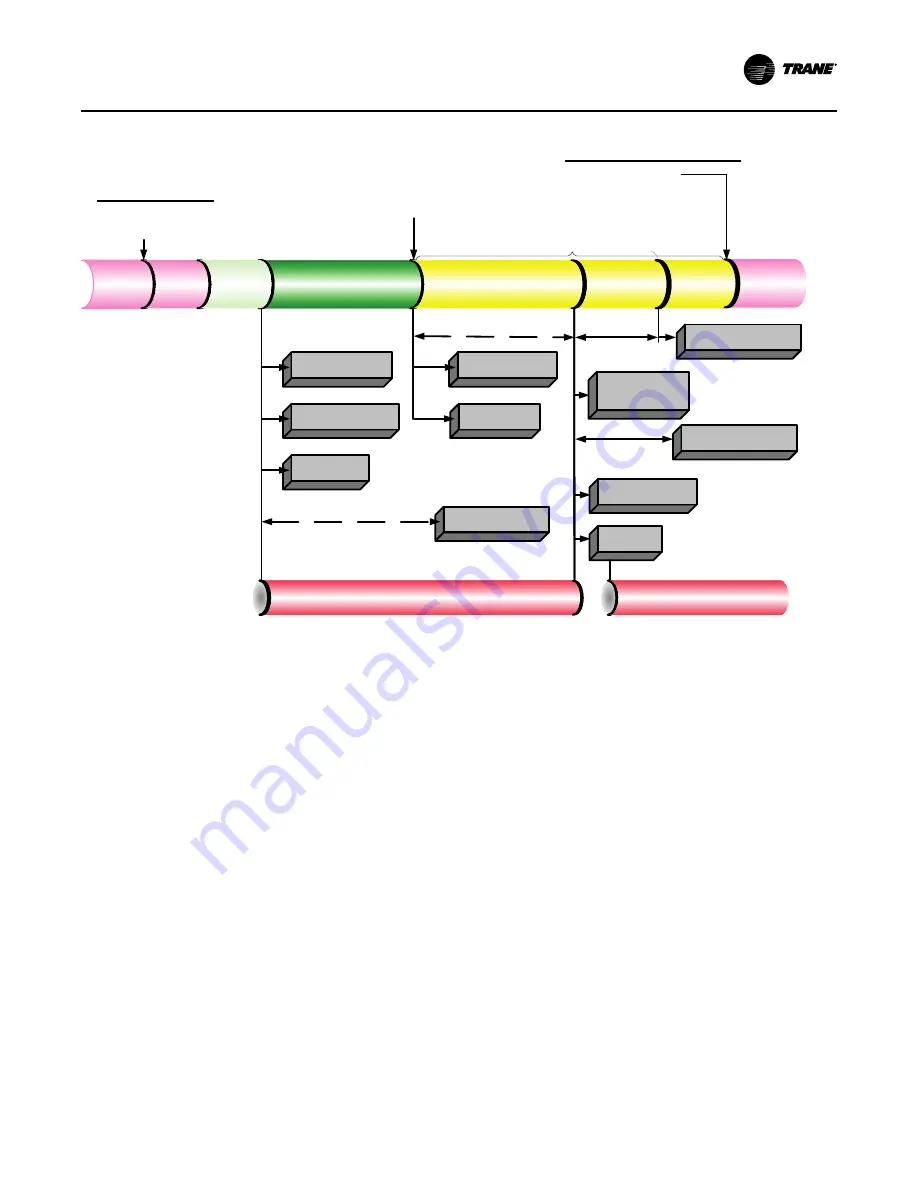
CVHE-SVX005B-EN
83
Figure 59.
Sequence of operation: ice building: auto to ice to ice building complete to auto
Evap Entering Water
Temp Falls Below the
Ice Termination
Setpoint
Running
(Ice Building)
Open IGV at MaxRate/Max
AFD Frequency
Close IGV /Min AFD
Frequency
Enforce All Limits and Running Mode Diagnostics
Command Ice Building via:
1. Front Panel OD (On)
2. Tracer (On)
3. External Input (Close/Short)
Energize
Ice Building Relay
Ignore Softloading and Set
DLS = 100%
De-Energize Ice
Building Relay
De-Energize Head Relief
Request Relay
Close IGV
(0-50 Seconds)
Shutting Down
(Ice Building
Complete)
Energize Head Relief
Request Relay
Head Relief Request Relay Delay
(1 to 60 Mins)
Preparing Shutdown
(Ice Building Complete)
De-Energize Oil Pump
De-Energize
Compressor
Post Lube
(3 Minutes)
Ignore Evap Pump Off
Delay Time For Ice
Building
De-Energize Evaporator
Water Pump Relay
De-Energize Condenser
Water Pump Relay
Confirm No Compressor Currents
Within 8 Seconds
Auto
(Waiting For A
Need To Cool)
Run Inhibit
(Ice Building
Complete)
Remove all Ice Building Commands via:
1. Front Panel OD (Auto)
2. Tracer (Auto)
3. External Input (Open)
Evap Entering Water Temp Rises
above the Ice Termination Setpoint
Auto
(Waiting For A
Need To Cool)
Auto
(Waiting To
Start)
Auto
(Starting
Compressor)
Free Cooling Cycle
Based on the principle that refrigerant migrates to the
coldest area in the system, the free cooling option
adapts the basic chiller to function as a simple heat
exchanger. However, it does not provide control of the
leaving chilled water temperature.
If condenser water is available at a temperature lower
than the required leaving chilled water temperature,
the operator interface must remain in AUTO and the
operator starts the free cooling cycle by enabling the
Free Cooling mode in the Tracer
®
AdaptiView
™
Feature Settings group of the operator interface, or by
means of a BAS request. The following components
must be factory- or field-installed to equip the unit for
free cooling operation:
•
a refrigerant gas line, and electrically-actuated
shutoff valve, between the evaporator and
condenser,
•
a valved liquid return line, and electrically-actuated
shutoff valve, between the condenser sump and the
evaporator,
•
a liquid refrigerant storage vessel (larger
economizer), and
•
additional refrigerant.
When the chiller is changed over to the free cooling
mode, the compressor will shut down if running and
the shutoff valves in the liquid and gas lines open; unit
control logic prevents the compressor from energizing
during free cooling. Liquid refrigerant then drains (by
gravity) from the storage tank into the evaporator and
floods the tube bundle. Since the temperature and
pressure of the refrigerant in the evaporator are higher
than in the condenser (i.e., because of the difference in
water temperature), the refrigerant in the evaporator
vaporizes and travels to the condenser, cooling tower
water causes the refrigerant to condense on the
condenser tubes, and flow (again, by gravity) back to
the evaporator.
This compulsory refrigerant cycle is sustained as long
as a temperature differential exists between condenser
and evaporator water. The actual cooling capacity
provided by the free cooling cycle is determined by the
difference between these temperatures which, in turn,
determines the rate of refrigerant flow between the
evaporator and condenser shells.
If the system load exceeds the available free cooling
capacity, the operator must manually initiate
changeover to the mechanical cooling mode by
disabling the free cooling mode of operation. The gas
and liquid line valves then close and compressor
operation begins (refer to the figure in
“,”
[power up to
starting], beginning at Auto mode). Refrigerant gas is
drawn out of the evaporator by the compressor, where
it is then compressed and discharged to the condenser.