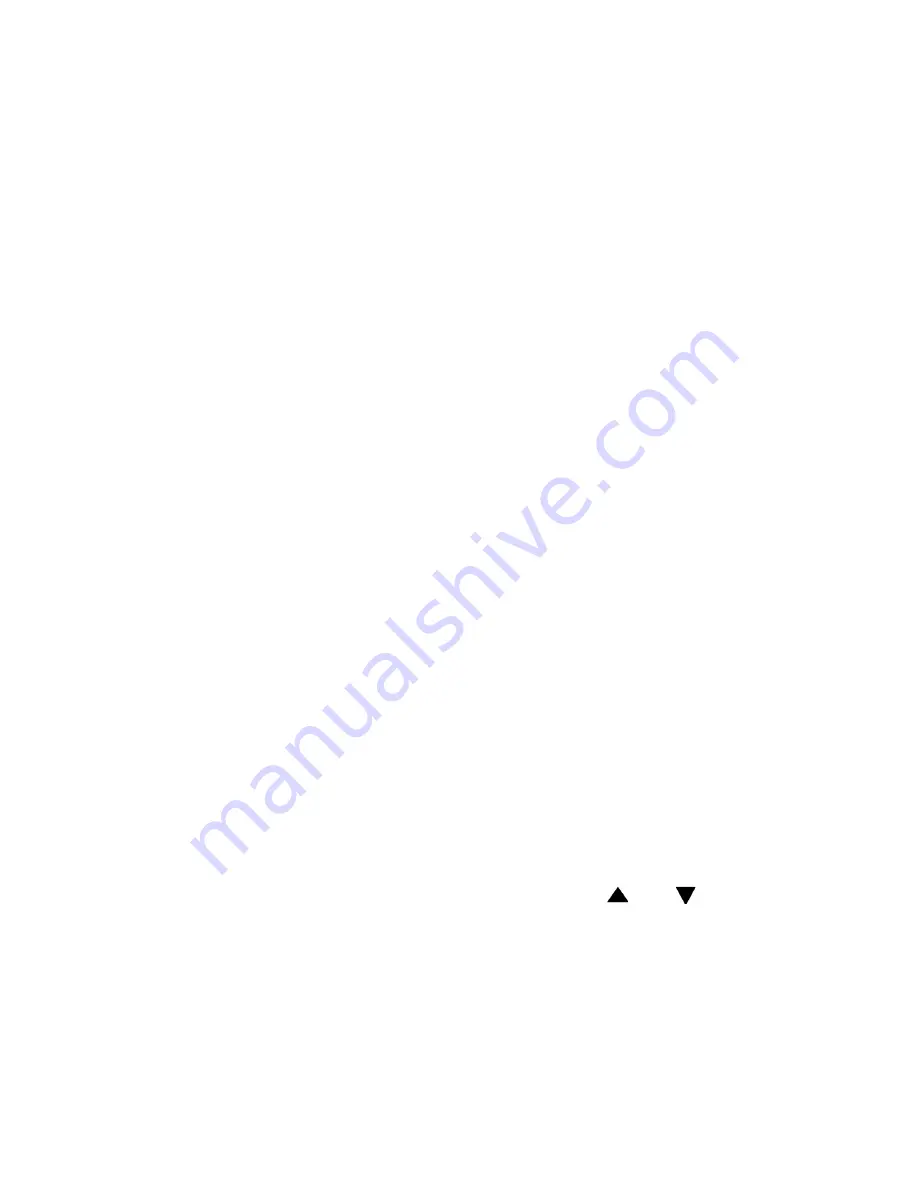
Thermo Fisher Scientific CryoExtra CE8100 Series
Preventative Maintenance | 61
Preventative Maintenance
Procedures
Level Verification
The differential pressure measurement system used on
CryoExtra freezers is nearly maintenance free. It provides a
high level of accuracy and resolution to give the operator a
precise indication of the exact amount of LN
2
present in the
freezer at all times. Despite its reliability, it is important that the
accuracy of the level measurement system is verified on a
weekly basis. This will prevent a control system malfunction
from adversely affecting the temperature in the freezer
storage space. Use the meter dipstick provided with every
CryoExtra
freezer to manually measure the amount of LN
2
in
the freezer. Follow the “Dip Stick Procedure” listed in section
“Liquid Nitrogen Level Calibration”
to properly measure
the level. If the level is off by 1.0 inch (25 mm) or more, follow
the calibration procedure listed in the aforementioned section.
Verify Adequate Supply
Adequate LN
2
supply pressure and flow is imperative to the
proper operation of CryoExtra freezers. Any LN
2
supply
whether from bulk tank or liquid cylinder must be able to
maintain a pressure of 22-35 psi (1.52 – 2.41 bar) during a
filling cycle and must have enough liquid to ensure the
completion of a fill cycle. The majority of nuisance alarms
reported from CryoExtra freezers are due to inadequate
supply.
1. Observe the pressure of the supply source. Ideally,
pressure should be 22 – 35 psi (1.52 – 2.41 bars).
Note:
It is very common for the pressure gauge on an
industrial liquid cylinder to be inoperative. If you suspect this
to be the case, install a pressure gauge inline between the
liquid cylinder and the freezer for verification.
2. Verify the amount of liquid in the supply source. Most bulk
tanks have some method of digital or analog volume
measurement. Liquid cylinders typically use a sight
gauge. As with the pressure gauge on liquid cylinders, it
is common for the sight gauge to be inoperative.
3. The minimum amount of liquid necessary in the supply
should be enough to completely fill the number of
freezers it is supplying. This amount can be determined
from the LN
2
inch to volume table in the Appendix.
4. Initiate a fill start on at least one freezer on the network.
The supply system should be able to maintain
appropriate pressure throughout the duration of the fill
cycle.
5. If the supply is determined to be inadequate, have your
gas supplier replenish / replace the supply.
Plumbing Leak Check
Leaky plumbing connections can create a host of problems
including but not limited to:
•
Slow fill times
•
Nuisance Alarms
•
High LN
2
Consumption
•
Inaccurate level readings
•
Inaccurate liquid usage readings
Leaky plumbing connections are especially common on liquid
cylinder supply systems, since the fittings are regularly
loosened and tightened during liquid cylinder swap out.
1. With the supply system at operating pressure, thoroughly
spray all transfer hose connections and freezer plumbing
connections with leak detect solution.
2. Allow leak detect solution to penetrate fittings for at least
30 seconds.
3. Large leaks will be immediately apparent with large
bubble formations.
4. Small leaks will take longer to detect, with small bubble
formation in the appearance of “foam”.
5. Most leaks can be repaired by tightening the suspect
fitting with a crescent or appropriate sized wrench.
6. If tightening the fitting does not fix the leak, check the
fitting for cracks and or galling. If the fitting is damaged,
replace.
7. Recheck any replaced fittings for leaks.
High Temp Alarm Test
Please refer to
“High Temperature Alarm Test”
for details and
instructions on the High Temp Alarm Test.
Level Alarm Test
The Controller can trigger a high level or low level alarm if the
LN
2
level in the freezer exceeds the user defined parameters.
High Level Alarm Test
1. Observe and record the current LN
2
level.
2. Record the current level settings. They may be accessed
by pressing the “
” and “
” simultaneously to
access the quick reference menu or through the “Liquid
Level Menus”. The current LN
2
level should be between
the High Level Alarm setting and Low Level Alarm setting.
If not, allow the freezer to fill until it reaches the High Level
Fill setting.
3. Adjust the level offset so that the current level is a value
that is greater than the High Level Alarm setting. For
example, if the High Level Alarm setting is currently
10.0 inches, increase the offset value by at least 1.0 inch.
This will “fool” the Controller into thinking that the level