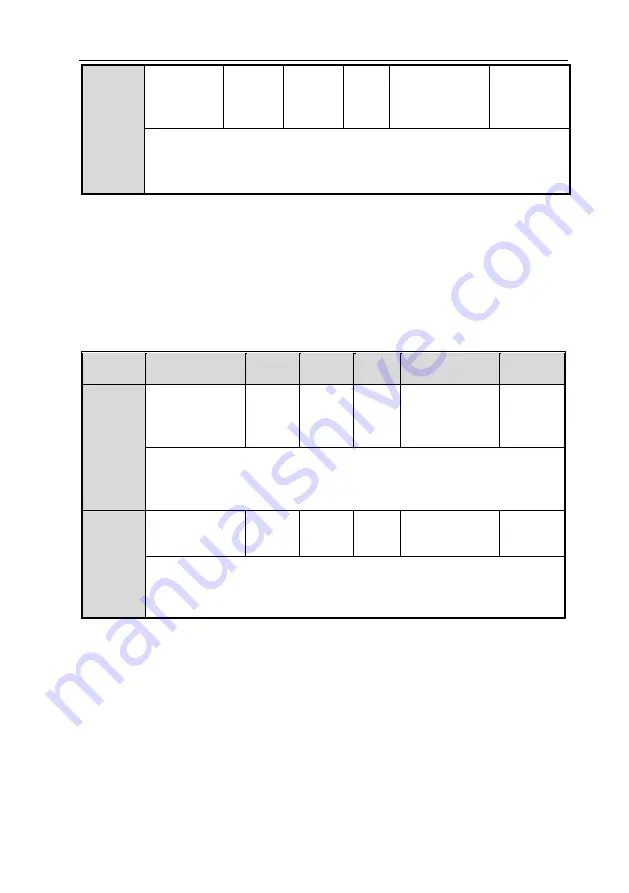
6 Adjustment
122 SD780 Series Servo Technical Manual
Pn300
Analog
speed
command
gain
150
~
3000
600
0.01V/
rated
speed
0x0300
Immediately
Use this parameter to set the analog voltage value of (V-REF) required by speed
command that makes the servo motor speed as rated value.
Note: Do not apply a voltage over-10V
~
10V. Exceeding this range may damage
the servo drive.
6.6.4 Torque Feedforward
Torque feedforward is a function to shorten the positioning time. The command is generated by
deviating the position command on the host device side. This command is sent to the servo
together with the speed command.
The speed command from the host device is connected to V-REF (CN1-5, 6), and the torque
feedforward command is connected to T-REF (CN1-9, 10).
Related parameters
Function
code
Parameter
Range
Default
Unit
Communication
address
When
enabled
Pn124
Speed/position
control selection
(T-REF
assignment)
0
~
1
0
-
0x0124
After
restart
Torque feedforward is a function to shorten the positioning time. Torque
feedforward can be selected to given by external analog T-REF.
0-None.
1-T-REF as a torque feedforward input.
Pn405
Analog torque
command gain
10
~
100
30
0.1V/
Rated
torque
0x0405
Immediat
ely
Use this parameter to set the analog voltage value of (T-REF) required by servo
motor rated torque.
Note: Do not apply a voltage over -10V
~
10V. Exceeding this range may damage
the servo drive.
6.6.5 PI-P Switching
When the control mode is speed control or position control, it could switch to PI-P control. When
the control mode is mixed, it is valid only when it is switched to internal speed, analog speed and
position mode. The PI-P switching can be switched by the digital signal “manual PI-P control signal
(/P-CON)”. When the /P-CON signal is ON, P control is performed. The conditions for selecting
automatic switching can also be selected by the parameter speed loop PI-P switching condition
selection switch Pn131.
(1)
Manual PI-P Control
a)
Configuration of manual PI-P Control