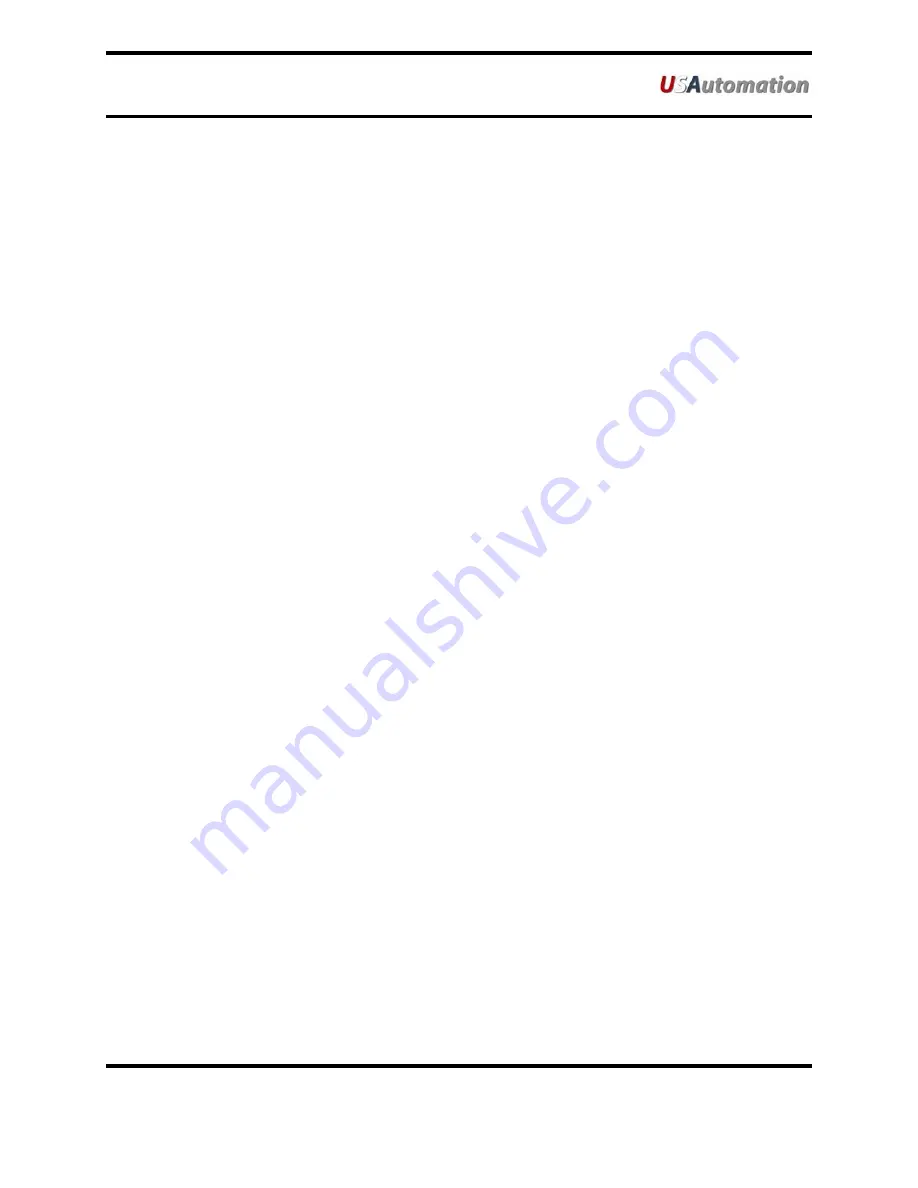
USA57 Revision
1.2
97
It is also possible to use the potentiometer to set the magnitude of the velocity and Switch1
input to be the direction of the velocity. Bit 7 Enables this.
Entering a /
1ad100am1000n65664z0P0R
command
starts the mode. (65664=65536+128)
This feature is available in Firmware V6.998+.
Further, it is possible to know if the shaft is following the commanded velocity, by using a shaft
encoder for feedback and setting the encoder ratio (
aE
) and the following error (
aC
), and setting
n16 mode to report overloads 65552 = (65536 + 16).
Example:
/1ad100aC400am128n65552aE12800z0P0R
If the potentiometer velocity mode is to be used with limit switches, the limits can be switched to
the two switch inputs, so as not to interfere with the potentiometer. The command to do this is
/1an16384R
.
Example:
/1ad100am1000an16384n65538z0P0R
switches the limits to the alternate inputs, and
enables limits (65536 +2 = 65538).
Potentiometer Position Feedback
This feature is available in Firmware V6.7+.
Potentiometer 1 can be used as an encoder for the motor. The value read back is from 0-16368.
NOTE: Please read Appendix E on encoder feedback mode first. Operation in potentiometer
position feedback mode is identical to encoder feedback mode except that the potentiometer
acts as an encoder which generates positions between 0 and 16386.
The command
/1N3R
designates Potentiometer 1 as the encoder (in place of the quadrature
encoder).
To use this mode:
1. Wire a 500-ohm linear taper potentiometer to the Potentiometer 1 position.
2. Connect the motor shaft to the shaft of the potentiometer, such that a move in the positive
direction for the motor increases the value read from the potentiometer using the
/1?aa
command.
3. Turn the potentiometer all the way to zero by issuing a
D
command, e.g.
/1D1000R
.
4. Issue a
/1z0R
command
to zero the motor position.
5. Issue a
/1N3R
command
to enable the potentiometer as encoder.
6. Move motor by issuing
P
commands until it is at about ¾ of the potentiometer range.
7. Issue a
/1aE0R
command
to automatically work out the “encoder ratio” for the
potentiometer.
8. Issue a
/1n8R
command
to enable feedback mode.
Note that if the motor shaft is forced, a correction will be issued to return the motor to its original
position.
If the shaft oscillates at some positions, this may be because of a nonlinearity in the
potentiometer. Try increasing the dead band set by the “
aC”
command. Or it could be because
Содержание Accuriss 57 Series
Страница 1: ... USA57 Revision 1 2 Accuriss 57 Series Integrated Motor Drive Control System USA57 USER S MANUAL ...
Страница 4: ...USA57 Revision 1 2 4 Appendix I 101 Appendix J 103 ...
Страница 11: ...USA57 Revision 1 2 11 ...
Страница 102: ...USA57 Revision 1 2 102 Encoders must have 0 2V Low to 4V High swing at the input of the connector ...