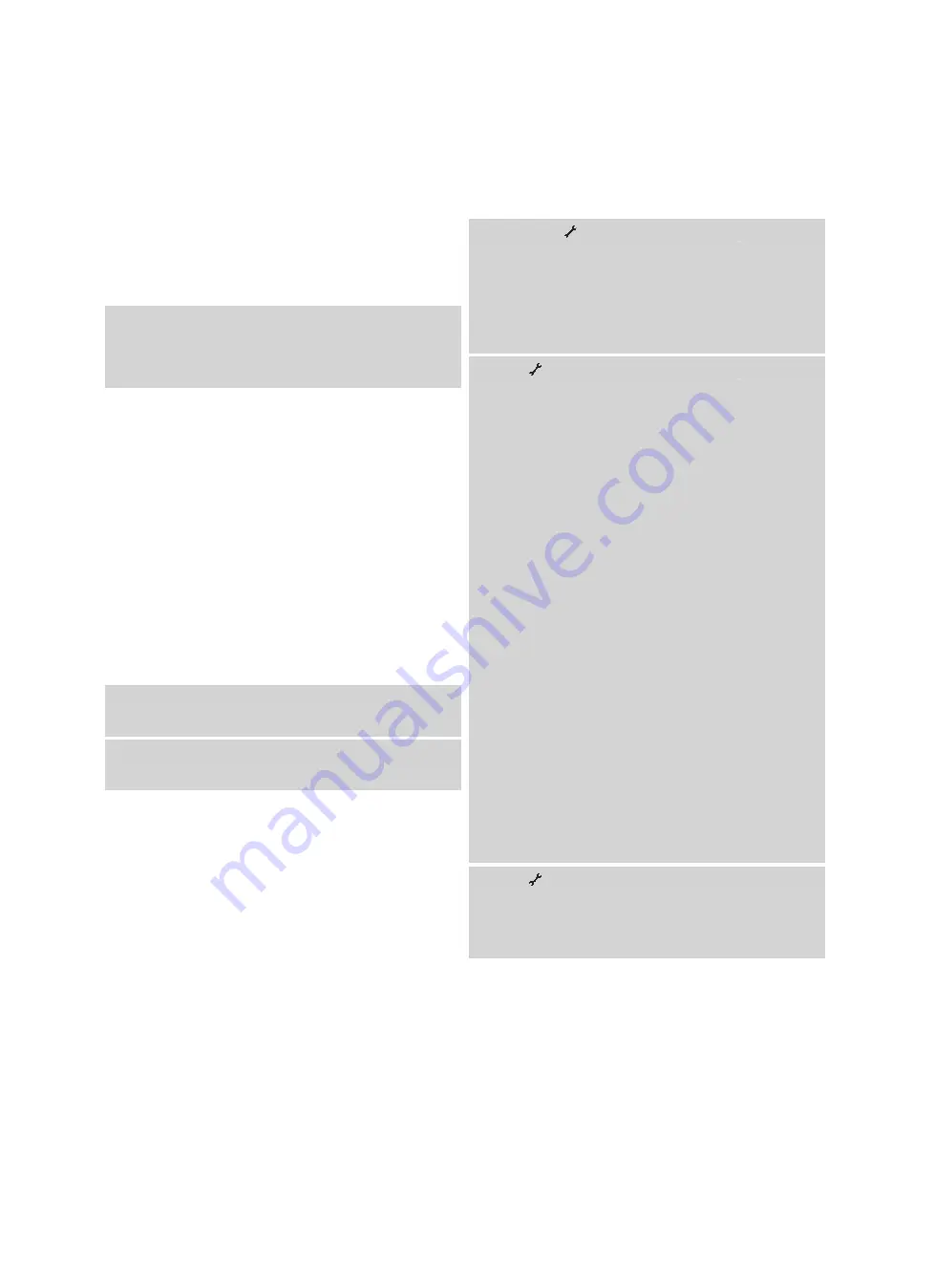
0020193968_05 ecoTEC exclusive Installation and maintenance instructions
39
14.
Retighten the cap nuts and the lock nuts on the cold
water inlet.
15.
Open the cold water stop valve.
12.12 Checking the impeller sensor
▶
Check the impeller sensor for dirt/damage.
12.13 Checking the pre-charge pressure for the
internal expansion vessel
1.
Close the service valves and drain the product.
2.
Measure the pre-charge pressure of the expansion
vessel at the vessel valve.
Condition
: Pre-charge pressure < 0.075 MPa (0.75 bar)
▶
Ideally, you should top up the expansion vessel with ni-
trogen. Otherwise, top it up with air. Ensure that the drain
valve is open when topping up.
3.
If water escapes from the valve of the expansion
vessel, you must replace the expansion vessel
(
→
Page 42).
4.
Fill the heating installation. (
→
Page 29)
5.
Purge the heating installation. (
→
Page 30)
12.14 Checking the filling pressure of the heating
installation
1.
Check the filling pressure of the heating installation and
top up with heating water, if necessary.
2.
Fill the heating installation. (
→
Page 29)
3.
Purge the heating installation. (
→
Page 30)
12.15 Checking the water flow rate (domestic hot
water)
1.
Check the water flow rate (domestic hot water).
Condition
: Insufficient water flow rate
▶
Check the incoming water supply.
Condition
: Sufficient incoming water supply
▶
Clean the filter in the cold water inlet. (
→
Page 38)
12.16 Checking the quality of the heating water
▶
Check the quality of the heating water. (
→
Page 27)
12.17 Completing inspection and maintenance
work
▶
Start a test operation after the maintenance.
▶
Check the heating mode and domestic hot water genera-
tion.
▶
Check the gas type. (
→
Page 18)
▶
Check the gas flow pressure. (
→
Page 30)
▶
Calibrate the heat generator and measure the CO/CO
₂
content and the gas flow in heating mode. (
→
Page 31)
▶
If required, reset the maintenance interval. (
→
Page 36)
▶
Check the product for tightness. (
→
Page 32)
▶
Install the front casing.
▶
Fill out the relevant Service Record section in the Bench-
mark Checklist.
12.18 Checking the product for leak-tightness
▶
Check that the product is leak-tight. (
→
Page 32)
13 Troubleshooting
13.1
Comfort protection mode for the heat cell
Condition
: Neither
nor a fault code
F.xx
are shown in the display
Unusual operating noises are emitted from the heat cell in
the product.
▶
Check whether
S.40
is displayed in
Live monitor
.
If
S.40
is displayed, the product is in a temporary test mode,
which it will exit again automatically.
Condition
:
is displayed.
The
Live monitor
shows
S.40
and
D.118
is at 0. The heat
cell is in permanent comfort protection mode. This is not
caused by the all-gas sensor.
▶
Decommission the product and check the entire air/flue
pipe.
▽
Are there any blockages or leakages?
▶
Eliminate the cause.
▽
Are any components damaged?
▶
Replace the defective components.
▶
If the air/flue pipe is OK, restart the product.
▶
Prepare the flue gas analyser for checking the recircula-
tion.
◁
The measuring probes must be rinsed and must not
be contaminated by a previous measurement.
▶
Check for recirculation at the air test point. The following
measured values are indicators of recirculation.
–
Oxygen value in the intake air: < 20 vol. %
–
Intake air CO value: > 20 ppm CO more than in the
ambient air
▽
Recirculation is present.
▶
Eliminate the deficiencies in the air/flue pipe.
▽
No recirculation is present.
▶
Ensure that there is a heat requirement. In the
Live Monitor, check whether the product has the
status
S.04
or
S.14
.
▶
If the combustion values are not OK, carry out check
programmes
P.04
and
P.14
.
Condition
:
and
F.55
are displayed
The
Live monitor
shows
S.40
and
D.118
≥
1. The heat cell
is in permanent comfort protection mode.
▶
Check and, if required, replace the all-gas sensor.