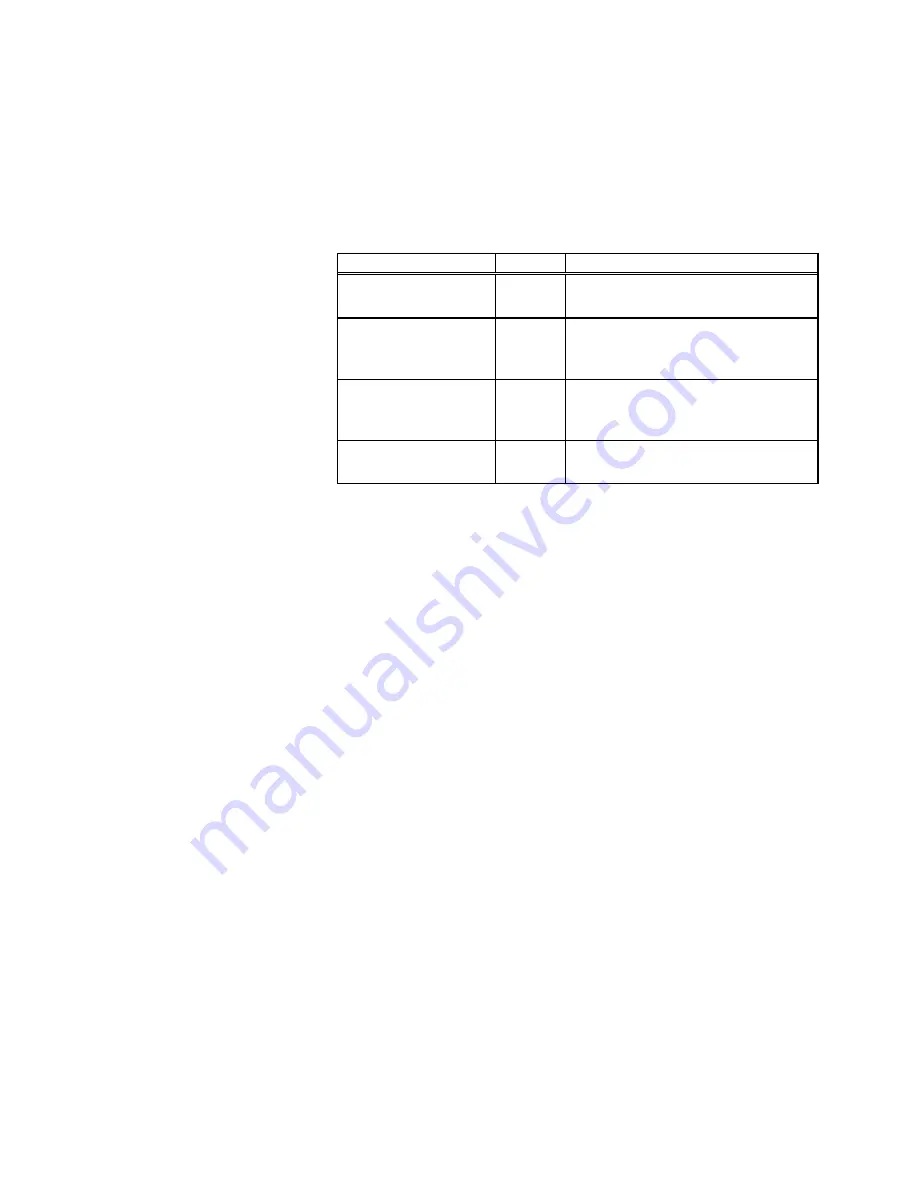
Thermo Fisher Scientific
A-
3
REC 4105 Rev L
When the TMD is unable to respond normally to a Modbus query, it will
return an appropriate exception response to the host.
Table A-1 shows the two-digit code and the meaning of each exception
response.
EXCEPTION
CODE
MEANING
Illegal Function
01
The function code received in the
query is not supported.
Illegal Data Address
02
The data address in the query is
not an allowable value for the
slave.
Illegal Data Value
03
The value in the query data field is
not an allowable value for the
slave.
Slave Device Busy
04
The slave is processing a long-
duration program command.
Table A–1.
TMD Exception Responses
The Modicon Modbus protocol establishes a minimum timing interval
between query and response messages that use RTU framing. This
delay allows devices attached to the serial bus to identify message
boundaries by means of the idle time between messages. The minimum
idle time between messages is 3.5 character times at the current serial
baud rate. However, there must be no more that 1.5 character times
between characters within a message, or the message will be considered
invalid.
In a multidrop system, all slave devices must process all query
messages, except for broadcast messages. Slave devices not addressed
by the query must also process and discard the response message sent by
the slave device that was addressed.
The slave device ID (slave address) for each individual TMD is assigned
in setup and can be from 1 to 247. On a multidrop line, each address
must be unique.
The TMD uses Modbus holding registers (4xxxx designation) to
implement the register set. The message function code implicitly
defines that the query applies to a holding register. The leading 4
(indicating a holding register) is not sent as part of the register address.
Registers are addressed starting at zero: register 1 is addressed as 0.
Exception
Responses
Master/Slave
Timing
Considerations
TMD Holding
Registers
Содержание Oretronic III
Страница 1: ...Oretronic III Tramp Metal Dector Operating Service Manual REC 4105 Rev L Part Number 060298 English...
Страница 4: ......
Страница 8: ......
Страница 14: ......
Страница 68: ......
Страница 100: ......
Страница 114: ......
Страница 131: ......
Страница 132: ......
Страница 133: ......
Страница 134: ......
Страница 135: ......
Страница 136: ......
Страница 137: ......
Страница 138: ......
Страница 139: ......
Страница 140: ......
Страница 141: ......
Страница 142: ......
Страница 143: ......
Страница 144: ......
Страница 145: ......
Страница 146: ......
Страница 147: ......
Страница 148: ......
Страница 149: ......
Страница 150: ......
Страница 151: ......
Страница 152: ......