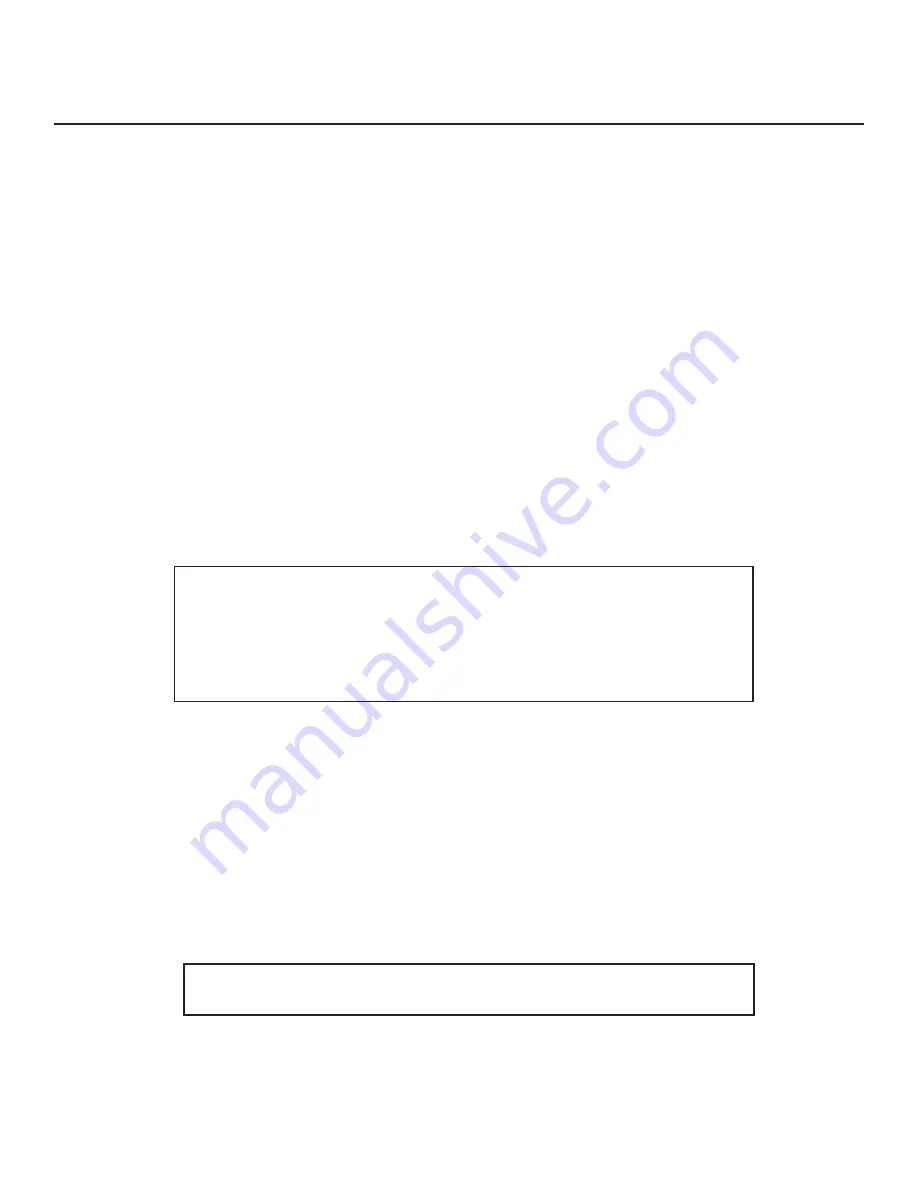
18
3.10 Refrigerant Recovery
Recovering the refrigerant is the removal of the charge from the system by use of a recovery pump and
storing in either a recovery bag or tank that is specifically designed for this purpose only.
Refrigerant recovery requires an EPA certification.
3.11 Flushing a System
Flushing a system is recommended when moisture, non-condensable, or other contaminants are
suspected in the system. It is also a must when a compressor burn out has occurred. A compressor burn
out will be evident by the smell when the system has been opened.
It is recommended that the system be flushed with dry nitrogen. Refrigerant can also be used for this
process as long as it is the same that is used when charging the system. Check the serial plate for the type
of refrigerant used in the system.
To flush the system, remove the compressor and filter / drier from the system. The condenser,
evaporator, and capillary tube should all be flushed independent from each other.
Before flushing, a process adaptor needs to be placed on one end of the component being flushed. Place
a rag over the opposite end to catch any oil or particles removed when flushed. Slowly open the valve
on the nitrogen tank to begin. Once started, the valve can be opened further.
CAUTION: Use extreme care when using dry nitrogen. A nitrogen tank
could be pressurized as high as 2000 PSI. The cylinder should be
equipped with a pressure regulator, relief valve, and pressure gauge. Also
ensure that hoses are adequate and not worn or damaged. Do not exceed
300 PSI when flushing a system.
CAUTION: IF REFRIGERANT IS USED AS A MEANS
OF FLUSHING - IT MUST BE RECOVERED
2010 - Viking Preferred Service
SMR-0005
Содержание DFUW244CL
Страница 6: ...Section 1 Introduction to Dual Zone 2010 Viking Preferred Service SMR 0005 ...
Страница 10: ...Section 2 Dual Zone Characteristics 2010 Viking Preferred Service SMR 0005 ...
Страница 16: ...Section 3 Refrigeration Systems 2010 Viking Preferred Service SMR 0005 ...
Страница 27: ...Section 4 TruProtect Control Diagnostics 2010 Viking Preferred Service SMR 0005 ...
Страница 30: ...Section 5 Mechanical System Components 2010 Viking Preferred Service SMR 0005 ...
Страница 38: ...Section 6 Structural Components 2010 Viking Preferred Service SMR 0005 ...
Страница 42: ...Section 7 Electrical Components 2010 Viking Preferred Service SMR 0005 ...
Страница 50: ...Section 8 Control Components 2010 Viking Preferred Service SMR 0005 ...
Страница 54: ...Section 9 Wiring 2010 Viking Preferred Service SMR 0005 ...
Страница 57: ...52 J110 J111 J112 J2 J1 J4 J7 J3 9 3 Main Power Board 2010 Viking Preferred Service SMR 0005 ...
Страница 58: ...9 4 User Interface 53 2010 Viking Preferred Service SMR 0005 ...
Страница 59: ...Section 10 Reference Charts 2010 Viking Preferred Service SMR 0005 ...
Страница 64: ...Section 11 Trouble Shooting Guide 2010 Viking Preferred Service SMR 0005 ...
Страница 68: ...Section 12 Reference Photos 2010 Viking Preferred Service SMR 0005 ...
Страница 71: ...2010 Viking Preferred Service SMR 0005 ...
Страница 72: ...2010 Viking Preferred Service SMR 0005 ...
Страница 74: ...2010 Viking Preferred Service SMR 0005 ...
Страница 75: ...2010 Viking Preferred Service SMR 0005 ...
Страница 76: ...2010 Viking Preferred Service SMR 0005 ...
Страница 77: ...2010 Viking Preferred Service SMR 0005 ...
Страница 78: ...2010 Viking Preferred Service SMR 0005 ...
Страница 79: ...2010 Viking Preferred Service SMR 0005 ...
Страница 80: ...2010 Viking Preferred Service SMR 0005 ...
Страница 81: ...2010 Viking Preferred Service SMR 0005 ...
Страница 84: ...2010 Viking Preferred Service SMR 0005 ...
Страница 86: ...2010 Viking Preferred Service SMR 0005 ...
Страница 87: ...2010 Viking Preferred Service SMR 0005 ...