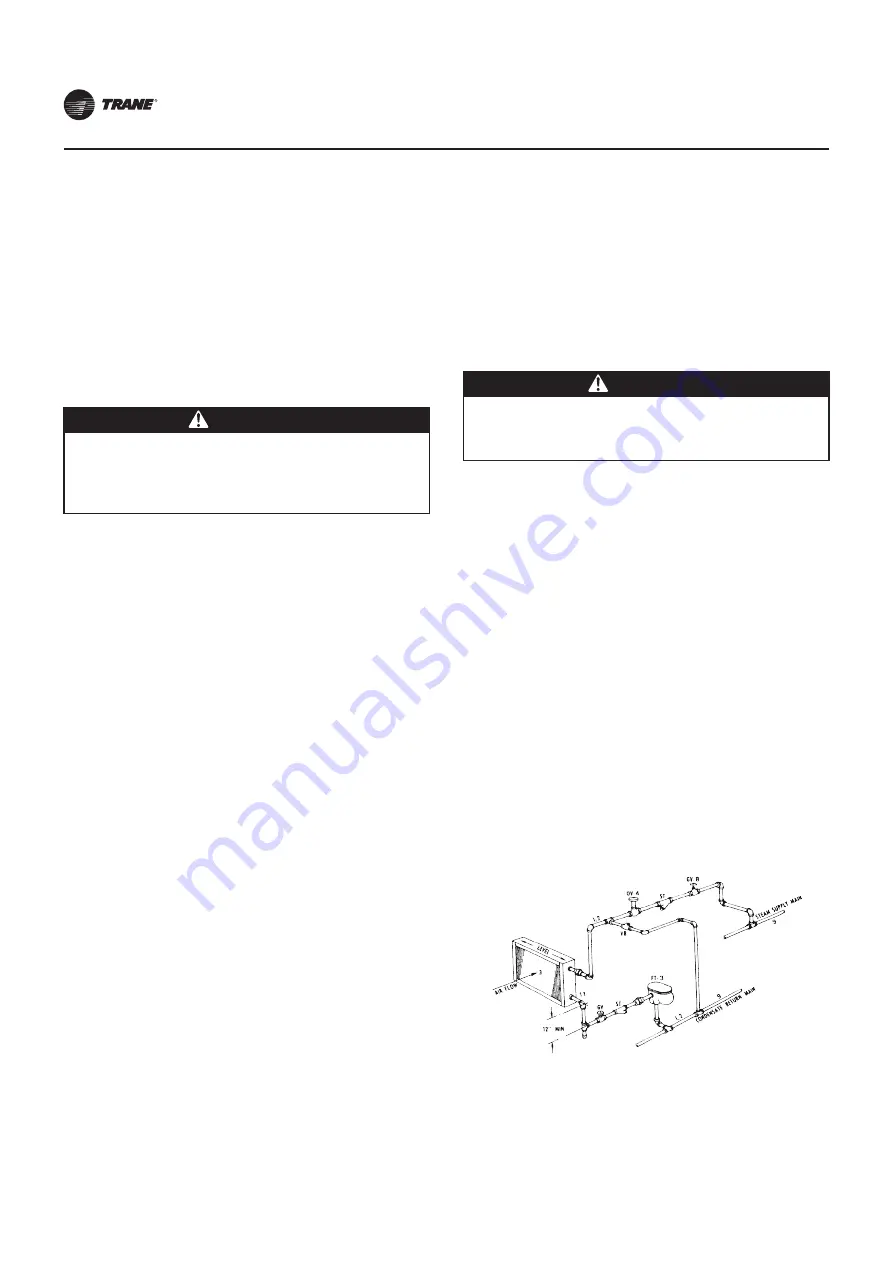
Piping and Connections
28
Use a V-port modulating valve to obtain gradual
modulating action.
Do not modulate systems with overhead or pressurized
returns unless the condensate is drained by gravity to a
receiver (vented to atmosphere) and returned to the main
by a condensate pump.
At start-up on units with fresh air dampers, slowly turn the
steam on full at least 10 minutes before opening the fresh
air.
Pitch all supply and return steam piping down minimum of
1-inch per 10 feet in the direction of flow.
Do not drain the steam mains or take-off through the coils.
Drain the mains ahead of the coils through a steam trap to
the return line.
Overhead return require 1 psig of pressure at the steam
trap discharge for each 2 – feet elevation to assure
continuous condensate removal.
5.
6.
7.
8.
9.
10.
Steam Coil Piping Type A, AA Steam
Coil
These are for central system, industrial and process
application with one row, opposite- end connection. Maximum
standard operating limit :
Copper tube : 100 psig and 400ºF
Type AA coils feeds alternate tubes. Refer to Figure 17 for
typical steam coil piping.
CAUTION
Condensate must flow freely from coil at all times to
prevent physical coil damage from water hammer,
unequal thermal stresses, freeze-up and/or corrosion.
CAUTION
Always open the steam supply control valve slowly to
prevent possible coil damage.
Install a ½ inch, 15 degree swing check vacuum breaker in
the unused condensate return tapping as close as
possible to the coil.
Vent the vacuum breaker line to the atmosphere or
connect it to the return main at the discharge side of the
steam trap.
Run the return pipe at the full size of the steam trap
connection except for the short nipple screwed directly
into the coil condensate connection. Do not bush or
reduce the coil return tapping size.
Proper steam trap selection and installation is necessary
for satisfactory coil performance and service life. For
installation, use the following steps:
•
•
•
1.
2.
Note: Vacuum breaker relief is mandatory when the coil is
controlled by a modulating steam supply or a two- position
(ON-OFF) automatic steam supply valve.
3.
4.
Select trap based on maximum possible condensate
rate.
Locate the steam trap discharge at least 12 inches
below the condensate return tapping, this provides
sufficient hydrostatic head pressure to overcome trap
losses and assure complete condensate removal.
Float and thermostatic traps are recommended
because of gravity drain and continuous discharge
operation.
•
•
•
Use float and thermostatic traps with atmospheric
pressure gravity condensate return, with automatic
control or where the possibility of low-pressure supply
steam exists.
Use bucket traps ONLY when the supply steams in
unmodulated and 25 psig or higher.
Always install strainers as close as possible to the inlet
side of the trap. Do not modulate Type A, AA coils. Use
two position (ON-OFF) steam supply controls.
Typical Piping for Steam Coil.
Figure 17
AV - Automatic or manual air vent
MV - Magnetic valve
GV - Gate valve
FT - Float and thermostatic steam trap
VB - Vacuum breaker
ST - Strainer
OV - Automatic two-position control valve
Содержание CLCP Euro 25
Страница 16: ...Assembly Installation CLCP EURO 50 Breakpoint Frame to Frame 16 CLCPEURO 50 Break Point Frame to Frame Joining...
Страница 17: ...17 Assembly Installation CLCP EURO 50 Breakpoint Panel to Frame CLCPEURO 50 Break Point Panel to Frame Joining...
Страница 18: ...Assembly Installation CLCP EURO CLCP EURO XP Paneling 18...
Страница 22: ...Assembly Installation CLCP EURO XP CKD At Jobsite 22...
Страница 23: ...23 Assembly Installation CLCP...
Страница 24: ...Assembly Installation CLCP 24...
Страница 40: ...Maintenance 40 Figure 20 Belt Tension Measurement...
Страница 42: ...Trouble Analysis 42...
Страница 43: ...43 Trouble Analysis Pulley and Belt...
Страница 44: ...Appendix A Fan and Arrangement 44 Fan Discharge Arrangement...
Страница 50: ...Appendix B Filter Layout and Quantity Filter Dimension Nominal and Arrangement HEPA AstroCel VXL Filter 50...
Страница 51: ...Typical Motor Wiring Diagram 51...
Страница 52: ...52 Service Light and Door Switch Wiring...
Страница 53: ...Factory Installed VFD TR200 Wiring Setting 53...
Страница 54: ...Factory Installed VFD TR200 Wiring Setting 54 TR200 BASIC SETTING_OPEN LOOP...
Страница 56: ...Pre Start Up Checklist 56...
Страница 57: ...Pre Start Up Checklist 57...