1HR & WS1.25HR Manual
The regenerant piston (the small diameter one behind the main piston) is removed from the main piston by pressing sideways and
unsnapping it from its latch. Chemically clean in dilute sodium bisulfi te or vinegar, or replace the regenerant piston if needed. To
remove the main downfl ow or upfl ow piston fully extend the piston rod and then unsnap the main piston from its latch by pressing
on the side with the number. Chemically clean in dilute sodium bisulfi te or vinegar, or replace the main piston.
Reattach the main piston to the drive cap assembly. Reattach the regenerant piston (if needed) to the main piston. Do not lubricate
the piston rod, main piston or regenerant piston. Lubricant will adversely affect the clear lip seals. Reinsert the drive cap assembly
and piston into the spacer stack assembly and hand tighten the drive cap assembly. Continue to tighten the drive cap assembly using
a screwdriver as a ratchet until the black o-ring on the spacer stack assembly is no longer visible through the drain port. Excessive
force can break the notches molded into the drive back plate. Make certain that the main drive gear still turns freely. The exact
position of the piston is not important as long as the main drive gear turns freely.
Reattach the drive assembly to the control valve and connect all plugs. After completing any valve maintenance, press and hold
NEXT and REGEN buttons for 3 seconds or unplug power source jack (black wire) and plug back in. This resets the electronics and
establishes the service piston position. The display should fl ash all wording, then fl ash the software version and then reset the valve
to the service position.
Note: Refer to Figure 6 to identify main piston.
Spacer Stack Assembly
(Refer to Figure 6 for WS1HR & WS1.25HR spacer stack identifi cation.)
To access the spacer stack assembly remove the drive assembly, drive cap assembly and piston. The spacer stack assembly can
be removed easily without tools by using thumb and forefi nger. Inspect the black o-rings and clear lip seals for wear or damage.
Replace the entire stack if necessary. Do not disassemble the WS1HR or WS1.25HR stack.
The spacer stack assembly may be chemically cleaned (dilute sodium bisulfi te or vinegar) or wiped with a soft cloth.
The spacer stack assembly can be pushed in to the control valve body bore by hand. Since the spacer stack assembly can be
compressed it is easier to use a blunt object (5/8
”
to 1-1/8
”
in diameter) to push the center of the assembly into the control valve
body. The assembly is properly seated when at least four threads are exposed (approximately 5/8
”
). Do not force the spacer stack
assembly in. The control valve body bore interior can be lubricated with silicone to allow for easy insertion of the entire stack. Do
not use silicone or any other type of lubricant on the clear lip seals or the piston.
Reattach the drive cap assembly and piston(s) and the drive assembly.
After completing any valve maintenance, press and hold NEXT and REGEN buttons for 3 seconds or unplug power source jack
(black wire) and plug back in. This resets the electronics and establishes the service piston position. The display should fl ash all
wording, then fl ash the software version and then reset the valve to the service position.
Injector Cap, Screen, Injector Plug and Injector
Unscrew the injector cap and lift off. Loosen cap with special plastic wrench or pliers if necessary. Attached to the injector cap is a
screen. Remove the screen and clean if fouled.
The plug and/or injector can be pried out with a small screwdriver. The plug can be wiped clean. If the plug leaks replace the entire
plug. The injector consists of a throat and a nozzle. Chemically clean the injector with vinegar or sodium bisulfi te. The holes can be
blown out with air. Both pieces have small diameter holes that control the fl ow rates of water to insure that the proper concentration
of regenerant is used. Sharp objects, which can score the plastic, should not be used to clean the injector. Scoring the injector or
increasing the diameter of the hole could change the operating parameters of the injector.
Содержание WS1HR
Страница 2: ......
Страница 13: ...WS1HR WS1 25HR Manual Page 13 Figure 3 Figure 4 Figure 1 Figure 2...
Страница 30: ...Page 30 WS1HR WS1 25HR Manual Drawings and Part Numbers...
Страница 42: ...Page 42 WS1HR WS1 25HR Manual Flow Diagrams Service and Backwash...
Страница 43: ...WS1HR WS1 25HR Manual Page 43 Flow Diagrams Downflow and Upflow WS1HR Only...
Страница 44: ...Page 44 WS1HR WS1 25HR Manual Flow Diagrams Rinse and Fill...
Страница 54: ...Page 54 WS1HR WS1 25HR Manual...
Страница 55: ...WS1HR WS1 25HR Manual Page 55...
Страница 56: ...Page 56 WS1HR WS1 25HR Manual...
Страница 57: ...WS1HR WS1 25HR Manual Page 57...
Страница 58: ...Page 58 WS1HR WS1 25HR Manual...
Страница 59: ...WS1HR WS1 25HR Manual Page 59...