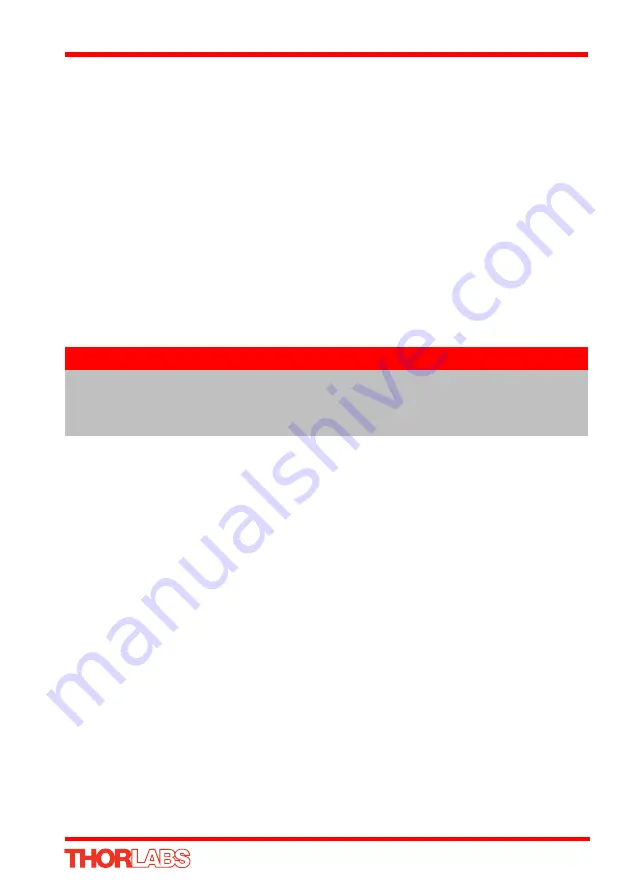
BBD30x Series Brushless DC Servo Controllers
Page 55
Current Loop (Settled) Control Settings
The following parameters are designed to assist in maintaining stable operation and
reducing noise at the demanded position. They allow the system to be tuned such that
errors caused by external vibration and manual handling (e.g. loading of samples) are
minimized, and are applicable only when the stage is settled, i.e. the Axis Settled
status bit (bit 14) is set - see Section 6.3.4.
Proportional
– This term drives the motor current to the demand value, reducing the
current error. It accepts values in the range 0 to 32767.
Integral
– This term provides the ‘restoring force’ that grows with time, ensuring that
the current error is zero under a constant torque loading. It accepts values in the
range 0 to 32767.
Integral Limit
– This term is used to cap the value of the lntegrator to prevent an
excessive build up over time of the ‘restoring force’, thereby causing runaway of the
integral sum at the output. It accepts values in the range 0 to 32767. If set to 0 then
the integration term in the PI loop is ignored.
Integral Dead Band
– This parameter allows an integral dead band to be set, such
that when the error is within this dead band, the integral action stops, and the move
is completed using the proportional term only. It accepts values in the range 0 to 32767.
Feed Forward
– This parameter is a feed-forward term that is added to the output of
the PI filter. It accepts values in the range 0 to 32767.
Persist Settings to Hardware -
Many of the parameters that can be set for the BBD30x
series drivers can be stored (persisted) within the unit itself, such that when the unit
is next powered up these settings are applied automatically. This is particularly
important when the driver is being used manually via a joystick, in the absence of a
PC and USB link. The
Position and Current Loop
parameters described previously
are good examples of settings that can be altered and then persisted in the driver for
later use.
To save the settings to hardware, check the ‘Persist Settings to Hardware’ checkbox
before clicking the ‘OK button.
The following two parameters assist in fine tuning the motor drive current
and help reduce audible noise and/or oscillation when the stage is near
the target position. A certain amount of trial and error may be
experienced in order to obtain the optimum settings.
Note
Содержание BBD301
Страница 1: ...Original Instructions BBD301 BBD302 BBD303 Brushless DC Motor Controllers APT User Guide ...
Страница 20: ......
Страница 30: ......
Страница 72: ......
Страница 82: ...Page 79 Appendix F Regulatory F 1 Declarations Of Conformity F 1 1 For Customers in Europe CE certificate ...
Страница 85: ...HA0409T Rev BAug2021 www thorlabs com ...