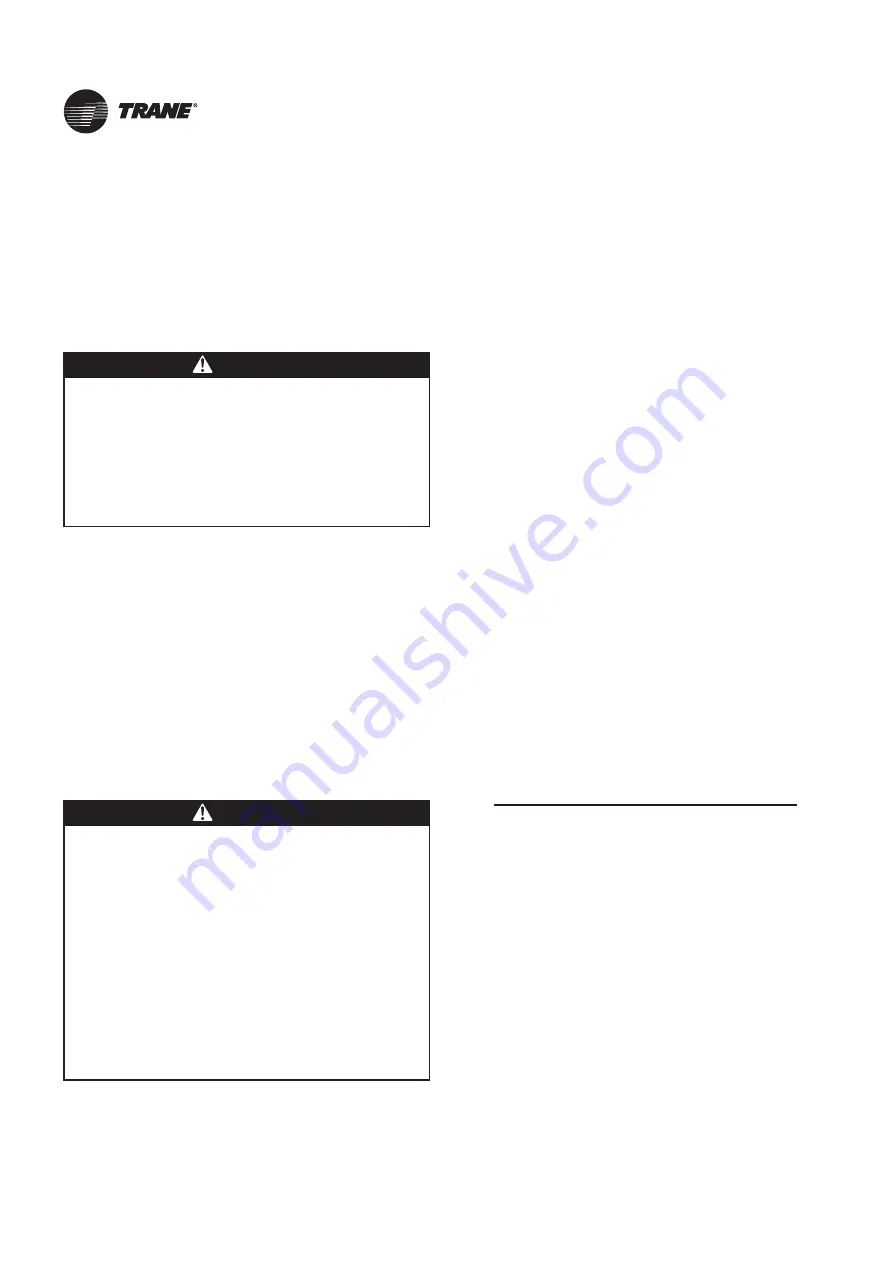
Start-Up
32
CAUTION
The use of untreated or improperly treated water in unit
coils may cause scaling, erosion, corrosion, algae,
smile or other equipment damage. Consult a qualified
water treatment specialist to determine if water
treatment is required. The Trane Company assumes no
responsibility for equipment damage caused by
untreated or improperly treated water.
WARNING
Disconnect electrical power prior to access into a fan or
ductwork. Even when locked out electrically, fans may
cause injury or damage if the impeller is subject to
“wind-milling.” The impeller should be secured to
physically restrict rotational movement. Failure to
secure impeller can cause severe personal injury or
death. Disconnect electrical power source when
connecting or disconnecting electrical wires for test
procedures. Do not open service access doors while
the unit is operating. Failure to exercise caution or while
inspecting. unit operation may result in injury or death
from electrical shock, air movement or rotating parts.
Start-up Procedures
After completing all start-up checks and procedures, the unit
may be started. The following checks and adjustment should
be made during initial start-up:
If the unit was stored for an extended period of time, the
following items should be checked before starting the unit.
1.
2.
3.
4.
5.
6.
Maximum allowable voltage imbalance is two percent. Voltage
imbalance is defined as 100 times the sum of the deviation of
the three voltage from the average, divided by twice the
amperage voltage. For example, if the three measured
voltage are 221, 230, and 227, the average would be 226
volts. The percent of voltage imbalance is then calculated:
In this example, 2.2 percent imbalance is not acceptable and
the power company should be notified to correct it.
7.
8.
Perform the following steps prior to starting the unit.
1.
2.
Inspect electrical connections. They should be clean and
secure. Compare actual wiring with specific diagrams
provided on the unit.
Check piping and valves for leaks. Open or close the
valves to check for proper operation. Drain lines should be
open.
Inspect motor bearings for moisture and rust. Replace
bearings if necessary and re-pack with new grease.
Check motor winding. An acceptable winding resistance
reading is from 6 meg-ohms to infinity. If reading is less
than 5 meg-ohms, winding should be dried out in an oven
or by a blower.
Inspect the entire motor for rust and corrosion.
Lubricate the motor as instructed in the section titled
“Periodic Maintenance”, or as indicated by the
maintenance tag on the motor.
Bump-start unit and observe the fan wheel for proper
rotation, as indicated by rotation arrow located on fan
housing.
Measure the motor voltage and amperage on all phases to
ensure proper operation. The readings should fall within
the range given on the motor nameplate.
Check unit vibration if the fan speed is changed more than
5% from the original designed rpm, or if parts such as
shafts, fan wheels, bearings, or other drive components
are replaced. Do not exceed max. fan rpm.
Pay particular attention to any vibration, noise or
overheating of the motor and fan bearings. (Bearings may
run warm during break in.)
3.
4.
5.
6.
7.
If equipped with a refrigerant coil, charge and leak-test the
unit and get it ready for operation according to instructions
provided with the condenser equipment.
Check that all air filters are in place and positioned
properly. Under Periodic maintenance, see section titled
“Air Filters”.
Close and secure all unit access doors. Check that the
latch set screw are tight.
Remove all foreign material from the drain pan and check
drain opening and condensate line for obstructions.
Prime the DRAIN TRAP.
100 x {[226-221]} + {[230-226[} + {[227-226]}
2 x 226
= 2,2% (unacceptable)
Содержание CLCP Euro 25
Страница 16: ...Assembly Installation CLCP EURO 50 Breakpoint Frame to Frame 16 CLCPEURO 50 Break Point Frame to Frame Joining...
Страница 17: ...17 Assembly Installation CLCP EURO 50 Breakpoint Panel to Frame CLCPEURO 50 Break Point Panel to Frame Joining...
Страница 18: ...Assembly Installation CLCP EURO CLCP EURO XP Paneling 18...
Страница 22: ...Assembly Installation CLCP EURO XP CKD At Jobsite 22...
Страница 23: ...23 Assembly Installation CLCP...
Страница 24: ...Assembly Installation CLCP 24...
Страница 40: ...Maintenance 40 Figure 20 Belt Tension Measurement...
Страница 42: ...Trouble Analysis 42...
Страница 43: ...43 Trouble Analysis Pulley and Belt...
Страница 44: ...Appendix A Fan and Arrangement 44 Fan Discharge Arrangement...
Страница 50: ...Appendix B Filter Layout and Quantity Filter Dimension Nominal and Arrangement HEPA AstroCel VXL Filter 50...
Страница 51: ...Typical Motor Wiring Diagram 51...
Страница 52: ...52 Service Light and Door Switch Wiring...
Страница 53: ...Factory Installed VFD TR200 Wiring Setting 53...
Страница 54: ...Factory Installed VFD TR200 Wiring Setting 54 TR200 BASIC SETTING_OPEN LOOP...
Страница 56: ...Pre Start Up Checklist 56...
Страница 57: ...Pre Start Up Checklist 57...