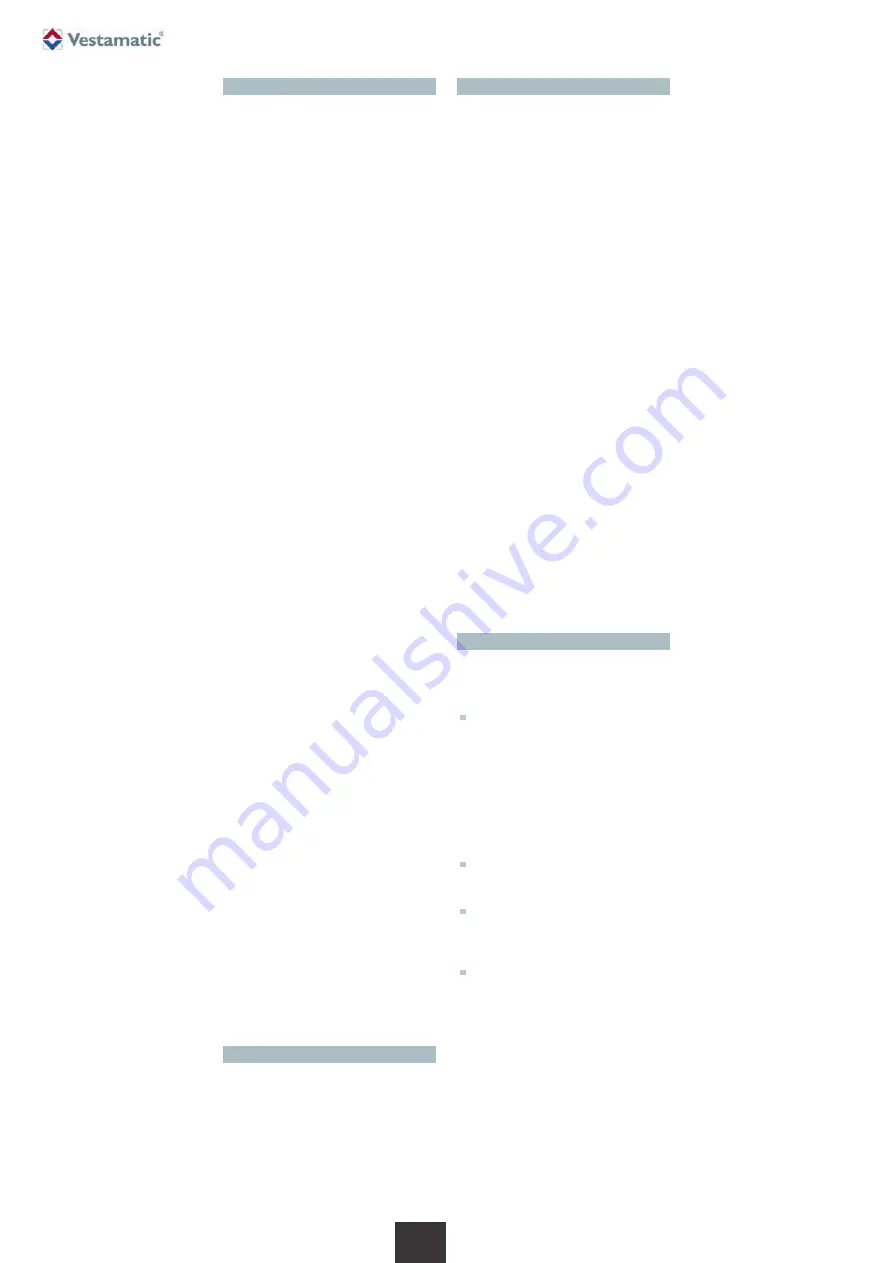
© Vestamatic GmbH
Ar
t.-Nr
.:
84501110 E1 •
V
estamatic GmbH • Dohrw
eg 27 • D-41066 Mönchengladbach • www
.v
estamatic.com
IF SMI KNX 24VDC
Subject to modifications.
Contents
General functional description
What is SMI?
17
General functional description
17
Software and functions
17
Operating states
18
State administration and state table
18
Travel command lock
18
Safety
18
Manual mode
18
Automatic mode
18
State table
19
ETS interface
20
ETS communication objects
21
“Safety” object
22
“Travel command lock” object
22
“Up/Down travel, channel x” object (manual mode)
22
“Stop/Step travel, channel x” object (manual mode)
22
“Sunshade, channel x” object (automatic mode)
22
“Automatic mode, channel x” object
22
“Position of sunshade (%), channel x” object
(automatic mode or, if automatic deactivated, manual mode)
22
“Position of slat angle (%), channel x” object
(automatic mode or, if automatic deactivated, manual mode –
only for blinds)
22
“Status position of sunshade (%), channel x” object
22
“Status position of slat angle (%), channel x” object
(only for blinds)
23
“Move to scene pos 1/pos 2, channel x” object
(manual mode)
22
“Save scene pos 1/pos 2, channel x” object (manual mode)
23
“Drive error status” object
23
ETS parameters
23–27
Planning and activation
27
Initialisation using drives with slave addresses already
programmed
27
Initialisation using drives with non-programmed slave
addresses or slave address 0
27
Errors and warnings during initialisation
28
Procedure for planning and activation
28
Options in the case of errors during planning and activation
28
User interface objects and properties (UIO interface)
28
Errors and warnings in properties 201 & 202
in the device object
28
User interface object 50001 and properties therein
29
Property 1, 51, 64 and 65 h
29
Property 80, 81 to 88
30
The SMI software
30
SMIdrive 8 is an EIB actuator for the control of up to 8 SMI drives. The
drives are independently addressed and controlled via the SMI. The drives
are controlled depending on the parametrisation of the actuator and com-
mands received via the EIB. Commands and data are transmitted via the
EIB using communication objects. Thus the drives connected to the actua-
tor can be moved independently via the EIB using standard functions such
as up/down, step/stop and others. Also, status information such as current
shade or slat position (%) and motor errors can be interrogated via the
EIB. A determination of prioritised operating states integrates manual and
automatic operations as well as those controlled by safety monitors or travel
locks.
The parametrisation and activation of the device is carried out via the ETS.
The ETS interface presents the project manager with parameters ar-
ranged in tabs. The communication objects are tabulated. The addressing
of the SMI drives connected to the device is carried out via the ETS acti-
vation. The addressing of the drives on the SMI side is either carried out
automatically using the slave addresses assigned in the ETS parametri-
sation or alternatively using SMI key IDs given in the ETS.
On the SMI side, the actuator only uses commands from the SMI standard
and is thereby compatible with SMI drives from all manufacturers. The
actuator does not functionally support use of manufacturer-specific fea-
tures. Nevertheless, manufacturer-specific parametrisation of SMI drives
can also be carried out via the EIB (see following section).
In addition to ETS parametrisation, a UIO (user interface object) interface
can be used in order to obtain access to the internal actuator SMI con-
figuration or directly to the SMI communication via the EIB. Software is
available for the practical use of this interface. It is, however, in principle
also possible to use this interface with, for instance, the device editor from
the ETS3 packet. The UIO interface permits further diagnostics within the
context of activation and also subsequent interventions in the parametri-
sation of SMI drives themselves.
Software and functions
The software of the SMI actuator consists of different units, which divide
into the resources available in the actuator hardware (a processor with
integrated Flash ROM, RAM and additional EEPROM).
The EIB operating system of the actuator “System 2” is compatible with
the BCU2 standard. It provides the entire interface for hardware resources
and applications software (firmware) on the one hand and for EIB on
the other. A bootloader in the Flash-ROM of the processor is an integral
component of System 2 and permits an exchange of software parts,
especially firmware (this is the applications software including SMI
communications library) through access via the EIB. The firmware is
mirrored in a copy in the EEPROM. Only firmware recognised as valid
is copied by the bootloader from the EEPROM into the processor Flash
ROM and, if appropriate, implemented.
An SMI communications library is an integral component of the firm-
ware. It is certified on the part of SMI and constitutes the interface to
the SMI and the slaves connected to it.
The actual applications software uses the remaining actuator memory
for the actuator software functionality depending on ETS parametrisa-
tion. It also includes the operation of the UIO interface via standardised
system functions.
The ETS interface includes information on EIB communication objects
and parameters, which specify the interface with the EIB and the
functionality of the actuator. These elements can be configured and
loaded into the actuator using the ETS. This information thereby reaches
the EEPROM of the actuator and can be read there by the operating
system and by the firmware and be evaluated in detail to determine the
performance.
Different software tools permit access to specific memories of the actuator
via the EIB. In addition to standard development tools, these tools are
namely a firmware update tool, which under certain conditions permits an
update of the firmware via the EIB, as well as an SMI tool, which using the
UIO interface supports diagnoses and direct access to the SMI via a gate-
way.
The functionality of the firmware and the elements of the ETS surface are
firstly described below. Other sections will explain specifics on the activa-
tion and the UIO interface.
2/ 15
G
SMI is the abbreviation for
S
tandard
M
otor
I
nterface. SMI has been de-
veloped for the connection of intelligent drives for roller shutters and sun
protection systems. SMI enables to transmit telegrams from control
system to the drive and vice versa. With SMI it is possible to combine
products from different sources together. The SMI Interface should spread
high value solutions and promote drives and controls on the market. The
applications in roller shutters and sun protection systems require extreme
robustness and economic efficiency. SMI has been developed to meet
these requirements.
What is SMI?