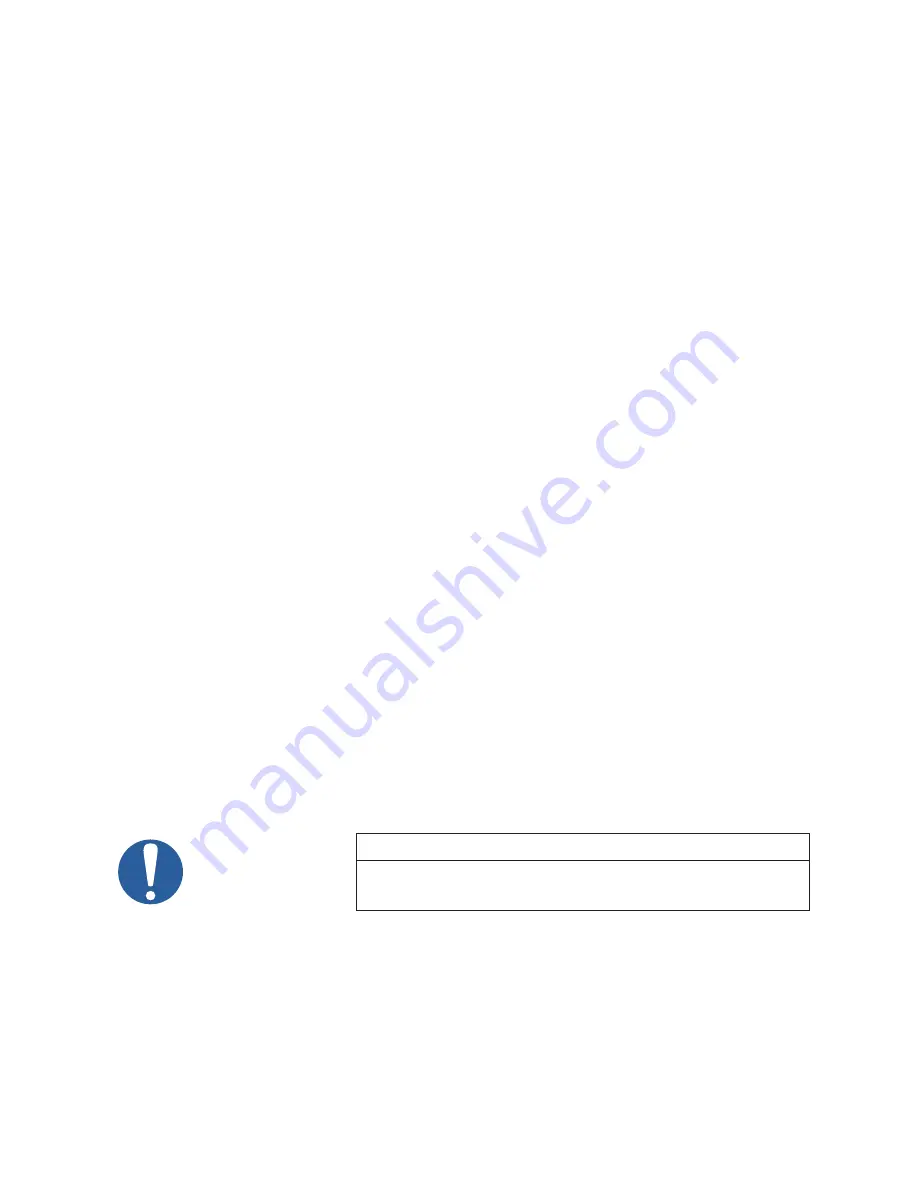
38
11. Put sealer on rotor housing, same as above. Install free end plate and secure in same manner.
12. Install seal mating rings as was done in Step 4. Install one bearing spacer (57) on each shaft. Lubricate
shafts and install roller bearing with inner race flange outward. See Figure 19. Install second bearing
spacer (57) on each shaft. Install oil retainer rings (14) and cap screws (30). Install roll pin (68)
washers (25), oil slinger (20) (on drive rotor), lock tabs (59) and bolts (29). Bend over tabs.
13. Install mounting feet (304) with machined surface against housing and secure with lockwashers (80)
and cap screws (307). Install lifting lugs (195) with cap screws (196).
10.2.3 ADJUSTING ROTOR INTERLOBE CLEARANCE
14. The driven gear is made of two pieces. The outer gear shell is fastened to the inner hub with four cap
screws and located with two dowel pins. A laminated shim, made up of .003” (.076 mm) laminations,
separates the hub and the shell. By removing or adding shim laminations, the gear shell is moved
axially relative to the inner hub. Being a helical gear, it rotates as it is moved in or out and the driven
rotor turns with it, thus changing the clearance between rotor lobes. Changing the shim thickness
.014” (.36 mm) will change the rotor lobe clearance .005” (.13 mm).
EXAMPLE: Referring to Figure 15, check the clearance at AA (right hand reading) and BB (left hand
reading). If AA reading is .017” (.43 mm) and BB reading is .004” (.10 mm), by removing.018” (.46
mm) shims, the readings should then read AA .011” (.28 mm) and BB .010” (.25 mm).
To determine the amount of shim to add or remove, subtract the smaller reading from the larger and
multiply the result by 1.4. (.017” [.43 mm] -.004” [.10 mm] = .013” [.33 mm] × 1.4 = .018” [.46 mm])
If the right side reading is higher than the left side, remove shim. If the right side reading is lower,
add shim. The final readings should be within .002” (.05 mm) of each other. When removing gear
shell from driven gear, it is not necessary to remove gear lock bolt. Make sure bolt locks are in place
because the dowel pins must come off with the gear shell.
15. Install oil slingers (395) back to back on drive shaft flange. Make sure both mating surfaces are clean
and free of burrs-then mount drive shaft to gear and secure with-nylok cap screws (29). Check drive
shaft runout at seal journal. Do not exceed .003” (.08 mm) T.I.R.
16. Remove temporary cap screws from gear end of housing and place bead of silicone around the
periphery of the end plate. Encircle the dowel pins. Install cover (6) and cap screws (26). The use of
two ½”-13 threaded rods as guide screws is recommended.
10.2.4 DRIVE SHAFT SEAL ASSEMBLY
17. Follow steps as listed below:
a. Install O-ring (75) into seal housing (91) and press in stator portions of mechanical seal (54) see
special tool drawing. Clean face of carbon and mating ring with soft tissue and acetone. Install
O-ring (92).
NOTE
Failure to properly pull this gear could result in damage to rotor keyway or
a bent rotor shaft. Never use excessive force.
b. Lubricate O-ring in ID of mating ring and carefully slide onto drive shaft with slot up and seat against
shoulder. Do not use any tools. Lapped surface should be facing outward.
c. Install seal housing (91) into cover bore and secure with four hex head screws (93).
d. With set screws (90) in place install mating ring retainer (89) (flange facing outward) while aligning
pin (300) with slot in mating ring. Secure to shaft with set screws.
e. Install dust washer (82) and secure with three hex head screws (111).
18. Install free end cover (7) same as gear end.
Содержание M-D Pneumatics 7010
Страница 43: ...43 NOTES ...
Страница 50: ...50 3200C CUTAWAY DRAWING 3200 90C 91C 92C 93C 1 OF 2 A ...
Страница 51: ...51 3200C CONFIGURATIONS DRAWINGS 3200 90C 91C 92C 93C 2 of 2 A ...
Страница 54: ...54 5500C CUTAWAY DRAWING 5500 90C 91C 92C 93C 1 OF 2 E OIL LEVEL SIGHT GAUGE DETAIL ...
Страница 55: ...55 5500C CONFIGURATIONS DRAWINGS 5500 90C 91C 92C 93C 2 of 2 E ...
Страница 56: ...56 7000C CUTAWAY DRAWING 7000 90C 91C 1 OF 3 ...
Страница 57: ...57 7000C CONFIGURATIONS DRAWING 7000 90C 2 OF 3 ...
Страница 58: ...58 7000C CONFIGURATIONS DRAWING 7000 91C 3 OF 3 7000 91C 7013 SHOWN ...
Страница 68: ...68 NOTES ...