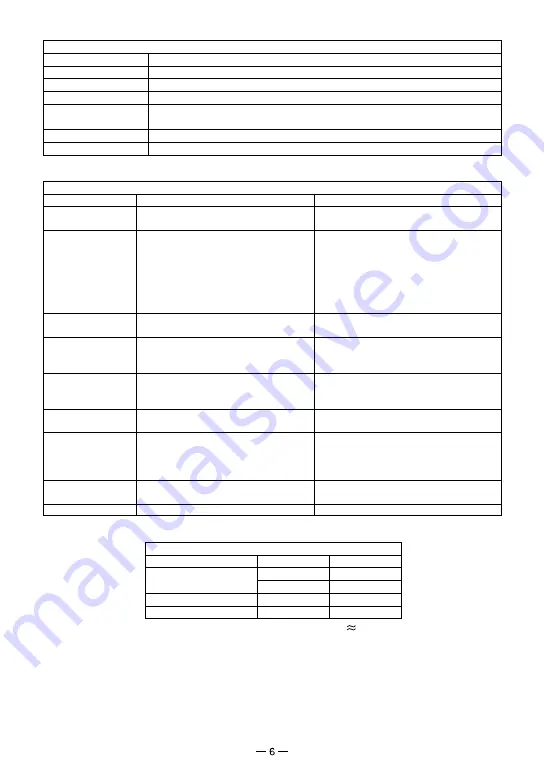
Sealing surfaces
Screen
Bimetal ring (HR80A)
Disc holder (HR80A)
Disc
Module valve seat
Body, Cover
Check for damage or dirt on the sealing surfaces
Check for clogging or corrosion damage
Check for rust, scale, oil film, warping or damage
Check for rust, scale, oil film, warping or damage
Check for wear and damage, scratches, on the surface where it contacts
the valve seat, and dirt or oil film
Check discharge channel and grooves for rust and scale inside
Check inside for erosion, dirt, grease, rust or scale
Disassembly/Reassembly
(to reassemble, follow procedures in reverse)
Part & No.
During reassembly
During disassembly
Cap 12
Eye Nut 18
Cover bolt 10 or
Cover nut 16
Cover 2
Module gasket 7
(large)
Disc 4
Disc holder ring 6
(HR80A)
Air vent ring 5
(HR80A)
Module valve
seat 3
and Guide pin 14
Module gasket 8
(small)
Screen 9
Remove the set screw (HR80A) or
the eye nut and then the cap.
Use a socket wrench to remove
bolts or nuts at diagonal position
sequentially. Apply liquid penetrant
for at least 5 minutes to loosen the
bolts or nuts, if necessary. Lift up
and remove cover.
Remove the gasket and clean the
sealing surfaces.
Remove, being careful not to
scratch the lapped surface.
Remove without bending.
Remove without bending, as it will
not return to its proper shape.
Remove from the body.
Remove the gasket and clean the
sealing surfaces.
Be careful not to bend the screen.
Adjust length of spacer, if necessary.
(HR150A, HR260A)
Tighten bolts or nuts at diagonal
position sequentially after having
applied antiseize to the threads and
threaded bolt holes. It is
recommended to use new bolts and
nuts for the assembly. Tighten to the
proper torque.
Replace with a new gasket even if no
damage can be seen.
Make sure that the seat surface (the
lapped side with groove) is facing
down, toward the valve seat.
Set on the air vent ring and make sure
that it does not sit on the valve seat
surface.
Reinsert without bending.
Insert the guide pin into the hole in the
body and make sure it fits properly
into the respective hole of the module
valve seat.
Replace with a new gasket even if no
damage can be seen.
Be careful not to bend the screen.
Parts Inspection Procedure
* Different cover bolts are used depending on the product. Confirm distance
across flats and use it to select the appropriate torque.
If drawings or other special documentation were supplied for the product,
any torque given there takes precedence over values shown here.
Cover bolt HR80A*
Cover nut HR150A
Cover nut HR260A
35
50
130
280
(26)
(37)
(95)
(205)
Tightening Torque and Distance Across Flats
Part
N
•
m
13
14
22
27
mm
(Ib
•
ft)
1 N·m 10 kg·cm
( )
( )
( )
( )
(in)
2
1
16
9
8
7
1
16
1
/
/
/
/
Содержание PowerDyne HR150A
Страница 11: ...10 ...