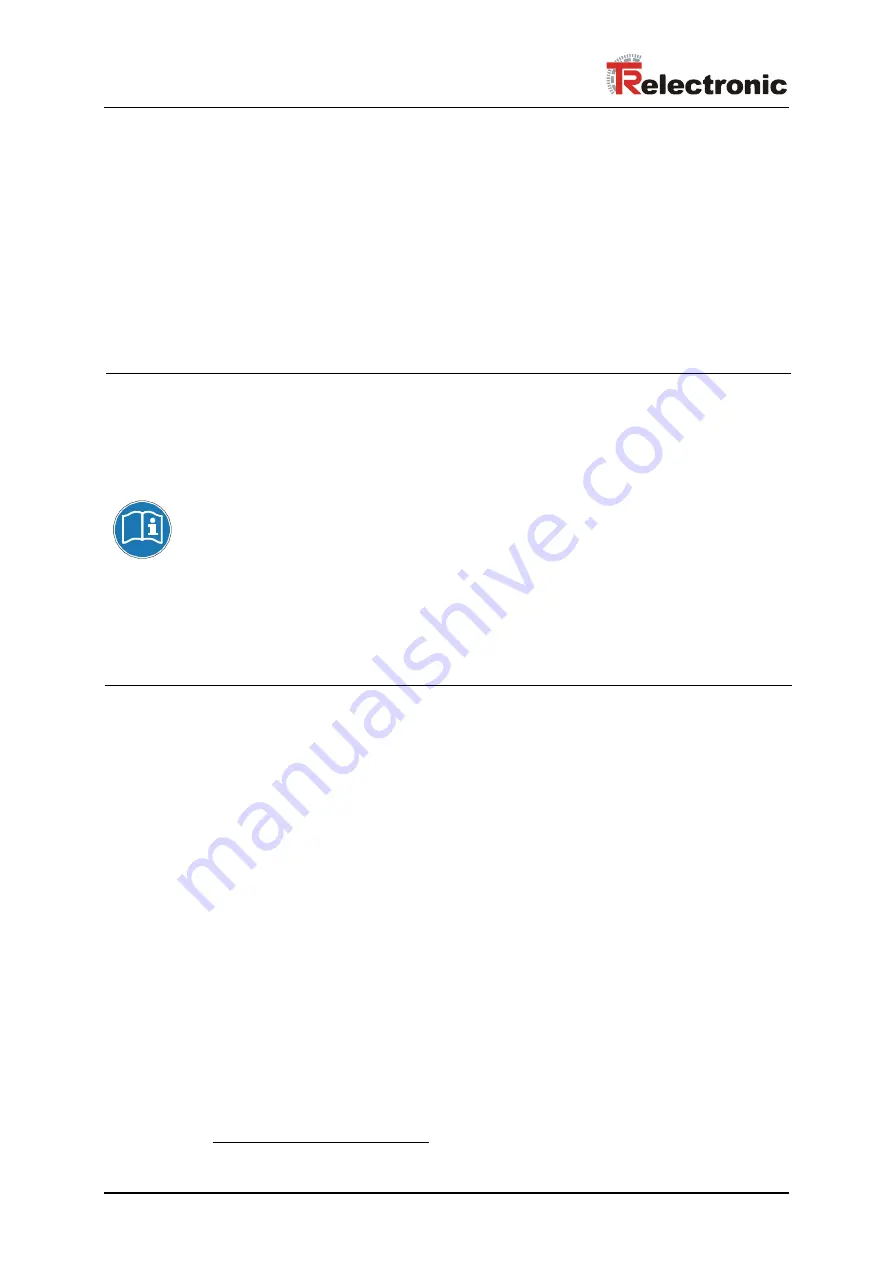
Device description / start-up
©
TR-Electronic GmbH 1997, All Rights Reserved
Printed in the Federal Republic of Germany
Page 28 of 45
TR - ECE - BA - GB - 0009 - 08
03/04/2010
3.8.3 Scaling function
3.8.3.1 Nominal configurations PNO Class 1+2
The encoder does not support a gear function. The position value is decoded in binary
form and balanced against a zero offset and the code sequence.
The position is calculated according to the following formula:
Measuring length in increments
*
Number of increments per revolution
= -------------------------------------------------
Number of revolutions
When entering the parameterization data, make sure the parameters 'Measuring
length in increments' and 'Number of increments per revolution' are chosen so
that the quotient of the two parameters is a second power.
If this is not the case, the encoder will correct the measuring length in
increments to the next smallest second power in revolutions. The number of
increments per revolution remains constant.
The re-calculated measuring length in increments can be read out via the
extended diagnostic information for Class 2 and is always smaller than the
predefined measuring length. Therefore it can be that the actually needed total
increment number is exceeded and the encoder generates a zero-point
changeover before reaching the maximum mechanical displacement distance.
Since the internal absolute position (before the encoder was scaled and a zero-
point adjustment was executed) recurs periodically after 4096 revolutions, at
rotating applications (endless driving to the same direction, the number of
revolutions is not a power of two)
it comes inevitably to offsets.
For such applications, one of the TR - nominal configurations has to be used.
*
Operator input