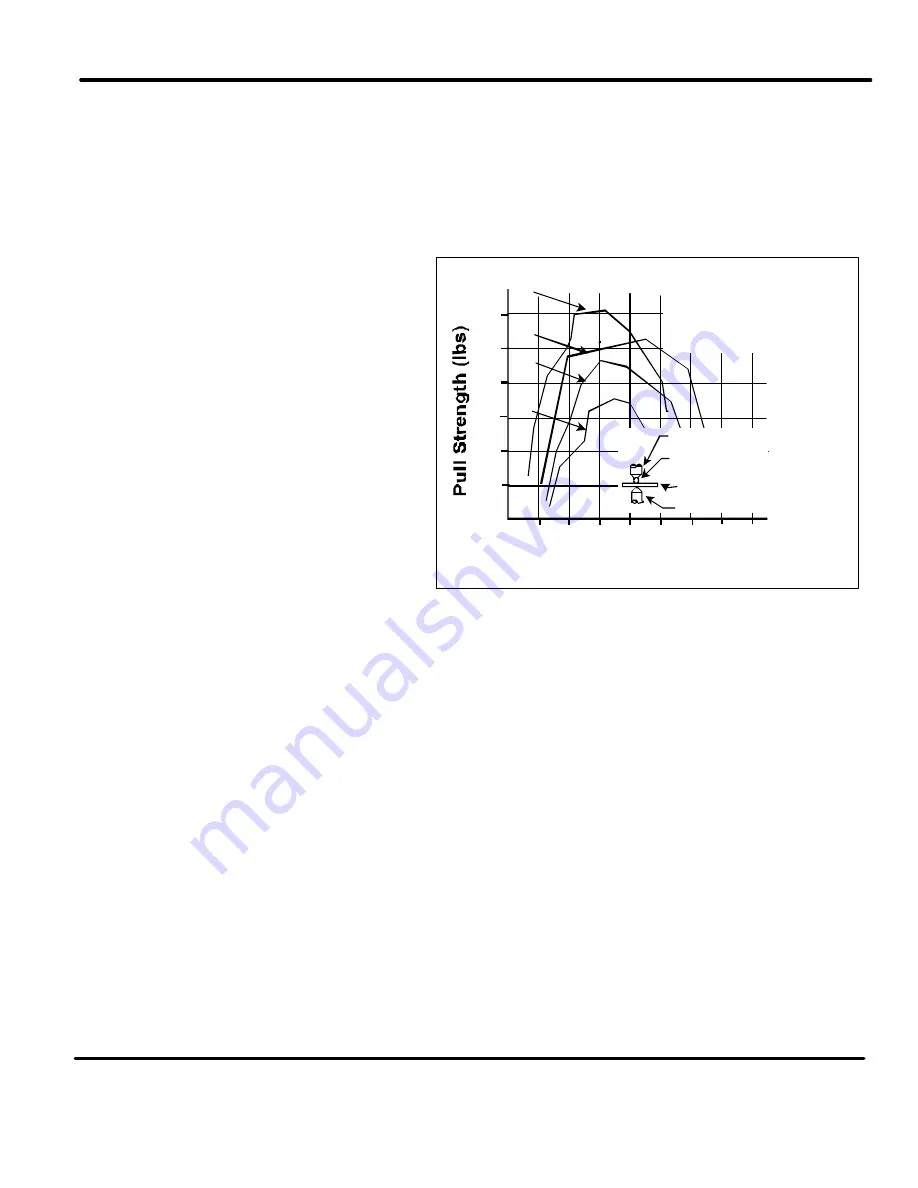
CHAPTER 3: OPERATING INSTRUCTIONS
PHASEMASTER™ 6 DIRECT ENERGY WELDING CONTROL
990-083
3-21
14
12
10
8
6
4
2
20
30
40
50
60
70
80
90 100
A = 8 lbs
B = 10 lbs
C = 12 lbs
D = 14 lbs
Energy (watt seconds or % Current)
Electrode Force
A
B
C
D
MOLY
.032 DIA TINNED
COPPER WIRE
0.010 X 0.030 Ni RIBBON
RWMA 2
Figure 3-5. Typical Weld Strength Profile
Weld Strength Profiles
Weld strength profiles are graphic presentations of the varying effects of %CURRENT and electrode force. To
make a weld strength profile, start at an initial energy setting, make four or five welds, and perform pull tests for
each weld. Calculate the average pull strength. Increase the %CURRENT and repeat the procedure. Continue to
increase the %CURRENT until any unfavorable characteristic occurs, such as sticking or spitting.
Perform pull tests and plot the results of
%CURRENT versus Pull Strength (see figure 3-
5). Repeat this procedure for different forces and
plot a separate curve for each electrode force.
Repeat this procedure using the longer pulse
width.
In figure 3-5, Curve C shows the highest pull
strengths but the lowest tolerance to changes in
weld energy. Curve B shows a small reduction in
strength but considerably more tolerance to
changes in weld energy.
Weld energy/current will vary as a result of
material variations and electrode wear. Curve B is
preferred since it shows more tolerance to
changes in weld energy and has nearly the same
bond strength as Curve C. A comparison of weld schedules for several different applications might show that they
could be consolidated into one or two weld schedules. This would have obvious manufacturing advantages.
Destructive Testing
Destructive Testing can be performed on the actual workpiece or on test specimens. For small, inexpensive parts,
actual production samples, taken on a random basis, should be used. Destructive tests made on spot welds include
tension, tension-shear, peel, impact, twist, hardness, and macro-etch tests. Fatigue tests and radiography have also
been used. Of these methods torsional shear is preferred for round wire and a 45 degree peel test for sheet stock.
Содержание PHASEMASTER 6
Страница 6: ...PHASEMASTER 6 DIRECT ENERGY WELDING CONTROL vi 990 083...
Страница 11: ......
Страница 34: ...CHAPTER 3 OPERATING INSTRUCTIONS PHASEMASTER 6 DIRECT ENERGY WELDING CONTROL 3 6 990 083...
Страница 37: ...CHAPTER 3 OPERATING INSTRUCTIONS PHASEMASTER 6 DIRECT ENERGY WELDING CONTROL 990 083 3 9...