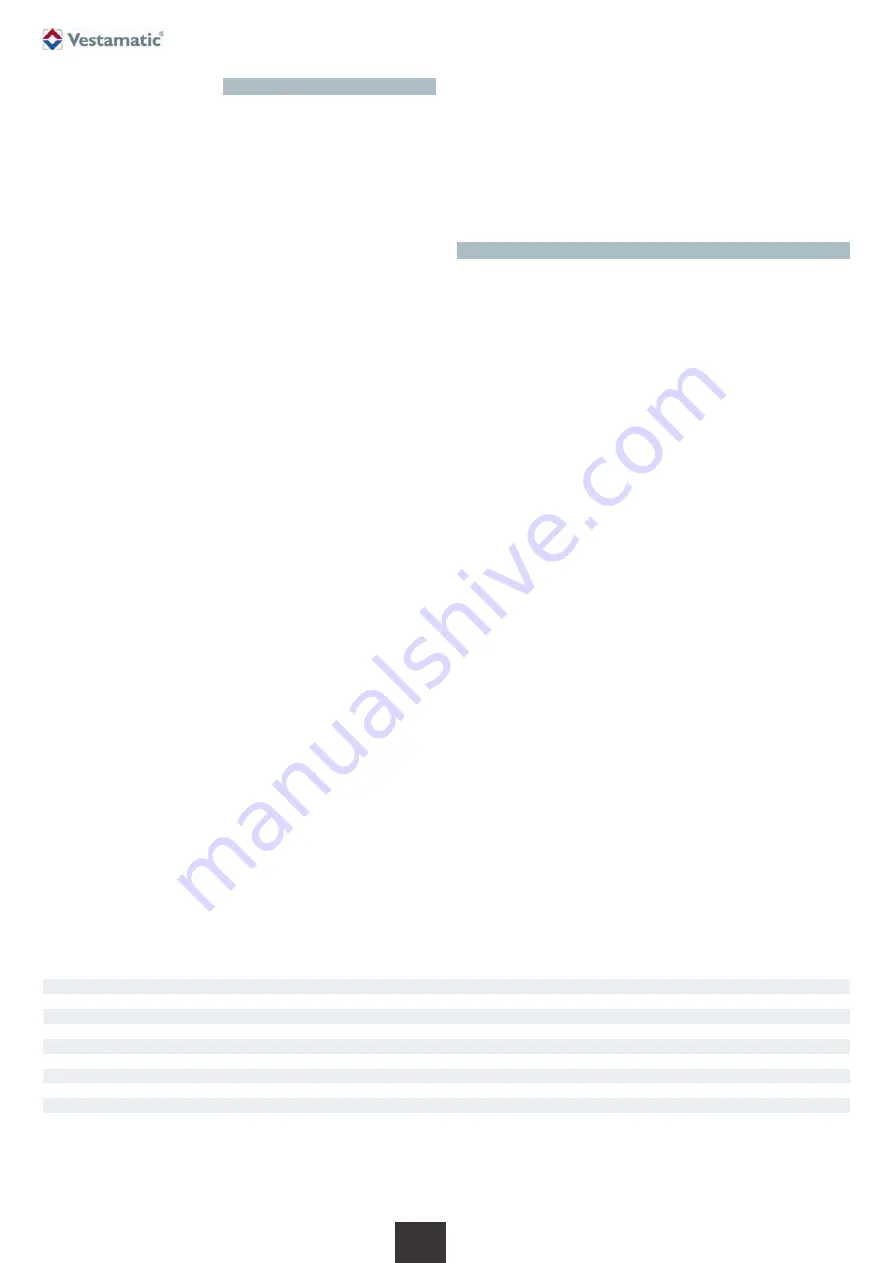
© Vestamatic GmbH
Ar
t.-Nr
.:
84501110 E1 •
V
estamatic GmbH • Dohrw
eg 27 • D-41066 Mönchengladbach • www
.v
estamatic.com
IF SMI KNX 24VDC
Subject to modifications.
Planning and activation
In the same way, the properties in the user interface object 50001 can be
checked and interpreted using the description outlined further below.
Please refer to “User interface object 50001 and properties therein”. The
SMI Tool is a diagnostic aid with very wide-ranging possibilities. It will
make access to individual actuators and the corresponding properties of
the user interface object 50001 much easier (see the following).
The user interface objects and properties have an interface which enables
(via the EIB through use of appropriate tools) further diagnoses, settings
and interventions, particularly on the SMI side at the particular actuator.
The use of the UIO interface is possible either via a standard tool such as
the Device Editor from the ETS3 accessories, or via a special tool that can
be used independently of the ETS but is used for the communication with
the particular actuator from the Falcon library and the EIB. The free soft-
ware assumes that the Falcon library (an integral component of, for exam-
ple, ETS3) is available.
However, the use of the UIO interface with, for instance, the Device Editor
requires the user to have special knowledge and a certain degree of ex-
perience. This chapter should therefore be read thoroughly and under-
stood. It is recommended that use with the Device Editor is reserved only
for emergencies, for instance for the diagnosis of otherwise inexplicable
faults. It is much simpler to use the UIO interface with the SMI tool (see
“The SMI software”).
The actuator software supports, in addition to the interface objects set out
in the EIB standard, another object with the ID “50001”, which supports
diagnosis and provides certain setter functionality for the actuator-con-
nected SMI bus and its devices. The above-mentioned software visualises
the properties provided via the user interface object 50001, thus enabling
a clear diagnosis. The software provides a practical way of intervening in
the SMI addressing of slave drives and in their parametrisation.
Essentially it is also possible to access the SMI drives directly and to
transmit any conceivable SMI command to the individual connected slaves
through the particular actuator acting as an SMI gateway. This is where
property 64 is used. As access is provided via the EIB, no hardware con-
nection to the particular SMI bus is required. Communication is conveyed,
via the physical address of the actuator concerned in the EIB, to the
appropriate SMI bus. Of course, drives may also be parametrised physi-
cally.
Errors and warnings in properties 201 & 202 in the device object
The actuator’s EIB operating system “System 2” provides further proper-
ties (in addition to those specified in the KNX standard) in the device
object that are partially co-used by the actuator’s application firmware.
In particular, the properties 201 and 202 in the device object allow
access to errors and warnings, thus supporting a diagnosis in the event of
faults.
Also written in these properties by the operating system are, if appropriate,
warnings or errors. The latter have codes
k
hex 6F and are described in
the documentation on System 2; those of the application of the actuators
have codes
g
hex 70 and are summarised in the following table.
Errors and warnings during initialisation
Irrespective of the mode of addressing, the actuator will generate corre-
sponding error codes if an assignment attempt is unsuccessful. Warning
codes are generated if, for instance, slaves are reprogrammed or it is iden-
tified that slaves have been exchanged. The 6 last different errors and
warnings are stored each in a property in the device object of the actuator.
Property 201 (hex C9) contains the warnings; Property 202 (hex CA) con-
tains the errors. The corresponding table of errors and warnings in proper-
ties 201 & 202 in the device object displays the possible error and warning
codes and their causes.
Procedure for planning and activation
The basic addressing modes of “automatic” and “per manufacturer and
SMI key ID” should be selected according to whether the drive data
(manufacturer and key ID) of the drives can be or has been recorded by
the installer during installation.
Many manufacturers help here by supplying the drives, the shades or the
cable with peelable stickers detailing the drive’s key ID. If the drive data is
clearly assigned to the drives’ installation locations, the setter can usually
carry out the activation through “per manufacturer and SMI key ID” addres-
sing with a single ETS download per actuator. This process also has the
advantage that all drive data is then documented in the ETS project.
In all other circumstances, “automatic” addressing should be used, which
may require appraisal of the initial random assignment after the first down-
load. After the slave addresses have been re-sorted in the ETS and follow-
ing a new download, the assignment is complete.
Even if the drives have been programmed with known slave addresses,
these can be entered straight into the ETS. If the spatial distribution of the
drives with these addresses is known from the outset, the assignment via
the channels can be set with similar precision. If the position of the drives
is not known, this can be determined after the initial ETS download
through operation via the EIB and then re-sorted.
If preprogrammed drives or partly pre-programmed, partly non-prepro-
grammed drives are used with unknown slave addresses, the actuator can
be initiated with the re-addressing = “enforce” parameter in order to pre-
program all slaves with the slave address 0. Thereupon the actuator will
program all connected slaves, according to the selected mode of addres-
sing, with the slave addresses given in the ETS. Whether the channel
assignment is then complete depends on the addressing procedure (see
above).
Options in the case of errors during planning and activation
If, during a full re-addressing process, more key IDs (i.e. slaves) have been
found than there are slave addresses available according to the ETS para-
metrisation, the remaining drives (key IDs) keep the slave address 0.
Alternatively, if fewer key IDs are found than there are slave addresses
available according to the ETS parametrisation, no drives will be assigned
to the remaining slave addresses or channels – the channels remain
without function.
Other possible errors during activation may be identified, whereby the pro-
perties 201 and 202 are read out from the device object (if appropriate
with the Device Editor from the ETS 3 accessories).
13/15
G
Code
Type
Description
Cause
0x73
Error
SMI transmission time-out
Error in SMI communication during transmission, possibly no SMI power.
0x74
Error
EEPROM error
Data error in EEPROM (checksum faulty), ETS download may be faulty.
0x76
Error
Slave programming error
An attempt to program a slave has failed.
0x77
Error
Slave address duplicated
A slave address has been assigned twice (same for two channels) in the ETS.
0x78
Warning
Unknown slave
A slave has been found that is not present in the ETS parametrisation.
0x7a
Warning
EEPROM updated
One or more new or exchanged slaves have been identified.
0x7b
Warning
Enforced new programming
All slaves are re-programmed according to ETS parameters.
0x7c
Warning
Missing slaves
It has not been possible to assign all the slaves that, according to the ETS, should be available.
0x7d
Warning
Incorrect key ID ignored
A slave is ignored because it has a different key ID to the one expected according to the ETS.
User interface objects and properties (UIO interface)