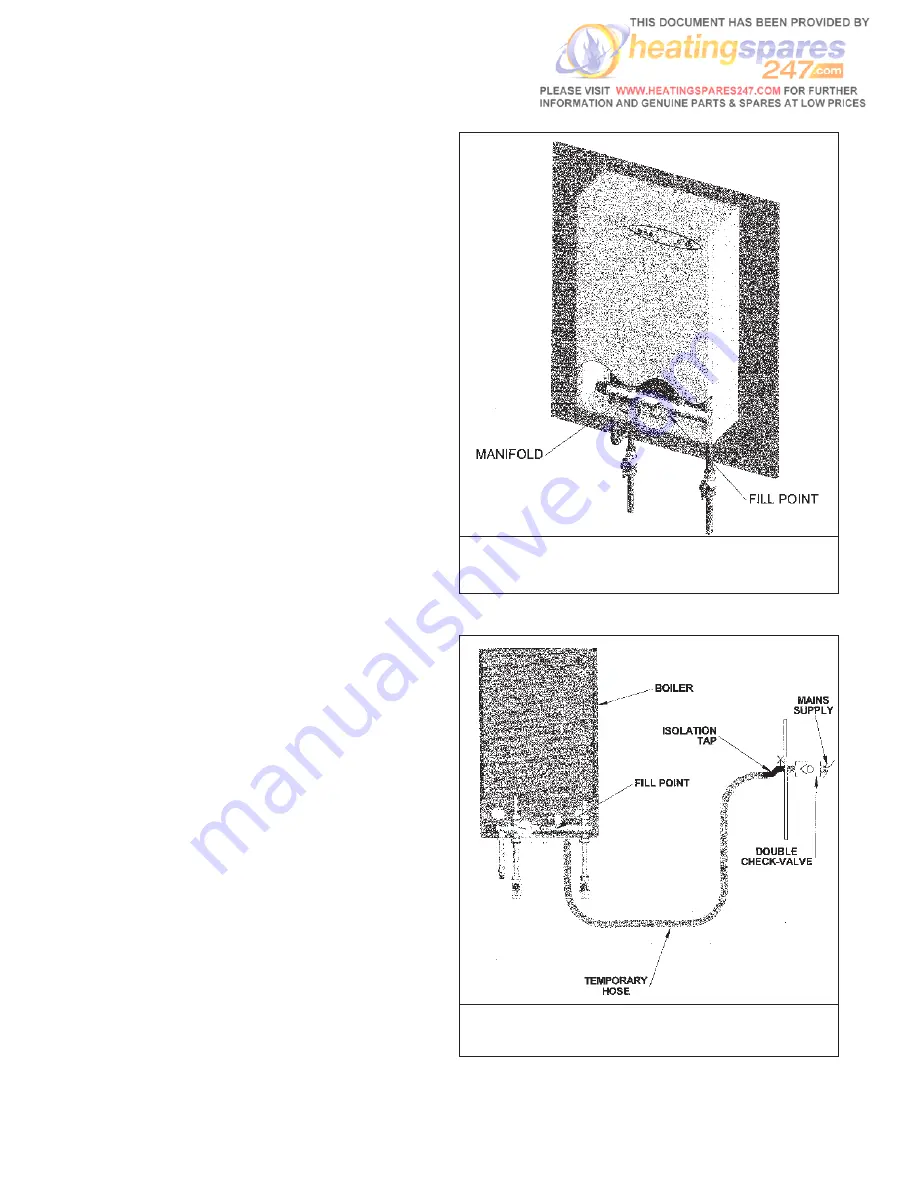
FITTING INSTRUCTIONS (cont.)
FILLING THE SYSTEM
A filling point connection is provided on the front face of
the boiler manifold to facilitate the initial filling and
pressurising of the system via a hose connection
(supplied). Alternatively, a permanent filling-loop may be
employed.
Notes:
a) Before filling, ensure that all fittings and joints
have been made.
b) Thoroughly flush out the system to remove any
swarf and residue from the pipework and
radiator(s).
c) There must be no permanent connection between
the boiler and the mains water supply.
Filling Method 1: Temporary Hose (Figs. 10/11)
1) Connect a hose to the fill point on the manifold
using the fittings supplied.
2) Connect the other end of the hose to the mains
water supply, ensuring that all safety valves are
fitted in the run
(Fig. 11)
to prevent system
water entering the mains supply. Approved hose
unions should be used on all connections.
3) Open the fill point on the manifold
(Fig. 10)
by
turning the isolating knob anti-clockwise.
4) Ensure all isolation valves to the system are open,
that the bypass valve is closed, and that the
automatic air vent contained within the boiler
casings is open (turn the black cap on the device
fully anti-clockwise).
5) Switch on the mains supply to the boiler and test
the pressure relief valve by continuing to fill until
this device activates and releases water into the
drain.
6) Switch off the mains water supply.
7) Using the pressure gauge on the front face of the
manifold for reference, reduce the water content of
the system until the pressure is indicated as 1.5
bar.
8) Thoroughly vent all parts of the system of air and,
if necessary, readjust pressure back to 1.5 bar.
9) Close off the fill connection on the manifold, remove
the hose and close the automatic air vent.
10) Check all joints are water-tight before operating
the appliance.
8
FIG. 10 - FILL POINT
FIG. 11 - FILLING METHOD 1
Содержание Aztec Gold
Страница 14: ...14 FIG 17 BOILER SCHEMATIC ...