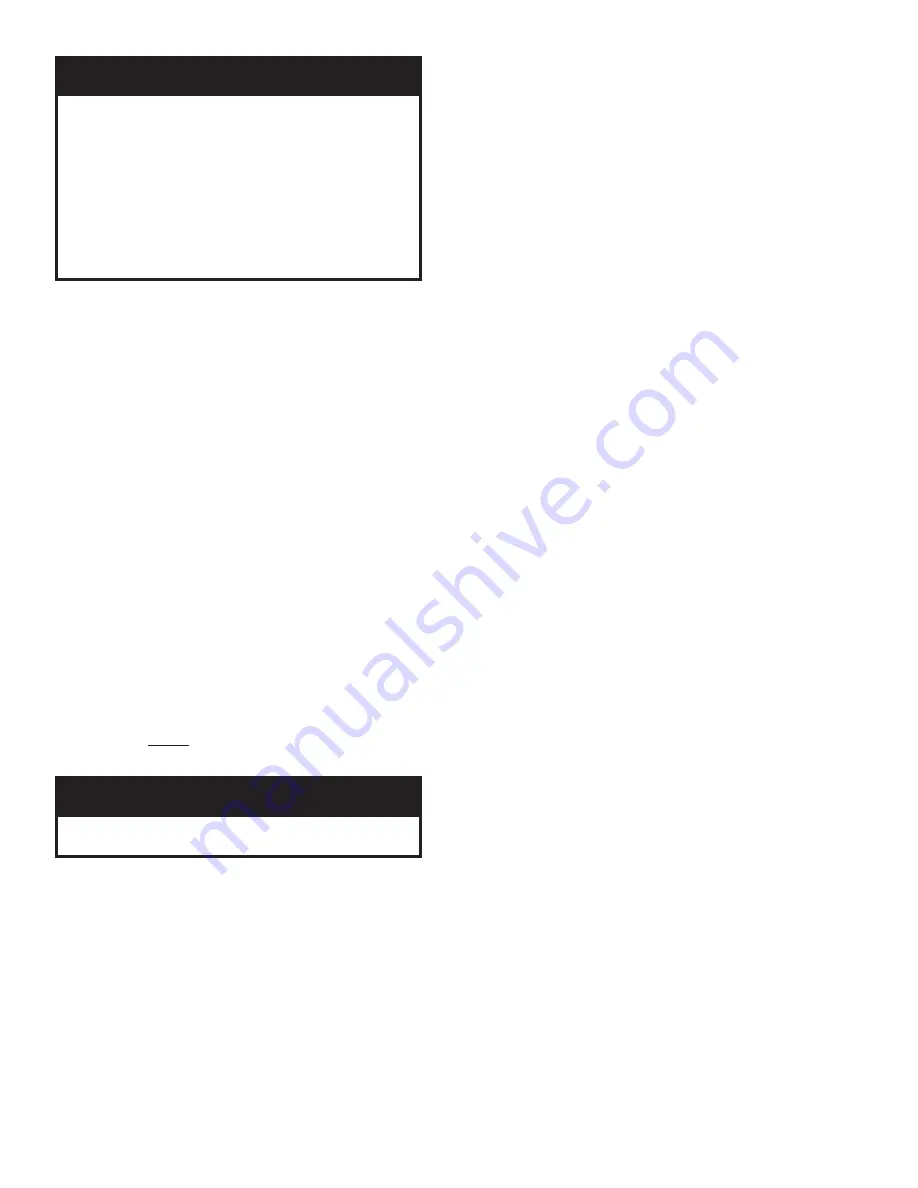
40
WARNING
The maximum operating pressure of this boiler
is 160 psig. Never exceed this pressure. This
boiler was supplied with a safety relief valve with
a pressure relief setting specified at the time of
purchase. The relief valve setting must be above
the maximum operating pressure of the system.
Consult Thermal Solutions if the desired system
operating pressure is above the safety relief
valve pressure setting. Do not plug or change
safety relief valve.
C.
Power the boiler
- Turn on electrical supply to the
boiler and circulation system at fused disconnect
switches. Turn on control circuit breaker inside front
jacket panel. Note that there is electrical power at
certain components even with the boiler operating
switch off. See wiring diagrams in Figures 9a-9c.
D.
Power the Circulators
- Turn system circulators on
and purge air from the boiler and system piping.
1. Confirm motor rotation on boiler and system
circulators.
2. Confirm that water flow switch is operating
properly.
E.
Pressurize the Fuel System
- Turn on gas supply to the
boiler gas piping.
1
.
Confirm that the supply pressure to the gas regulator
supplied with the boiler conforms to Table 3 for
maximum and minimum supply pressures.
2
.
Open the manual gas shut-off valves located
upstream of the gas regulator supplied with the
boiler. Do not open manual gas valve inside of
boiler jacket.
DANGER
Do not use matches, candles, open flames or
other ignition source to check for leaks.
3. Using soap solution, or similar non-combustible
solution, electronic leak detector or other approved
method, check that boiler gas piping valves,
regulators and all other components are leak free.
Eliminate any leaks.
4
.
Purge gas line of air.
5
.
Reset low gas pressure safety switch.
F.
Turn the boiler operating switch to the on position.
G.
Check Blower Rotation
- Remove air filter to expose
the fan blades.
1. Allow boiler to enter the sequence of operation.
2. While in Pre-Purge, position the flame control to the
test position.
3. Confirm proper blower motor rotation.
4. Shut boiler off and position the flame control back
to run. Reinstall air filter.
H.
Flame Safeguard Operation Check
- Turn boiler
operating switch to the on position.
1. Allow boiler to complete prepurge and trial for
ignition period. Once pilot flame is recognized
by controller, position flame control switch to test
position.
2
.
Look through the boiler sight glass and confirm that
pilot flame is blue and steady and that the flame
signal is steady and between 1.5 and 5.0 volts DC.
On some boiler sizes, the pilot flame may not be
visible. In these cases, confirm proper flame signal
(as indicated above.)
3. Adjust pilot gas regulator until proper pilot manifold
gas pressure is achieved per firetest report label.
Pilot flame should be blue with very little yellow.
4
.
Turn the boiler off, place flame control switch in
"run" position, and repeat Steps H.1 and H.2 at least
five times until reliable pilot ignition and signal is
achieved and confirmed.
5
.
With the pilot operating properly, allow boiler to
continue to trial for main flame. Confirm that the
flame control locks out on main flame failure.
6
.
Open the manual main gas shut-off valve located
inside the boiler jacket. Using the procedure detailed
in Step E.3, leak test gas piping and valves upstream
of the boiler main gas valve. Eliminate any leaks.
7
.
Reset flame safeguard and allow boiler to run
through prepurge, trial for pilot and trial for main
flame.
8. Confirm that main flame ignites smoothly.
9. Observe main flame and confirm that burner
element is evenly orange without flickering.
10. Observe flame signal and confirm signal is steady
and between 1.5 and 5.0 volts DC.
11. Using the procedure detailed in step E.3, leak test
gas piping and valves downstream of the boiler gas
valve. Eliminate any leaks.
Содержание EVO-1000
Страница 12: ...12 Figure 3 Sidewall Positive Pressure Venting Optional Figure 2 Sidewall Positive Pressure Venting...
Страница 13: ...13 Figure 4 Vertical Pressurized Venting...
Страница 15: ...15 Figure 5 Typical Negative Pressure Conventional Venting...
Страница 17: ...17 Figure 7 Vertical Air Intake Piping...
Страница 26: ...26 Figure 9a Standard UL FM CSD 1 Wiring Diagram on off EVO 500 2000...
Страница 27: ...27 Figure 9b Standard UL FM CSD 1 Wiring Diagram Modulation EVO 500 2000...
Страница 30: ...30 Figure 11 Modular System Horizontal Air Intake Piping...
Страница 31: ...31 Figure 12 Modular System Vertical Air Intake Piping...
Страница 32: ...32 Figure 13 Modular System Typical One Pipe Water Piping...
Страница 33: ...33 Figure 14 Modular System Typical Primary Secondary Water Piping...
Страница 34: ...34 Figure 15 Modular System Typical Primary Secondary without System Pump...
Страница 35: ...35 Figure 16 Modular System Typical Reverse Return Water Piping...
Страница 36: ...36 Figure 17 Modular System Reverse Return with System Pump Only...
Страница 37: ...37 Figure 18 Modular System Typical Primary Secondary with Reverse Return...
Страница 47: ...47 This Page Intentionally Left Blank...
Страница 48: ...48 Troubleshooting Guide B Troubleshooting Guide...
Страница 49: ...49 Troubleshooting Guide...
Страница 53: ...53 This Page Intentionally Left Blank...
Страница 54: ...54 Figure 19 Combustion Chamber Assembly...
Страница 56: ...56 Figure 20 Burner Assembly FRONT VIEW TOP VIEW...
Страница 58: ...58 Figure 21 UL FM CSD 1 Main Gas Train Assembly...
Страница 60: ...60 Figure 22a DB B DB B w POC Gas Train 500 750 Figure 22b DB B DB B w POC Gas Train 1000 2000...
Страница 62: ...62 Figure 23 Jacket Panels 4D 4J 4C 4B 4F 4I 4G 4E 4R 4K 4H 4J 4N 4M 4L 4Q 4A 4P 4P...
Страница 64: ...64 Figure 24a Control Panel Assembly On Off...
Страница 66: ...66 Figure 24b Control Panel Assembly Modulation...
Страница 68: ...68 Figure 25 Bishop Pilot Assembly...
Страница 72: ...72 NOTES...
Страница 73: ...73 NOTES...
Страница 74: ...74 NOTES...
Страница 75: ...75 NOTES...