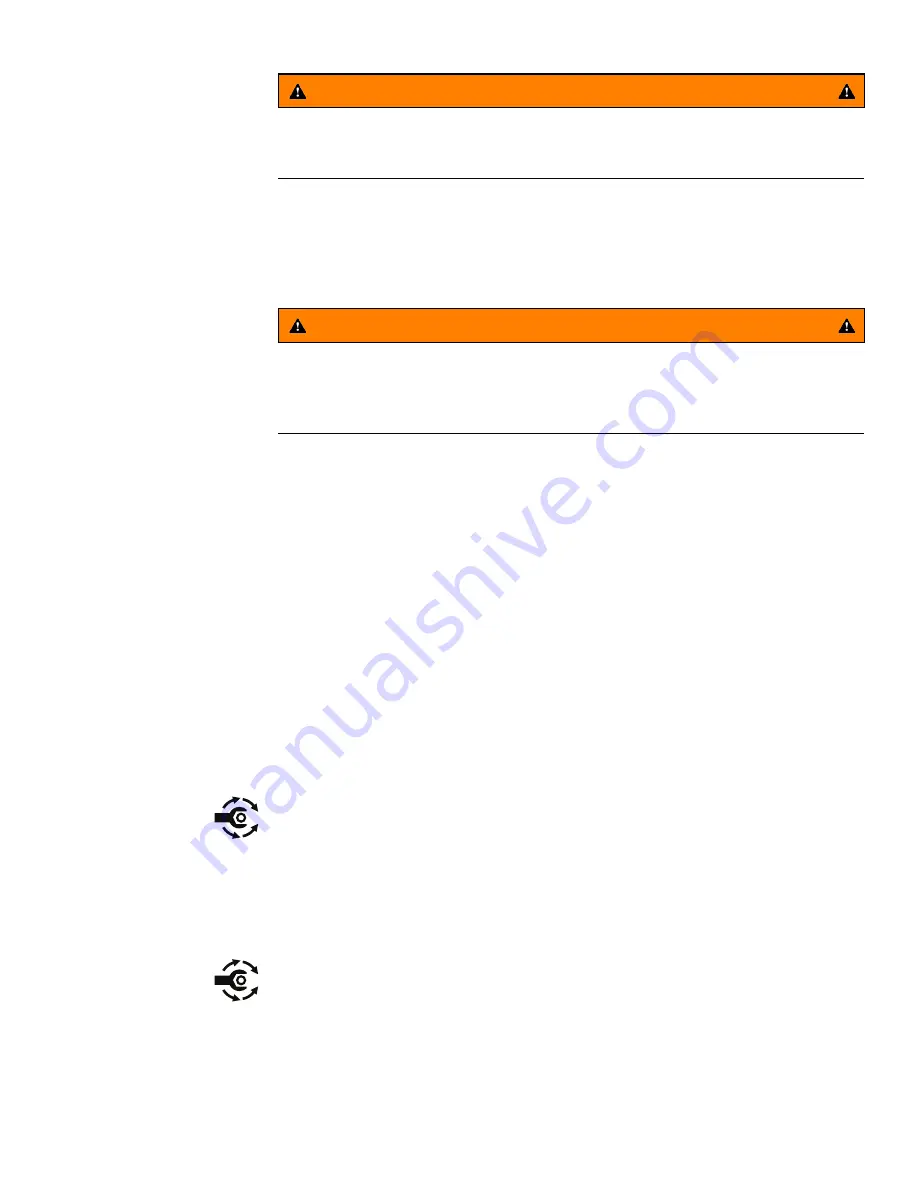
Removing the Steering Cylinder (continued)
WARNING
Before jacking up the machine, review and follow
Instructions (page 1–7)
.
2. Jack or lift rear wheel off the ground.
3. Remove the rear wheel from the machine.
4. Thoroughly clean hydraulic hose ends and fittings on steering cylinder to
prevent hydraulic system contamination.
WARNING
Before disconnecting or performing any work on the hydraulic
system, all pressure in the system must be relieved. See
Hydraulic System Pressure (page 5–3)
.
5. Label the hydraulic hoses to show their correct position on the steering
cylinder. Remove the hydraulic hoses from steering cylinder.
6. Remove the flextop lock nut from both steering cylinder ball joints.
7. Use a suitable tool (pickle fork) to separate the ball joints from the machine.
8. If hydraulic fittings are to be removed from steering cylinder, mark fitting
orientation to allow correct assembly. Discard the O−rings from removed
fittings.
9. If needed, remove the ball joints from steering cylinder.
Installing the Steering Cylinder
1. If removed, install ball joints into steering cylinder.
2. Lubricate and place new O−rings onto removed steering cylinder fittings.
Install fittings into cylinder openings using marks made during the removal
process to properly orientate fittings. Tighten fittings (see
Hydraulic Fittings (SAE Straight Thread O-Ring Fittings) (page 5–8)
).
3. Install the steering cylinder to machine. When securing cylinder ball joints
to machine, torque tighten the flextop lock nut from
115 to 156 N·m (85 to
115 ft−lb)
.
4. Remove caps and plugs from steering cylinder fittings and hoses. Using
labels placed during cylinder removal, properly connect hydraulic lines to
steering cylinder (see
Installing Hydraulic Hoses and Tubes (O-Ring Face
Seal Fittings) (page 5–6)
).
5. Secure the rear wheel to the machine with four (4) lug nuts. Lower machine
to the ground. Torque wheel lug nuts in a crossing pattern from
61 to 88
N·m (45 to 65 ft−lb)
.
6. Make sure that the hydraulic tank is full. Add correct fluid if necessary.
7. After assembly is completed, operate steering cylinder to verify that hydraulic
hoses and fittings are not contacted by anything.
Reelmaster
®
3100-D/3105-D
Page 5–137
Hydraulic System: Service and Repairs
20252SL Rev A
Содержание 03200 Reelmaster 3100-D
Страница 4: ...NOTES NOTES Page 4 Reelmaster 3100 D 3105 D 20252SL Rev A ...
Страница 6: ...g341979 Figure 1 Preface Page 6 Reelmaster 3100 D 3105 D 20252SL Rev A ...
Страница 10: ...Preface Page 10 Reelmaster 3100 D 3105 D 20252SL Rev A ...
Страница 20: ...Safety Safety and Instructional Decals Page 1 10 Reelmaster 3100 D 3105 D 20252SL Rev A ...
Страница 44: ...Specifications and Maintenance Special Tools Page 2 24 Reelmaster 3100 D 3105 D 20252SL Rev A ...
Страница 88: ...g344528 Figure 28 Hydraulic System Hydraulic Schematic Page 5 12 Reelmaster 3100 D 3105 D 20252SL Rev A ...
Страница 89: ...g344526 Figure 29 Reelmaster 3100 D 3105 D Page 5 13 Hydraulic System Hydraulic Schematic 20252SL Rev A ...
Страница 198: ...g345756 Figure 95 Hydraulic System Service and Repairs Page 5 122 Reelmaster 3100 D 3105 D 20252SL Rev A ...
Страница 204: ...g345782 Figure 99 Hydraulic System Service and Repairs Page 5 128 Reelmaster 3100 D 3105 D 20252SL Rev A ...
Страница 224: ...Hydraulic System Service and Repairs Page 5 148 Reelmaster 3100 D 3105 D 20252SL Rev A ...
Страница 308: ...Wheels Brakes and Chassis Service and Repairs Page 7 30 Reelmaster 3100 D 3105 D 20252SL Rev A ...
Страница 376: ...Universal Groomer Optional Service and Repairs Page 9 22 Reelmaster 3100 D 3105 D 20252SL Rev A ...
Страница 382: ...Page A 6 20252SL Rev A Reelmaster 3100 D 3105 D Drawing 122 1522 Rev A Sheet 1 of 1 Electrical Schematic g346835 ...
Страница 383: ...Reelmaster 3100 D 3105 D Drawing 122 1523 Rev B Sheet 1 of 2 20252SL Rev A Page A 7 Wire Harness Drawing CV g346834 ...
Страница 384: ...Page A 8 20252SL Rev A Reelmaster 3100 D 3105 D Drawing 122 1523 Rev A Sheet 2 of 2 Wire Harness Drawing g346833 ...
Страница 385: ......