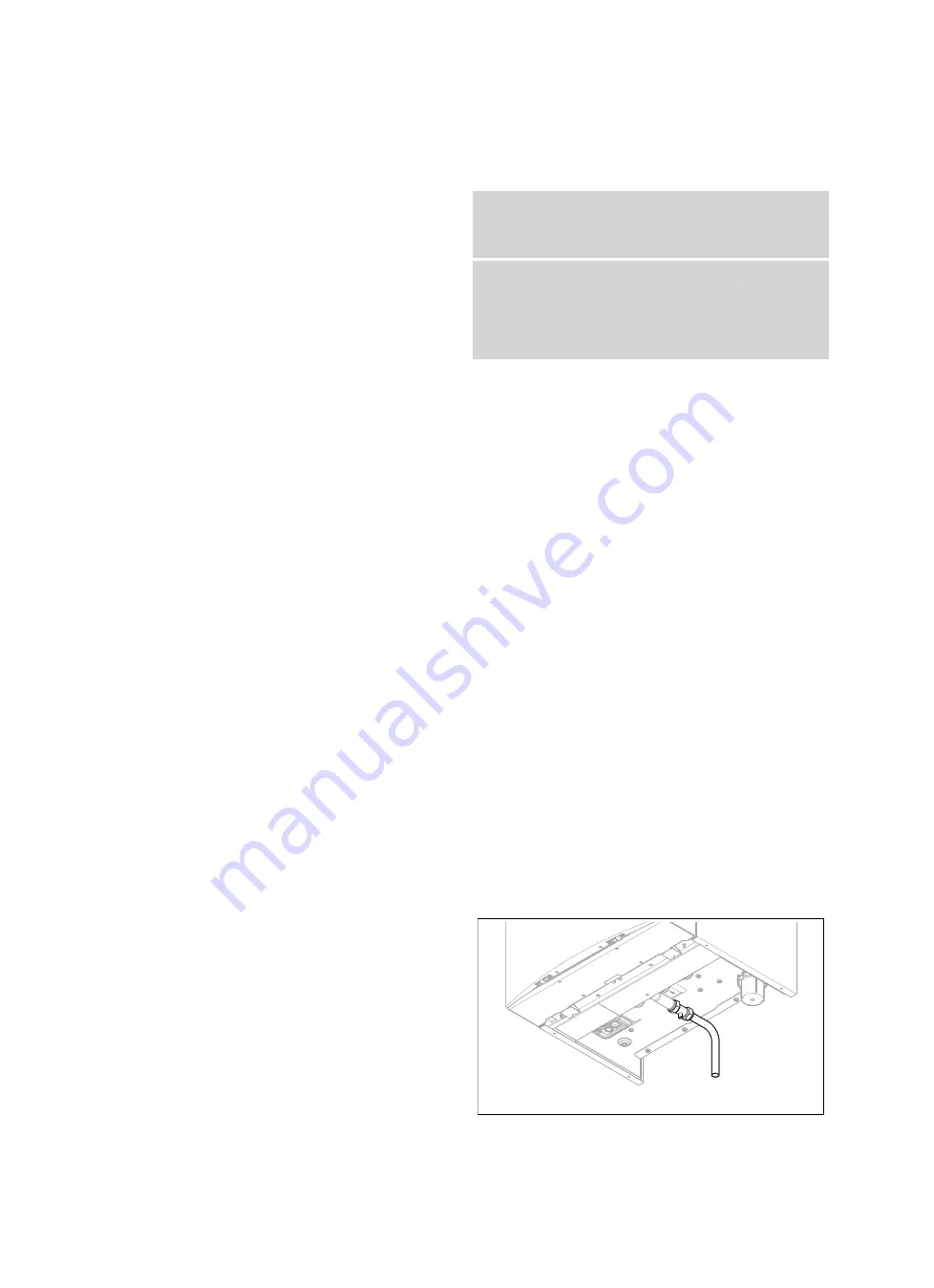
18
Installation and maintenance instructions ecoTEC exclusive 0020193968_05
7
Installation
7.1
Installation requirements
7.1.1
Information on liquefied petroleum gas
operation
In the as-supplied condition, the product is preset for opera-
tion with the gas group indicated on the data plate.
If you have a product that is preset for operation with nat-
ural gas, you must replace the gas family coding resistor with
the enclosed coding resistor for liquefied petroleum gas dur-
ing the installation. During start-up, the product must be con-
verted for operation with liquefied petroleum gas in the in-
stallation assistant. You do not require a conversion set, be-
cause the product has a gas-adaptive heat cell, which is set
independently to the relevant gas type within the gas family.
The gas type can also be changed at a later point using dia-
gnostics code
D.087
.
Furthermore, for operating with liquefied petroleum gas, the
differential pressure sensor must be replaced with a bypass
since, otherwise, this may lead to fault messages. The by-
pass is available as an accessory.
If you have selected the "liquefied petroleum gas" gas type,
after the start-up process is complete, affix the enclosed
"Liquefied petroleum gas" conversion sticker onto the data
plate and affix the enclosed tank sticker (propane quality) so
that it is clearly visible on the tank or the cylinder cabinet, if
possible close to the filler nozzle.
7.1.2
Purging the liquid gas tank
If the liquid gas tank is not purged properly, this may result in
ignition problems.
▶
Ensure that the liquid gas tank has been purged properly
before installing the product.
▶
If required, contact the filler or the liquid gas supplier.
7.1.3
Using the correct gas type
Using the incorrect gas type may cause fault shutdowns in
the product. Ignition and combustion noise may occur in the
product.
▶
Only use a gas type from the gas group that is defined on
the data plate.
▶
Check whether the gas type that is available at the in-
stallation site and the gas type that is set in the product
are the same.
▶
To do this, check the setting for diagnostics code
D.087
.
(
→
Page 33)
7.2
Preparing for installation
1.
Make sure that the existing gas meter is capable of
passing the rate of gas supply required.
2.
Consider the maximum heat output given in DHW
mode.
3.
Install a system separator (to be provided on-site) dir-
ectly on the cold water connection for the combi boiler.
4.
Install the following components:
–
Draining cocks at the lowest points in the heating
installation (
→
current version of "BS 2879")
–
A stopcock on the cold water connection
–
A stopcock in the gas pipe
5.
Check that the volumetric capacity of the expansion
vessel is sufficient for the system volume.
Condition
: The volume of the installed expansion vessel is insufficient
▶
Install an additional expansion vessel, connected as
close to the product as possible, in the heating return.
Condition
: External expansion vessel installed and warm start active
▶
Install a non-return valve in the product outlet (heating
flow) or decommission the internal expansion vessel in
order to prevent the warm start function from being in-
creasingly activated due to backflow.
6.
Install the connection pipes such that they are free
from mechanical stress.
7.
If you use non-diffusion-tight plastic pipes in the heat-
ing installation, ensure that no air gets into the heat
generator circuit.
8.
Only solder connectors if the connectors are not yet
screwed to the service valves.
9.
Only bend connection pipes if they have not yet been
connected to the product.
10.
Flush the heating installation thoroughly before in-
stalling the product.
11.
If, during gas leak-tightness tests, you also place the
gas pipes and the gas valve assembly in the product
under pressure, use a max. test pressure of
≤
11 kPa
(110 mbar).
12.
If you cannot limit the test pressure to 11 kPa
(110 mbar), close any gas stopcocks that are installed
upstream from the product before you carry out the gas
leak-tightness test.
13.
If, during gas leak-tightness tests, you have closed the
gas stopcock that is installed upstream of the product,
relieve the gas line pressure before you open this gas
stopcock.
14.
Install a tundish with condensate siphon for the con-
densate discharge and the exhaust pipe on the expan-
sion relief valve. Route drain pipework that is as short
as possible, at a downward gradient away from the tun-
dish.
15.
Insulate bare pipes exposed to environmental influ-
ences to protect them from frost using suitable insula-
tion material.
7.3
Installing the gas connection
1.
Install the gas line in accordance with the recognised
rules of technology.