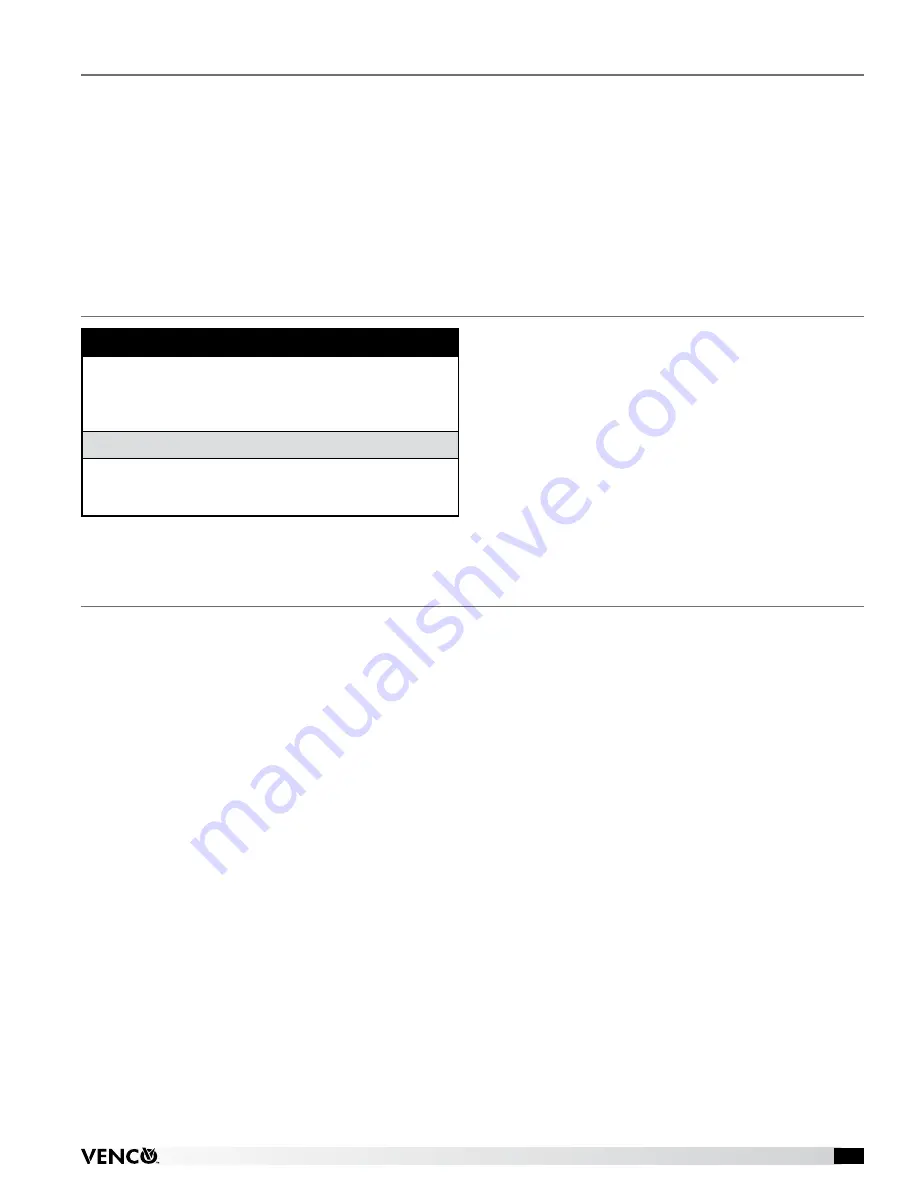
DANGER
Disconnect and secure to the ‘OFF’ position all
electrical power to the fan prior to inspection or
servicing. Failure to comply with this safety precaution
could result in serious injury or death.
DANGER
Pour écarter les risques de blessure grave ou de mort,
débrancher et verrouiller l’alimentation électrique en
position « Arrêt » avant tout contrôle ou entretien.
Inspection of the fan should be conducted at the first
30 minute and 24 hour intervals of satisfactory
operation.
• 30 Minute Interval - Check all fasteners for
tightness. Adjust and tighten as necessary.
• 24 Hour Interval - Inspect all fan components.
Check all fasteners, airfoil retaining ring, the safety
cable, and guy wires (if applicable). Adjust and
tighten as necessary.
Inspection
IMPORTANT:
If unusual vibration or oscillating
movement is observed during fan operation,
immediately discontinue use of the fan and contact the
manufacturer or a suitably qualified maintenance/repair
technician.
1. When the fan is started, observe the operation
and check for any unusual noise, vibration or
overheating. Refer to the Troubleshooting section
of this manual if a problem develops.
2. With the system in full operation, measure current
input to the VFD and compare with the FLA ratings
in the table above to determine if the motor/VFD
system is operating under safe load conditions.
3. Keep approaches to fan clean and free from
obstruction.
Operation
NOTE:
Installation and maintenance are to be
performed only by qualified personnel who are familiar
with local codes and regulations and have experience
with this type of equipment.
Once the fan has been put into operation, a periodic
maintenance program should be set up to ensure
reliable fan performance. A proper maintenance
program will help deliver years of dependable service.
Items to be included in this program are as follows:
1. Verify that all fasteners are tight and properly
torqued.
2. Verify that all of the fan’s safety systems – safety
cable, airfoil retaining ring, and guy wires (if
applicable) are properly installed. Inspect for signs
of damage or failure. Safety cable and guy wire
tension should also be checked. Safety cable
should be wrapped around the building structure
leaving as little slack as possible. Guy wires
should be under enough tension to prevent any
lateral movement of the motor and downtube (if
applicable).
3. Inspect the fan for signs of fatigue, corrosion, or
wear.
4. Impellers require little attention when moving clean
air. Occasionally, oil and dust may accumulate
causing imbalance. When this occurs, clean
the impeller and other fan components to
ensure smooth and safe operation. Remove any
accumulated dust and dirt using hot water or mild
cleaning solutions. Harsh chemicals should not
be used to clean the fan as they may damage the
fan’s finish or motor.
IMPORTANT:
Do not allow water or solvents to enter
the motor. Under no circumstances should motors be
sprayed with steam, water or solvents.
5. Motor maintenance is generally limited to cleaning.
Limit cleaning to exterior surfaces only. Removing
dust buildup on motor housing ensures proper
motor cooling.
6. Prior to restarting unit, check all fasteners for
tightness each time maintenance checks are
performed.
Maintenance
High Volume, Low Speed Ceiling Fans
21