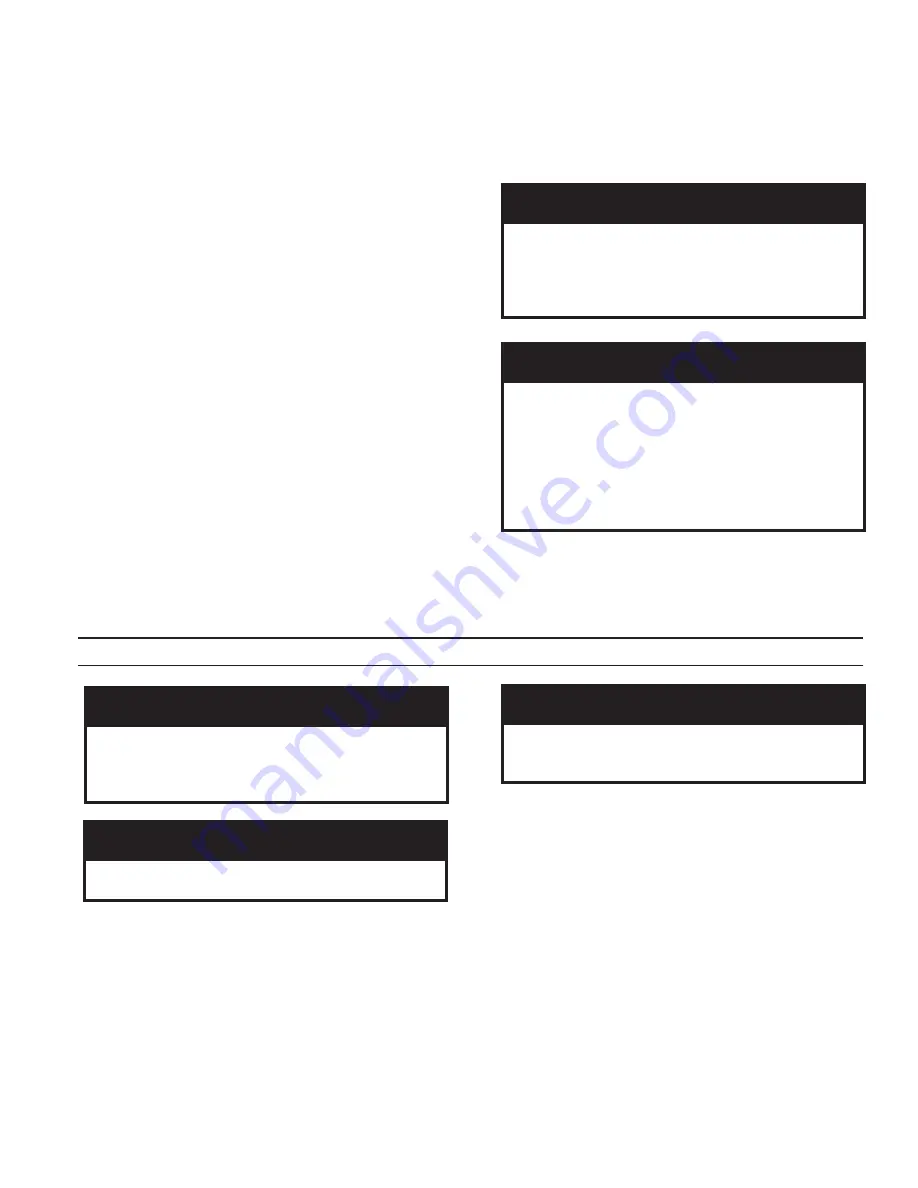
9
E.
Remove unit from shipping skid (if provided).
1
.
Tilt the boiler to one side and slide a small roller
under the raised base.
2. Tilt the boiler to the other side and slide another
roller under the base.
3. Place a larger pipe roller on floor behind the skid.
4. Roll the boiler forward or backward off the skid and
onto the pipe roller.
F.
Move boiler to its permanent location.
A
.
Move boiler to approximate installed position.
B.
Remove all crate fasteners.
C.
Open outside container and remove all inside protective
spacers and bracing.
D.
Remove all boiler hold-down fasteners.
a. Direct communication with outdoors. Minimum
free area of 1 square inch per 4,000 Btu per hour
input of all equipment in space.
b. Vertical ducts. Minimum free area of 1 square
inch per 4,000 Btu per hour input of all
equipment in space. Duct cross-sectional area
shall be same as opening free area.
c. Horizontal ducts. Minimum free area of 1
square inch per 2,000 Btu per hour input of all
equipment in space. Duct cross-sectional area
shall be same as opening free area.
Alternate method for boiler located within confined
space. Use indoor air if two permanent openings
communicate directly with additional space(s) of
sufficient volume such that combined volume of all
spaces meet criteria for unconfined space. Size each
opening for minimum free area of 1 square inch per
1,000 Btu per hour input of all equipment in spaces,
but not less than 100 square inches.
7. Ventilation Duct Louvers and Grilles. Equip outside
openings with louvers to prevent entrance of rain
and snow, and screens to prevent entrance of insects
and rodents. Louvers and grilles must be fixed in
open position or interlocked with equipment to open
automatically before burner operation. Screens must
not be smaller than ¼ inch mesh.
Consider the blocking effect of louvers, grilles and
screens when calculating the opening size to provide
the required free area. If free area of louver or grille
is not known, assume wood louvers have 20-25
percent free area and metal louvers and grilles have
60-75 percent free area.
DANGER
Do not install boiler where gasoline or other
flammable vapors or liquids, or sources of
hydrocarbons (i.e. bleaches, cleaners, chemicals,
sprays, paint removers, fabric softeners, etc.) are
used or stored.
NOTICE
Due to the low water content of the boiler, incorrect
sizing of the boiler with regard to the heating
system load will result in excessive boiler cycling
and accelerated component failure. Thermal
Solutions DOES NOT warrant failures caused
by incorrectly sized boiler applications. DO NOT
oversize the boiler to the system. Modular boilers
greatly reduce the likelihood of boiler oversizing.
NOTICE
Boiler crate is equipped with a tip and tell label. If
label indicates boiler has been tipped over during
shipping, remove crate and inspect before trucker
leaves.
CAUTION
Do not drop boiler. Do not bump boiler jacket
against floor.
WARNING
Installation of this boiler should be undertaken
only by trained and skilled personnel from a
qualified service agency.
II. Unpack the Boiler
Содержание EVO-1000
Страница 12: ...12 Figure 3 Sidewall Positive Pressure Venting Optional Figure 2 Sidewall Positive Pressure Venting...
Страница 13: ...13 Figure 4 Vertical Pressurized Venting...
Страница 15: ...15 Figure 5 Typical Negative Pressure Conventional Venting...
Страница 17: ...17 Figure 7 Vertical Air Intake Piping...
Страница 26: ...26 Figure 9a Standard UL FM CSD 1 Wiring Diagram on off EVO 500 2000...
Страница 27: ...27 Figure 9b Standard UL FM CSD 1 Wiring Diagram Modulation EVO 500 2000...
Страница 30: ...30 Figure 11 Modular System Horizontal Air Intake Piping...
Страница 31: ...31 Figure 12 Modular System Vertical Air Intake Piping...
Страница 32: ...32 Figure 13 Modular System Typical One Pipe Water Piping...
Страница 33: ...33 Figure 14 Modular System Typical Primary Secondary Water Piping...
Страница 34: ...34 Figure 15 Modular System Typical Primary Secondary without System Pump...
Страница 35: ...35 Figure 16 Modular System Typical Reverse Return Water Piping...
Страница 36: ...36 Figure 17 Modular System Reverse Return with System Pump Only...
Страница 37: ...37 Figure 18 Modular System Typical Primary Secondary with Reverse Return...
Страница 47: ...47 This Page Intentionally Left Blank...
Страница 48: ...48 Troubleshooting Guide B Troubleshooting Guide...
Страница 49: ...49 Troubleshooting Guide...
Страница 53: ...53 This Page Intentionally Left Blank...
Страница 54: ...54 Figure 19 Combustion Chamber Assembly...
Страница 56: ...56 Figure 20 Burner Assembly FRONT VIEW TOP VIEW...
Страница 58: ...58 Figure 21 UL FM CSD 1 Main Gas Train Assembly...
Страница 60: ...60 Figure 22a DB B DB B w POC Gas Train 500 750 Figure 22b DB B DB B w POC Gas Train 1000 2000...
Страница 62: ...62 Figure 23 Jacket Panels 4D 4J 4C 4B 4F 4I 4G 4E 4R 4K 4H 4J 4N 4M 4L 4Q 4A 4P 4P...
Страница 64: ...64 Figure 24a Control Panel Assembly On Off...
Страница 66: ...66 Figure 24b Control Panel Assembly Modulation...
Страница 68: ...68 Figure 25 Bishop Pilot Assembly...
Страница 72: ...72 NOTES...
Страница 73: ...73 NOTES...
Страница 74: ...74 NOTES...
Страница 75: ...75 NOTES...