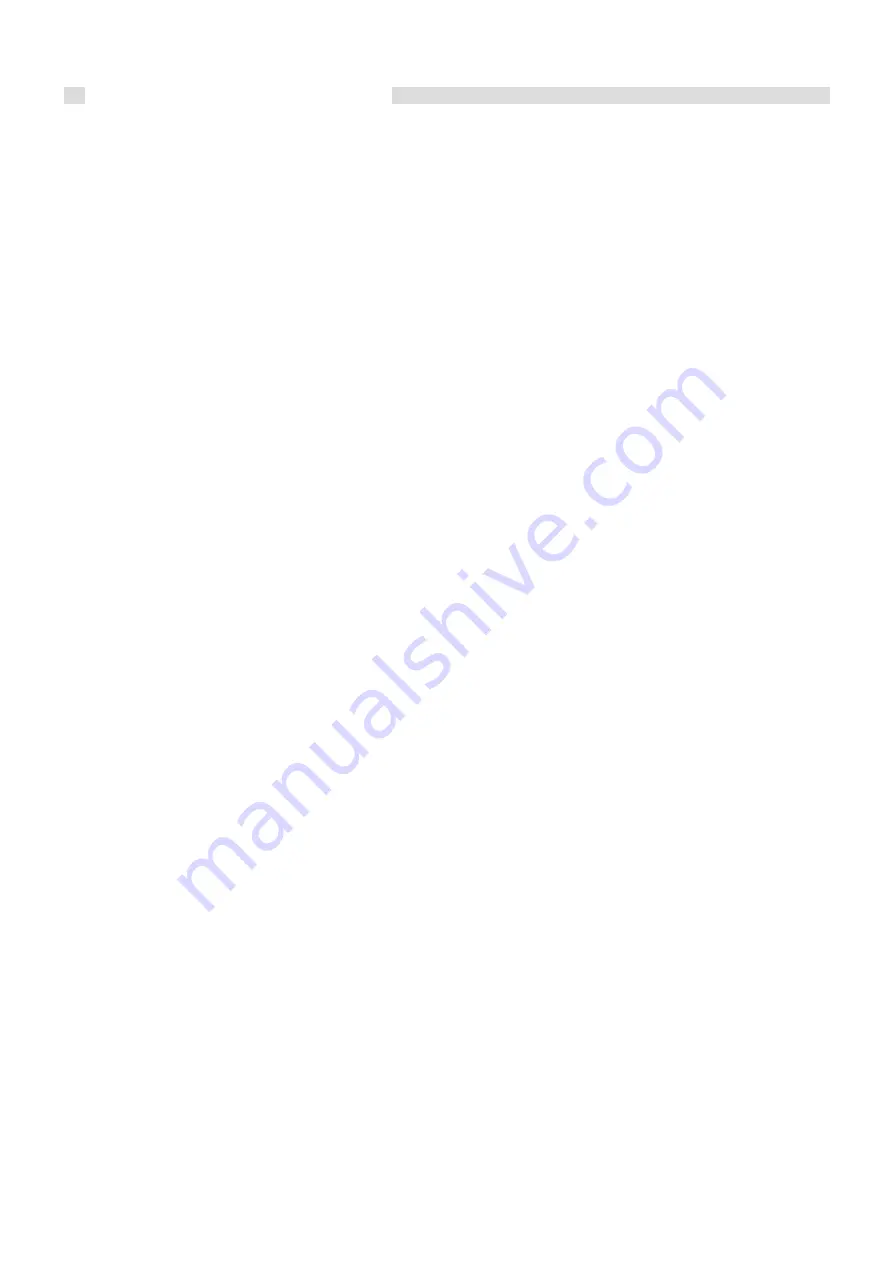
20
Instructions for the installer
3.14 - SHELL INSTALLATION
I) Insert the bulbs into the sheaths of the instruments as
shown in fig. 13, route the cables through the side fairlead
on the side where you want to go out and make the
electrical connection of the panel control to the power
line, to the burner and any eventual pumps, etc..
Replace the box cover of the electric board.
Fix the support plate of the fairlead (item 12) on two side
Fix the side cover plate (item 13) on the left side
J) Attach to the side panels the front panels pos. 16 and 17.
K) Put the upper front panel pos. 14 and attach it by pressing
the two side panels.
L) Fix the two crossbeams can. 19 to the rear panel pos. 18.
Fasten the panel to the rear side panel lower left .
Secure the two panel pos. 20 at the rear side panel lower
right corner.
Combine the two rear panels with reinforcing profile pos.
21.
M) Fix the top rear panel to the two side upper panels
N) Place the top rear panel pos. 23 and attach it by pressing
to the two side panels.
O) Fix the boiler labels and installation data (Item 24) to the
side panel after degreasing it with a suitable solvent.
The plates are inserted into the envelope documents
A) Fix the support brackets (item 1 and 2) of the below hip
shell to the boiler by 8 screws M 6x20 and the associated
nuts and washers.
B) Install the bottom insulation of the boiler (Item 3) and fix
the two strips joints with elastic pegs (item 5) provided in
the accessory box, hooked to the outer fabric insulation.
C) Install the upper insulation of the boiler (item 4) and fix
the two strips joints with elastic pegs (item 5) provided
in the accessory box, hooked to the outer fabric of the
bottom insulation
D) Install the front insulation (Item 6) on the hinges.
E) Install the insulation back pos. 7.
F) Put the lower side panels (item 8 and 9) with the lower
fold in the L profiles on the support basis of the boiler, and
hooking the top part in the cuts on the brackets pos. 1 and
2.
G) Lift forward the cover of the control panel after unscrew the
two side screws with a screwdriver and drive in holes on
the base the entering electrical cables and the capillaries
of output the probe.
Fasten the control panel to the right above side panel (item
11).
H) Place the side panels above (Item 10 and 11) by engaging
side panels below and fitting the upper part in the cuts
expected on the plates of the boiler.
Содержание INOXIA GJ Series
Страница 1: ...INOXIA GJ INSTALLATION AND SERVICING MANUAL 00335290 1st edition 04 11...
Страница 21: ...21 Instructions for the installer fig 12 5 24 4 8 10 12 13 6 3 1 2 7 23 20 14 19 17 21 18 1 2 11 9 16 12 15...
Страница 54: ......
Страница 55: ......