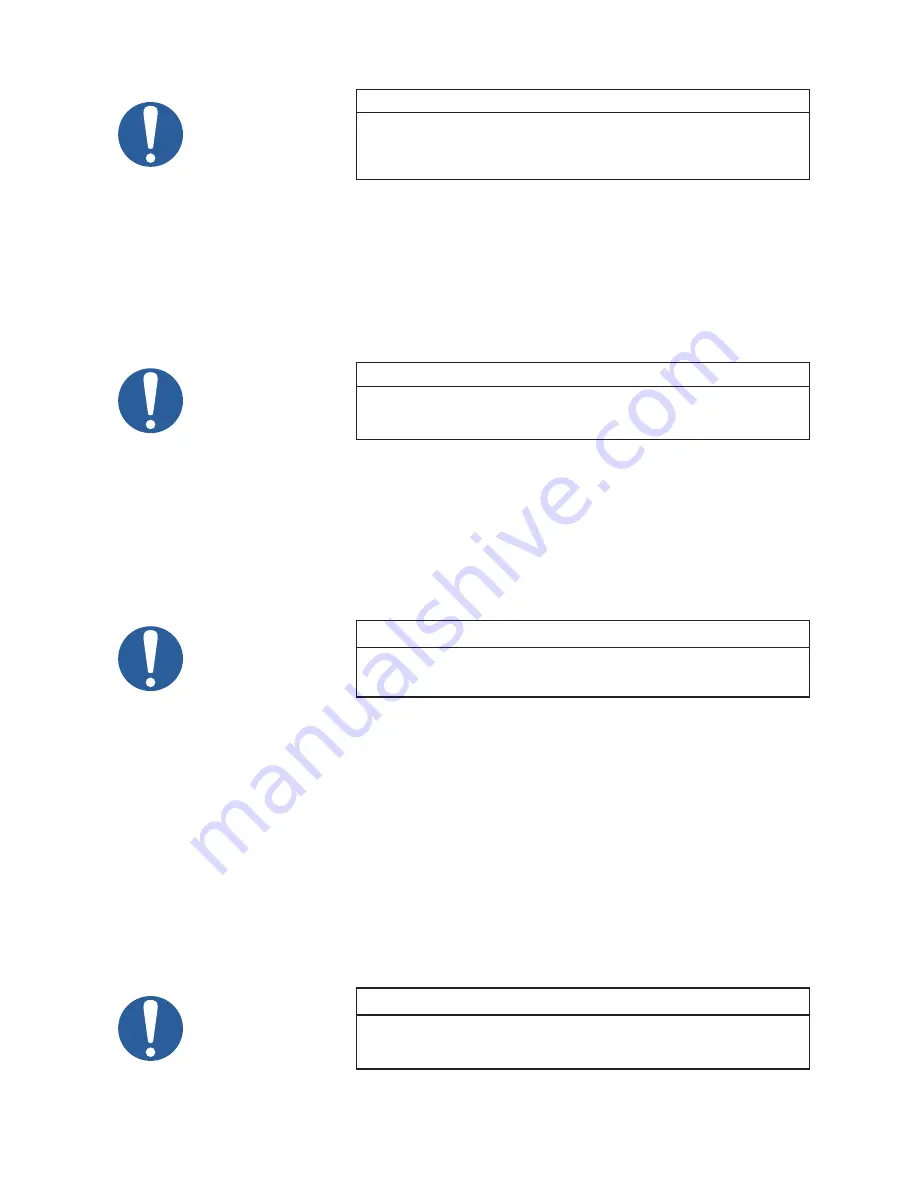
28
6. Lubricate shafts and press the double row ball bearings [9] onto rotor shafts and into end plate bores.
NOTE
These bearings have been flush ground at the factory. The inner race will
have a black dot etched on the surface. This dot must be up and visible
when bearings are installed. Secure with bearing retainers (14) and socket
head screws (30).
7. Check clearance between the face of the end plate and rotor lobes. See
Assembly Clearances
table
on page 41 for correct gear end clearances. If clearances are not within specifications, recheck parts to
find cause of improper clearances before proceeding.
8.2.3 INSTALLATION OF TIMING GEARS
8. Install spacer [17] (.260” {6.60 mm} thickness) on one shaft and spacer [18] (.200” {5.08 mm} thickness)
and oil slinger [20] on the other shaft.
NOTE
The oil slinger and its spacer should always be mounted on lower rotor for
horizontal flow units.
It can be mounted on either shaft for vertical flow units. Install timing shim in same location as found in
disassembly. This does not necessarily insure the unit will be in proper time. Adjustments can
be made later in the assembly process.
9. Insert gear keys [24] in their proper location and flush with top of shaft. Use the two keyways facing to
the right. A tight fit is required. Coat shafts and keys with lubricant. Install drive gear (right hand helix)
on drive rotor (left side). To install driven gear, align reference marks as shown in Fig. 7. Install driven
gear carefully to avoid damaging any teeth when engaging opposite gear. Secure with spacers [57],
washers [25], and flat head Allen screws [29].
NOTE
All timing gears must be used in sets, as they are matched and serially
numbered.
10. Remove assembly from press and stand on work table with gears down. Place blocks under end plate
to prevent assembly from falling over. Drive gear should remain on left side.
8.2.4 HOUSING AND FREE END ASSEMBLY
11. Place a small bead of sealer around the periphery of the end plate, encircling each bolt hole. Install
rotor housing [3] and secure with 4 screws evenly spaced.
12. Check clearance between end of lobes and housing using a flat bar and feeler gauges or a depth
micrometer. Refer to
Assembly Clearances
table on page 41 for free end clearances.
13. Place a small bead of sealer around the periphery of the housing, encircling each bolt hole. Install free
end plate and secure with 4 screws.
14.
90/91
- Install mating rings same as gear end, No. 5.
92/93
- Install seal slinger same as gear end.
15. Install bearing spacers [123] on each shaft. Lubricate shafts and install roller bearings [10].
NOTE
Inner race of bearing has a flange on one side only. This flange must face
outward. See Figure 14.
16. Install oil retainer rings [14] with button head screws [30]. Only two required for each ring.
Содержание M-D Pneumatics 7010
Страница 43: ...43 NOTES ...
Страница 50: ...50 3200C CUTAWAY DRAWING 3200 90C 91C 92C 93C 1 OF 2 A ...
Страница 51: ...51 3200C CONFIGURATIONS DRAWINGS 3200 90C 91C 92C 93C 2 of 2 A ...
Страница 54: ...54 5500C CUTAWAY DRAWING 5500 90C 91C 92C 93C 1 OF 2 E OIL LEVEL SIGHT GAUGE DETAIL ...
Страница 55: ...55 5500C CONFIGURATIONS DRAWINGS 5500 90C 91C 92C 93C 2 of 2 E ...
Страница 56: ...56 7000C CUTAWAY DRAWING 7000 90C 91C 1 OF 3 ...
Страница 57: ...57 7000C CONFIGURATIONS DRAWING 7000 90C 2 OF 3 ...
Страница 58: ...58 7000C CONFIGURATIONS DRAWING 7000 91C 3 OF 3 7000 91C 7013 SHOWN ...
Страница 68: ...68 NOTES ...