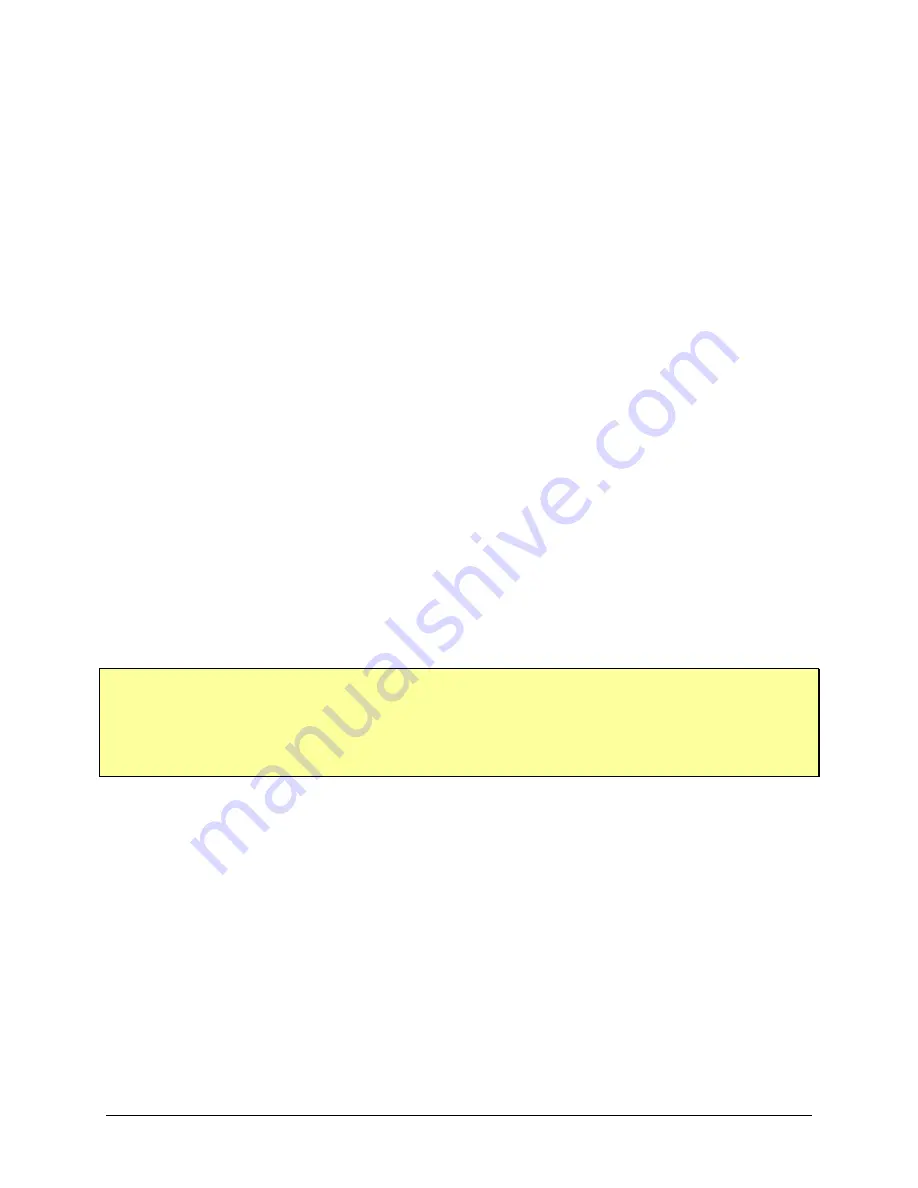
VTI Instruments Corp.
72
EX10xxA Triggering
The instrument’s internal system timer generates ticks at the specified timer interval, where each
tick represents a unique event. For example, a TRIG event source set to Timer at a timer interval of
0.005 s will generate internal triggers at a rate of 200 Hz.
The LXI alarm is specified by
IVI 3.15, IVILxiSync
specification. Similar to the timer, the LXI alarm
will cause an event, but these events are based on IEEE 1588 time and always occur at the pre-
programmed time. The alarm period can be set for this event as well, allowing the LXI alarm to fire
repeatedly at a defined interval.
As previously mentioned, an event condition can be designated to be any combination of Trigger
Bus channel transitions or levels, Digital I/O channel transitions or levels, and Timer ticks. If
multiple sources for an ARM event are specified, they are logically combined as follows:
ARM event = [(Timer tick event) AND (LXI alarm event) AND (LAN event) AND (Digital I/O event) AND (Trigger
Bus event)]
If multiple sources for a TRIG event are specified, they are logically combined as follows:
TRIG event = [(Timer tick event) AND (LXI alarm event) AND (LAN event) AND (Digital I/O event) AND (Trigger
Bus event)]
Within each digital hardware port (and LAN events), it is also possible to select multiple channels
and multiple conditions for a specific channel. In that case, they are logically combined as follows:
Digital I/O event = (Ch 7 events) AND (Ch 6 events) … AND (Ch 0 events)
Finally, within each channel, the four event conditions of Pos. Edge, Neg. Edge, Pos. Level, and
Neg. Level are OR’ed together.
As an example, if a Digital I/O event is specified to be a combination of a Pos. Level on channel 3,
a Pos. Edge on channel 6, and a Neg. Edge on channel 6, the event will be satisfied when a Pos.
Level on channel 3 occurs simultaneously with a Pos. Edge or a Neg. Edge transition on channel 6.
While the Digital I/O event structure was used as an example, the Trigger Bus event structure
operates in the same manner.
NOTE
The extensive flexibility of the trigger model system permits the creation of very specialized trigger
conditions, which is a powerful application tool. However, it also permits the creation of trigger
conditions that would be very difficult to satisfy in practice. For example, if edge conditions are
specified on multiple digital hardware channels, the edges must occur within 25 ns of each other to
be recognized as having occurred simultaneously. Similarly, the timer source should not be
combined with any digital hardware edge conditions.
M
AXIMIZING
M
EASUREMENT
P
ERFORMANCE
/ Noise Performance in Section 3, the EX10xxA takes advantage of
a sampling rate setting of less than 1 kSa/s to acquire and average multiple samples. This offers
improved noise performance, while maintaining the requested data output rate. However, the trigger
model must be configured in a specific manner to allow this to occur. Specifically, the TRIG event
source must be configured for Timer or LXI alarm must be enabled and configured. This is critical,
because only under this condition does the EX10xxA know exactly the rate and timing of the trigger
events. That is, it knows the available time in which to complete the acquisition and consequently
how many samples it can average and still complete the entire scan list. With any other trigger
source, the triggers can occur at any time. In that case, the EX10xxA completes the scan list in
minimum time and does not average.
Содержание EX1000A
Страница 25: ...www vtiinstruments com EX10xxA Introduction 25 FIGURE 1 2 RACKMOUNT HARDWARE INSTALLATION DIAGRAM ...
Страница 27: ...www vtiinstruments com EX10xxA Introduction 27 FIGURE 1 4 ISOMETRIC AND INTERNAL CJC PLATE DIAGRAM ...
Страница 28: ...VTI Instruments Corp 28 EX10xxA Introduction EX1044 DIAGRAM ...
Страница 29: ...www vtiinstruments com EX10xxA Introduction 29 FIGURE 1 5 EX1044 TABLE TOP USAGE ...
Страница 34: ......
Страница 56: ......
Страница 74: ......
Страница 130: ......
Страница 282: ......