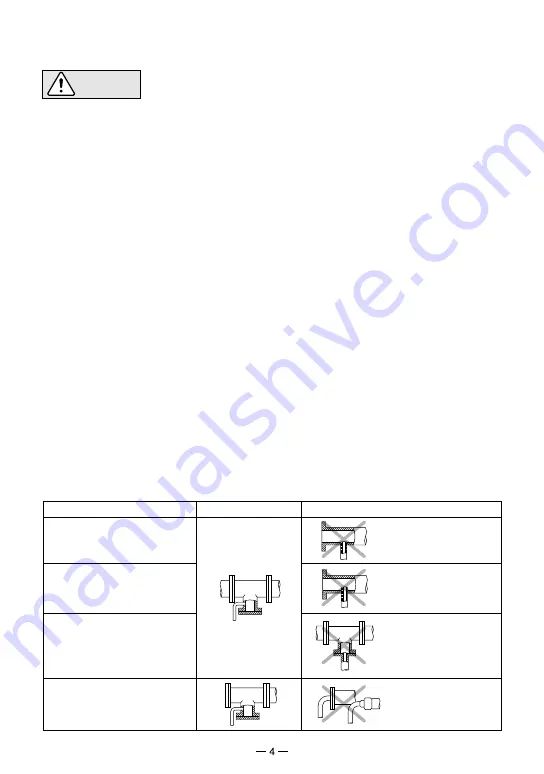
NOTE: For socket weld connections, use electric welding with a single pass. As internal parts are
not damaged by a single welding pass, there is no need to remove them before welding.
1. The trap can be installed either horizontally or vertically, but make sure the arrow on the trap
points in the direction of flow.
2. Before installation, be sure to remove all protective seals.
3. Before installing the trap, blow out the inlet piping to remove all dirt and oil.
4. Install the trap in the lowest part of the pipeline or equipment so the condensate flows naturally
into the trap by gravity. The inlet pipe should be as short and have as few bends as possible.
5. Support the pipes properly within 800 mm (2.5 ft) on either side of the trap.
6. Install a bypass valve to discharge condensate, and inlet and outlet valves to isolate the trap in
the event of trap failure or maintenance.
7. Install a check valve at the trap outlet whenever more than one trap is connected to the
condensate collection pipeline.
8. In order to avoid excessive back pressure, make sure the discharge pipes are large enough;
(the outlet back pressure allowance should be no more than 50% of the inlet steam pressure).
9. We recommend unions to facilitate connection and disconnection of screwed models.
4. Proper Installation
• Installation, inspection, maintenance, repairs, disassembly, adjustment
and valve opening/closing should be carried out only by trained
maintenance personnel.
• Take measures to prevent people from coming into direct contact with
product outlets.
• Install for use under conditions in which no freeze-up will occur.
• Install for use under conditions in which no water hammer will occur.
CAUTION
Check to make sure that the pipes connected to the trap have been installed properly.
1. Is the pipe diameter suitable?
2. Has sufficient space been secured for maintenance?
3. Have maintenance valves been installed at inlet and outlet? If the outlet is subject to back
pressure, has a check valve been installed?
4. Is the inlet pipe as short as possible, with as few bends as possible, and installed so that the
condensate will flow naturally down into the trap?
5. Has the piping work been done properly as shown in the table below?
5. Piping Arrangement
Requirement
Diameter is too
small.
Diameter is too
small and inlet
protrudes into pipe.
Rust and scale
flow into the trap
with the
condensate.
Condensate
collects in the
pipe.
Correct
Incorrect
Install a catchpot with the
proper diameter.
Make sure the flow of
condensate is not
obstructed.
To prevent rust and scale
from flowing into the trap,
connect the inlet pipe 25 -
50 mm (1 - 2 in) above
the base of the T - pipe.
When installing on the
blind end, make sure
nothing obstructs the flow
of condensate.
Содержание PowerDyne HR150A
Страница 11: ...10 ...