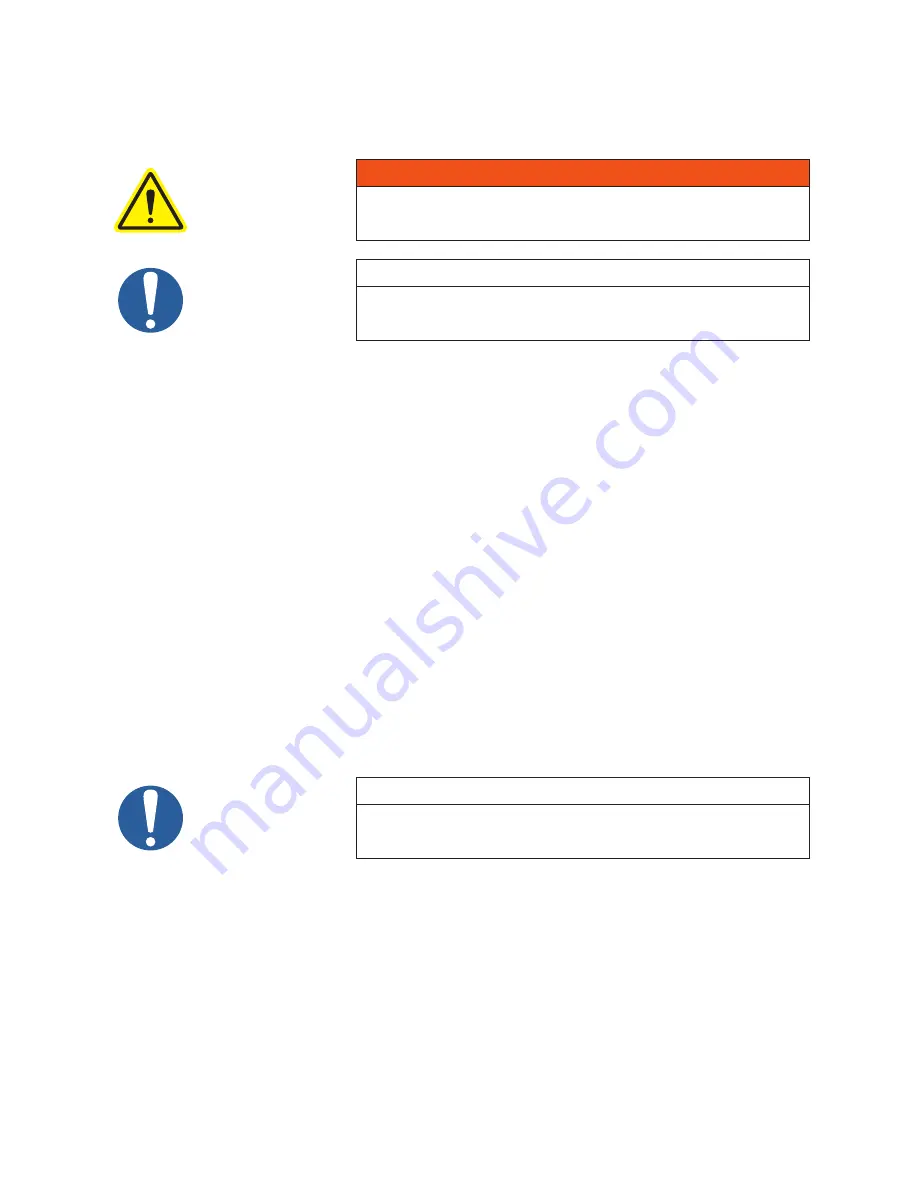
17
Proper gap between coupling halves must be established according to coupling manufacturers instructions
with the motor armature. This will minimize the change for end thrust on the booster shaft. All direct coupled
base mounted units must be re-aligned and greased after field installation.
5.10 MOTOR AND ELECTRICAL CONNECTIONS
WARNING
The motor and connections shall be protected to assure that product and
environmental condensation does not come in contact with the electrical
connections.
NOTE
It is the responsibility of the installer to assure that the motor is in compliance
with the latest edition of IEC 60204-1 and all electrical connections
performed per IEC 60204-1, this includes over current protection.
Wire the motor and other electrical devices such as solenoid valves and temperature switch to the proper
voltage and amperage as indicated on the nameplate of each component being wired. Turn the booster by
hand after wiring is completed to determine that there are no obstructions and if the booster turns freely;
then momentarily start the booster to check the direction of rotation. Figure 2 shows direction of air flow in
relation to rotor rotation. The air flow direction can be reversed by reversing the appropriate motor leads.
5.11 C-FLANGE COUPLING INSTALLATION
Two types of couplings are used: the Wood’s and the Lovejoy L-Type.
5.11.1 WOOD’S COUPLINGS
1. Inspect all coupling components and remove any protective coatings or lubricants from bores, mating
surfaces and fasteners. Remove any existing burrs, etc. from the shafts.
2. Slide one coupling flange onto each shaft, using snug-fitting keys where required.
3. Position the flanges on the shafts. It is usually best to have an equal length of shaft extending into each
flange.
4. Move one flange to its final position. (Usually the motor shaft.) Torque fasteners to proper value.
5. Slide the other flange far enough away to install the sleeve. With the two piece sleeve, do not move the
wire ring to its final position, allow it to hang loosely in the groove adjacent to the teeth. The coupling
employs a two-piece sleeve with a wire ring. Force the ring into its groove in the center of the sleeve. It
may be necessary to pry the ring into position with a blunt screw driver.
NOTE
Coupling sleeves may be thrown from the coupling assembly with substantial
force when the coupling is subjected to a severe shock load or abuse.
5.11.2 LOVEJOY COUPLINGS
1. Type-L sizes L099, L100, L110, L150, and L190 are used.
2. Follow instructions 1 and 2 for Wood’s couplings.
3. Shaft sleeves may be used with this type of coupling to prevent the hubs from sliding back on the shafts
should they come loose. Slide the locking collars on the shafts first. Do not tighten.
4. Position the hubs on the shafts. It is usually best to have an equal length of shaft extending into each
hub. Move one hub to its final position and torque fasteners to proper value.
5. Slide the other hub far enough away to install the spider. Lock the hub in place and slide the locking
collars up against the back of each of the hubs and lock in place.
Содержание M-D Pneumatics 7010
Страница 43: ...43 NOTES ...
Страница 50: ...50 3200C CUTAWAY DRAWING 3200 90C 91C 92C 93C 1 OF 2 A ...
Страница 51: ...51 3200C CONFIGURATIONS DRAWINGS 3200 90C 91C 92C 93C 2 of 2 A ...
Страница 54: ...54 5500C CUTAWAY DRAWING 5500 90C 91C 92C 93C 1 OF 2 E OIL LEVEL SIGHT GAUGE DETAIL ...
Страница 55: ...55 5500C CONFIGURATIONS DRAWINGS 5500 90C 91C 92C 93C 2 of 2 E ...
Страница 56: ...56 7000C CUTAWAY DRAWING 7000 90C 91C 1 OF 3 ...
Страница 57: ...57 7000C CONFIGURATIONS DRAWING 7000 90C 2 OF 3 ...
Страница 58: ...58 7000C CONFIGURATIONS DRAWING 7000 91C 3 OF 3 7000 91C 7013 SHOWN ...
Страница 68: ...68 NOTES ...