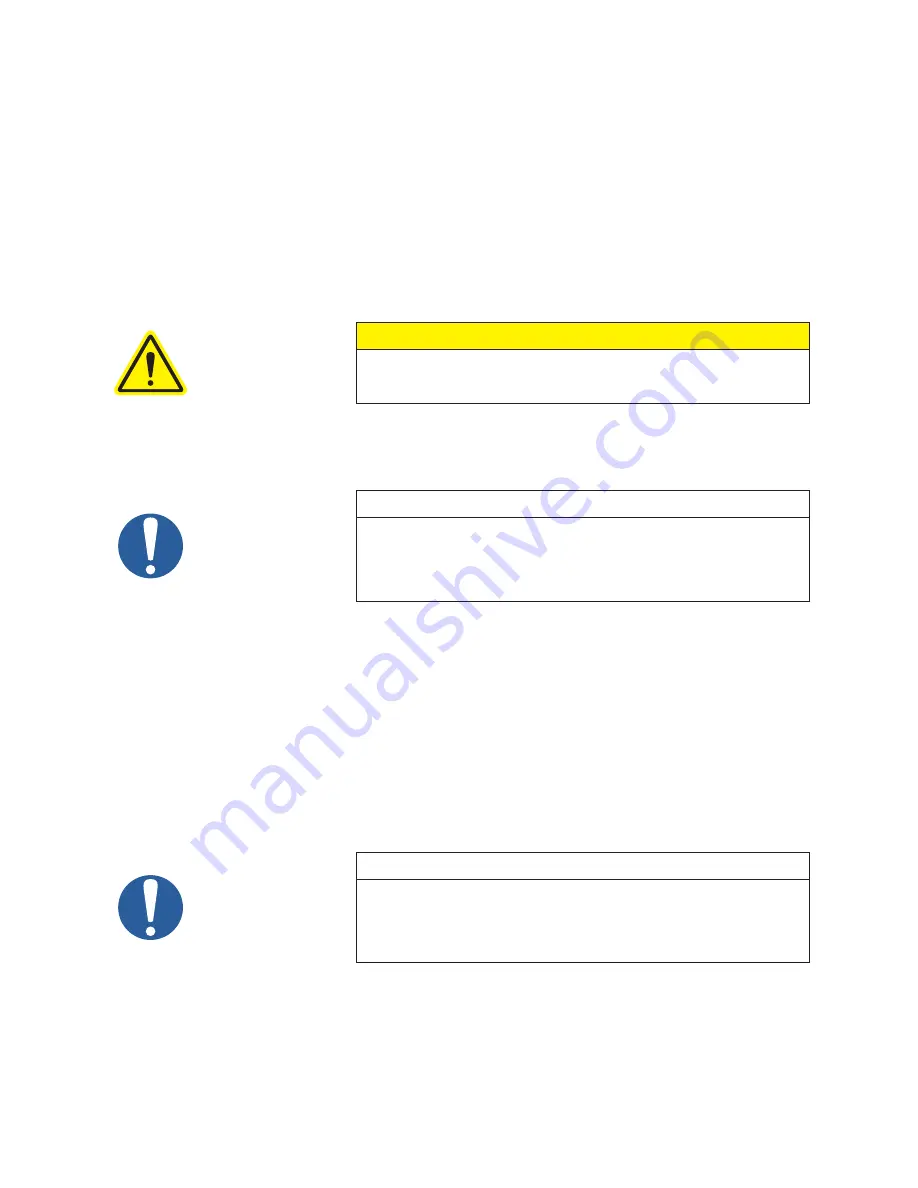
36
8. Repeat procedure used in No. 4 to remove free end cover (7). Remove rotor shaft screws as was
done in No. 6 and also oil slinger (20). Remove cap screws (30) and oil retainer rings (14).
90 Series:
Place ½” eye bolt into both sides of end plate on 90 series, in holes provided for lifting.
91 Series:
Place ½” eye bolt into top of end plate on 91 series.
9. Make up four pieces of threaded rod ½”-13 UNC approximately 9” long with double nuts or a single
welded nut to turn rods. On the opposite ends remove about ½” of threads as this end will mushroom
slightly when jacking end plate. This will prevent threads from jamming when removing rods. Run
in equally to remove end plate. Tap out roller bearings (10). Note that each bearing on this end has
two identical spacers (57), one on each side of bearing. Tap out seals (54) or (12). Also remove the
labyrinth seals (51), as they should be replaced with each overhaul.
90/91 Series:
discard O-ring (75) and retain O-ring spacers (74) for reassembly.
10. Remove cap screws (30) and bearing retainer rings (14) from drive end of unit. Remove rotors (1). To
remove the rotors from the end plate will require either a two-jaw gear puller with jaws inserted in the
oil feed slots of the bearing bore, or a bar-type puller using the tapped holes around the bearing bore.
CAUTION
If rotors are side by side, position the lobes vertically when removing. If
they are one on top of the other, remove top rotor first in a vertical position.
Then position bottom rotor vertically and remove.
11. Support end plate with eyebolts and lift strap. Remove temporary cap screws and tap end plate from
housing (3). Remove bearings and seals.
12. Clean and inspect parts for damage and wear. Replace all O-rings, seals and bearings at each overhaul.
NOTE
If end plates, housing or end covers are not being reassembled in their
original position or some new parts are being used, it will be necessary to
clean all paint or rust build-up from the mating surfaces to insure a good
seal. Failure to do so could result in excessive end clearances and air or
oil leaks.
10.2 ASSEMBLY OF 7000C SERIES BOOSTERS
The assembly procedure is generally the same for all series, but where there are differences, notations are
made. Dowel pins are used to locate end plates, housing and end covers in their proper locations relative
to each other. Be sure they are in place. An O-ring lubricant should be used on all O-rings.
It is recommended that the gear end rotor shaft bearings be purchased from Tuthill Vacuum & Blower
Systems, as they are specially ground to locate the rotors with correct end clearance relative to the gear
end plate.
Make sure all parts are clean and free of any nicks or burrs caused by disassembly. Refer to Special Tool
Drawings on page 44-45.
NOTE
When rebuilding the model 7000 blowers and vacuum boosters and
depending on the series designation, it may be necessary to reseal the
joints between the rotor housing, end plates, and end covers. The sealer,
Loctite 515, is recommended and available for purchase from Tuthill
Vacuum & Blower Systems.
10.2.1 PREPARATION OF END PLATES FOR ASSEMBLY
1. Press the labyrinth seals (51) into seal bores with the lips toward the oil side. ( Note:) For lip seal units
put a light coat of silicone in the seal bore of end plate. Install lip seal open side facing up.
2. Install O-ring spacers (74) with grooves up. Install O-rings (75) making sure they are fully seated in
their grooves. Apply a thin coat of sealer to O. D. of seal (54) and press into seal bore. Make sure seals
are fully seated without deforming. Clean seal carbon with soft tissue and cleaning agent (acetone).
Содержание M-D Pneumatics 7010
Страница 43: ...43 NOTES ...
Страница 50: ...50 3200C CUTAWAY DRAWING 3200 90C 91C 92C 93C 1 OF 2 A ...
Страница 51: ...51 3200C CONFIGURATIONS DRAWINGS 3200 90C 91C 92C 93C 2 of 2 A ...
Страница 54: ...54 5500C CUTAWAY DRAWING 5500 90C 91C 92C 93C 1 OF 2 E OIL LEVEL SIGHT GAUGE DETAIL ...
Страница 55: ...55 5500C CONFIGURATIONS DRAWINGS 5500 90C 91C 92C 93C 2 of 2 E ...
Страница 56: ...56 7000C CUTAWAY DRAWING 7000 90C 91C 1 OF 3 ...
Страница 57: ...57 7000C CONFIGURATIONS DRAWING 7000 90C 2 OF 3 ...
Страница 58: ...58 7000C CONFIGURATIONS DRAWING 7000 91C 3 OF 3 7000 91C 7013 SHOWN ...
Страница 68: ...68 NOTES ...