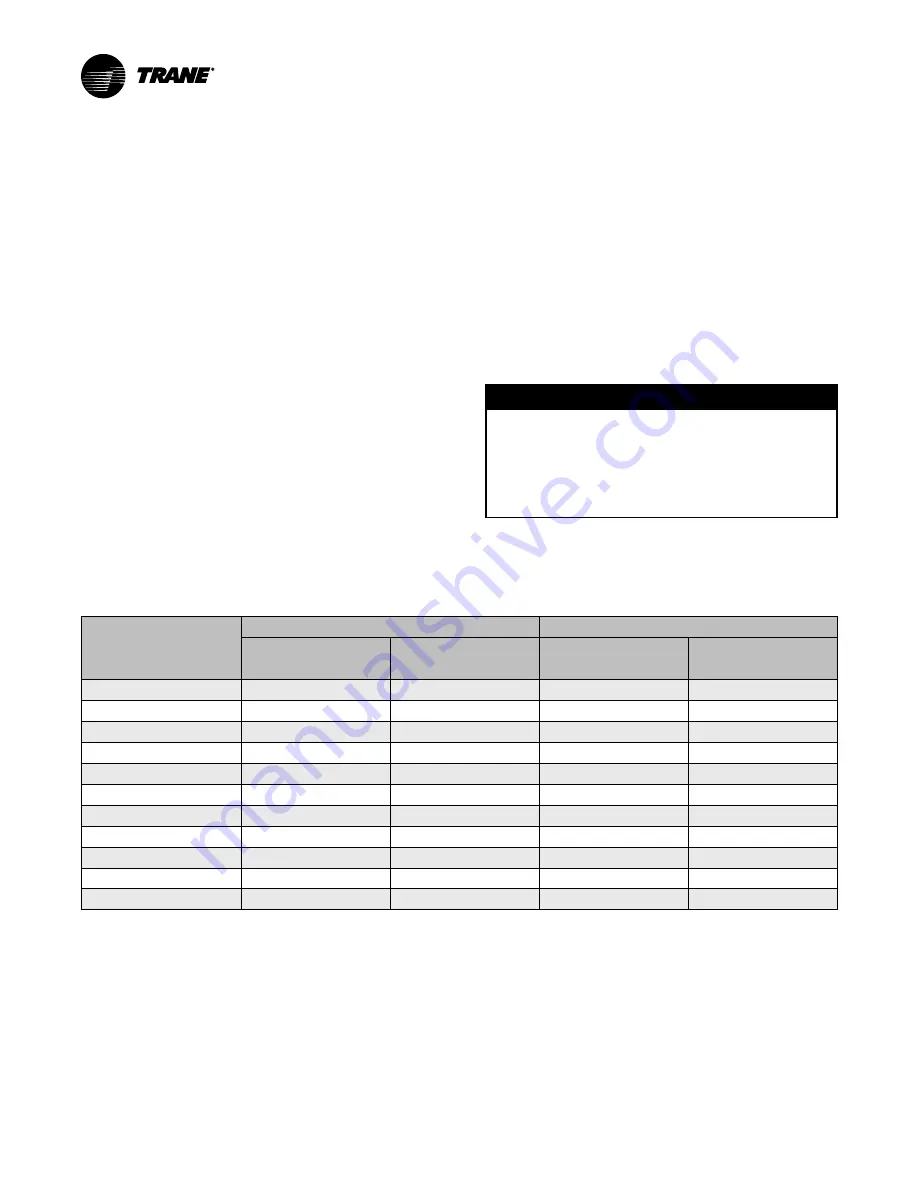
CVHE-SVX005B-EN
47
Insulation
Unit Insulation Requirements
Factory-installed insulation is available as an option for
all units. Factory installation does NOT include
insulation of the chiller feet; if required, insulation for
chiller feet is provided by others. In applications where
the chiller is not factory-insulated, install insulation
over the areas outlined and highlighted with dashed
lines as shown in the figure in
.
Insulate all 1/4-in. (6.35-mm) eductor lines, one from
the suction cover and one from the evaporator, to
prevent sweating.
The quantities of insulation required based on unit size
and insulation thickness are listed in the following
table. Insulation thickness is determined at normal
design conditions which are:
•
Standard comfort-cooling leaving chilled water
temperature
•
85°F (29.4°C) dry bulb ambient temperature
•
75 percent relative humidity
Operation outside of normal design conditions as
defined in this section may require additional
insulation; contact Trane for further review.
N
No
otte
e:: If the unit is not factory-insulated, install
insulation around the evaporator bulbwells and
ensure that the bulbwells and connections for
the waterbox drains and vents are still accessible
after insulation is applied. The sensor modules
(Low Level Intelligent Devices [LLIDs]) and
interconnecting four-wire cable inter-processor
communication (IPC) bus must be raised up
above the field-installed insulation. Secure the
IPC bus to the insulation top/outer surface after
insulation is completed.
IIm
mp
po
orrtta
an
ntt:: Do NOT insulate the motor housing, unit
wiring, or sensor modules.
N
NO
OT
TIIC
CE
E
E
Eq
qu
uiip
pm
me
en
ntt D
Da
am
ma
ag
ge
e!!
F
Fa
aiillu
urre
e tto
o rre
em
mo
ov
ve
e tth
he
e ssttrra
aiin
n rre
elliie
eff w
wiitth
h tth
he
e sse
en
nsso
orr
cco
ou
ulld
d rre
essu
ulltt iin
n e
eq
qu
uiip
pm
me
en
ntt d
da
am
ma
ag
ge
e..
D
Do
o N
NO
OT
T a
atttte
em
mp
ptt tto
o p
pu
ullll sse
en
nsso
orr b
bu
ullb
b tth
hrro
ou
ug
gh
h tth
he
e
ssttrra
aiin
n rre
elliie
eff;; a
allw
wa
ay
yss rre
em
mo
ov
ve
e tth
he
e e
en
nttiirre
e ssttrra
aiin
n rre
elliie
eff
w
wiitth
h tth
he
e sse
en
nsso
orr..
Table 13.
Evaporator insulation requirements
EVSZ
(a)
Standard Unit
Free Cooling
3/4 in. (19.05 mm)
Insulation(Square
Feet)
3/8 in. (9.525 mm)
Insulation
(b)
(Square
Feet)
3/4-in. (19.05 mm)
(Square Feet)
3/8 in. (9.525 mm)
(Square
Feet)
032 Short
337
52
347
74
032 Long
365
52
377
74
050 Short
385
63
398
72
050 Long
420
63
436
72
080 Short
505
84
515
97
080 Long
553
84
566
97
142 Medium
555
98
555
133
142 Long
578
98
578
133
142 Extended
603
104
629
133
210 Long
700
98
710
133
250 Extended
770
97
780
133
Note:
Chillers equipped with refrigerant pumps are NOT insulated on the motor or refrigerant drain lines.
(a)
3/4-in. (19.05-mm) sheet insulation is installed on the evaporator, evaporator waterboxes, suction elbow, and suction cover.
(b)
3/8-in. (9.525-mm) sheet insulation is installed on all economizers. All liquid lines and other pipes require the use of 1/2-in. (12.7-mm) pipe insulation or
3/8-in. (9.525-mm) sheet insulation. Copper oil eductor tube lines require pipe insulation.
Insulation Thickness
Requirements
Factory-applied Insulation
All low-temperature surfaces are covered with 3/4 in.
(19.05 mm) Armaflex
®
II or equal (thermal conductivity
= 0.28 Btu/h-ft
2
[1.59 W/m
2
-K]), including the
evaporator, waterboxes, and suction elbow. The
economizer and motor cooling lines are insulated with
3/8 in. (9.525 mm) and 1/2 in. (12.7 mm) insulation,
respectively.
The insulation is Armaflex
®
or equivalent closed cell
elastomeric insulation to prevent the formation of